Everything You Should Know About Stainless Steel Passivation
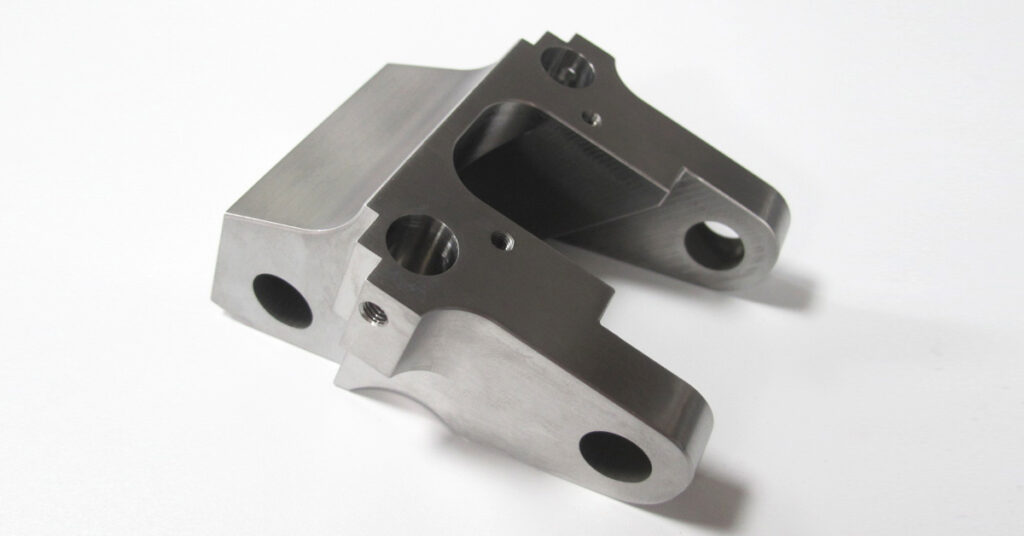
Passivation is a fundamental post-machining process for making corrosion-resistant steel parts and components. Stainless steel passivation creates a passive layer on the metal’s surface that prevents it from chemical reactivity.
This procedure eliminates contaminants like iron and dirt by producing a passive oxide layer on the stainless steel’s surface. However, various alloys and applications demand different passivation methods and techniques.
This guide discusses everything you need to understand about stainless steel passivation, its methods and techniques, benefits, and challenges of passivation. You’ll also learn helpful tips for effective stainless steel passivation. Read on to learn more about the topic!
Steel CNC Machining: A Comprehensive Guide
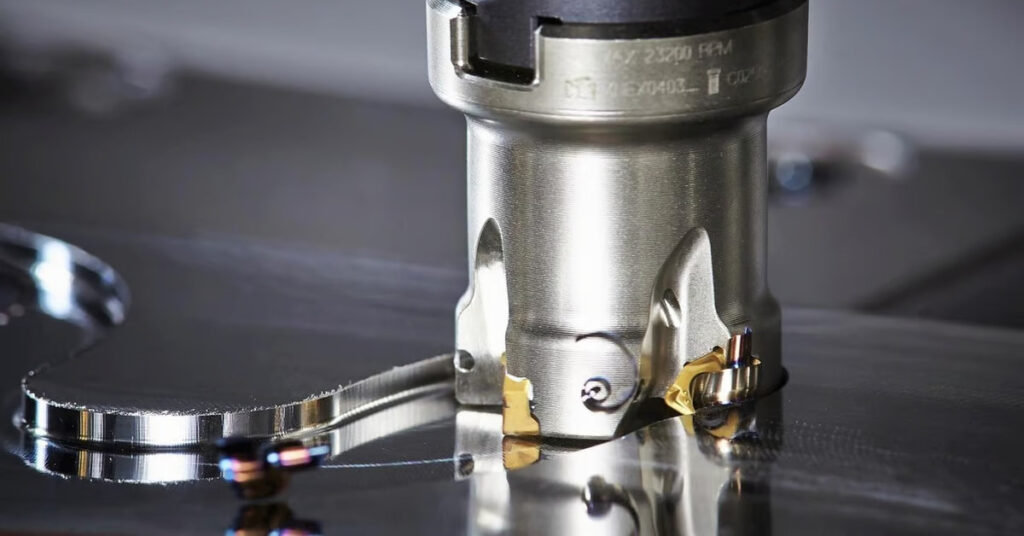
Steel is a good choice for various CNC machining operations because of its excellent machinability and homogeneity. It also offers strong workability, weldability, high ductility, and formability to fulfill any project’s specifications and is well-suited to your particular machining demands.
Steel has emerged as one of the more common industrial alloys for CNC machining projects due to its favorable physical qualities. The metal has a high tensile strength and excellent corrosion resistance, adding to the durability and part longevity of the product. This comprehensive guide explains all you need to know about steel CNC machining, including its surface finishes.
Engineering Tolerances: Definition, Types, and Fits
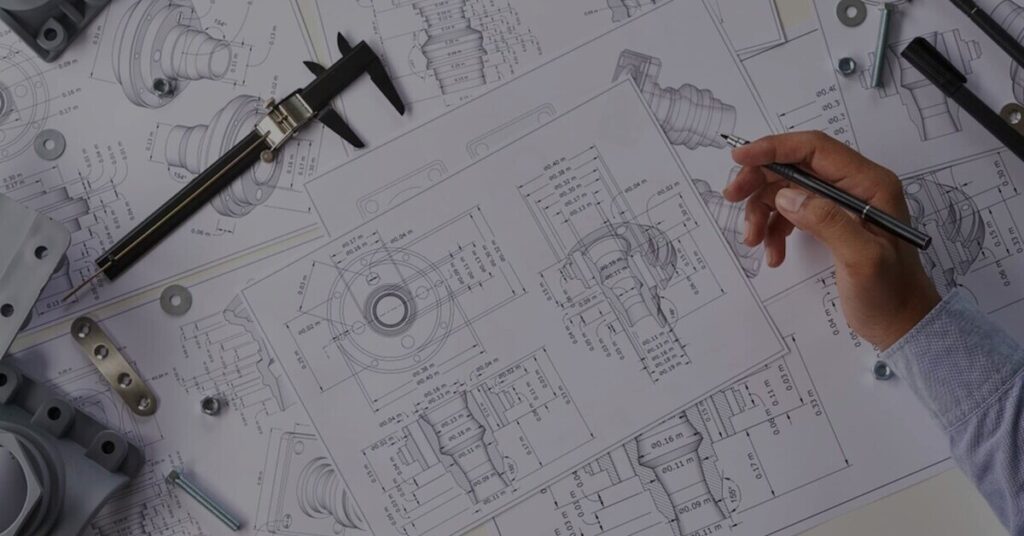
Tolerances establish the permissible deviation from the assigned dimensions or measured value in mechanical engineering. Manufacturers often use tolerances in product engineering to ensure the interchangeability of components in mechanical manufacturing.
A product may become unusable based on the design intent when the production parts’ dimension is not within the preferred tolerance limits since each fabrication process has a certain degree of inaccuracy. Therefore, it is pivotal to understand engineering tolerances and their types to achieve quality and usable products.
This article discusses what tolerance engineering is and its different types. You’ll also learn about fits and helpful considerations for part tolerancing. Let’s dive in!
Why Should Consider Wire EDM Cutting for Your Precision Project
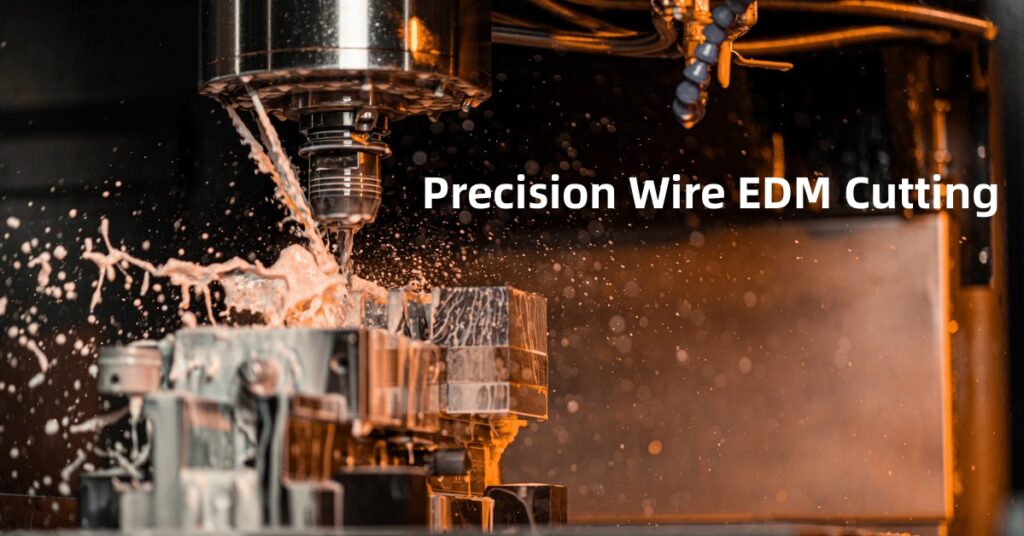
Wire Electrical Discharge Machining (EDM) emerges as a pivotal tool in precision machining, offering unparalleled accuracy and intricate design capabilities.
This article delves into the mechanics and essential components of Wire EDM, juxtaposing its advantages with limitations and drawing comparisons to Conventional EDM.
With insights into industries reaping its benefits and guidance on project-specific decision-making, this piece serves as an essential read for those exploring precision machining avenues.
Precision CNC Machining: Meaning, Advantages, and Applications
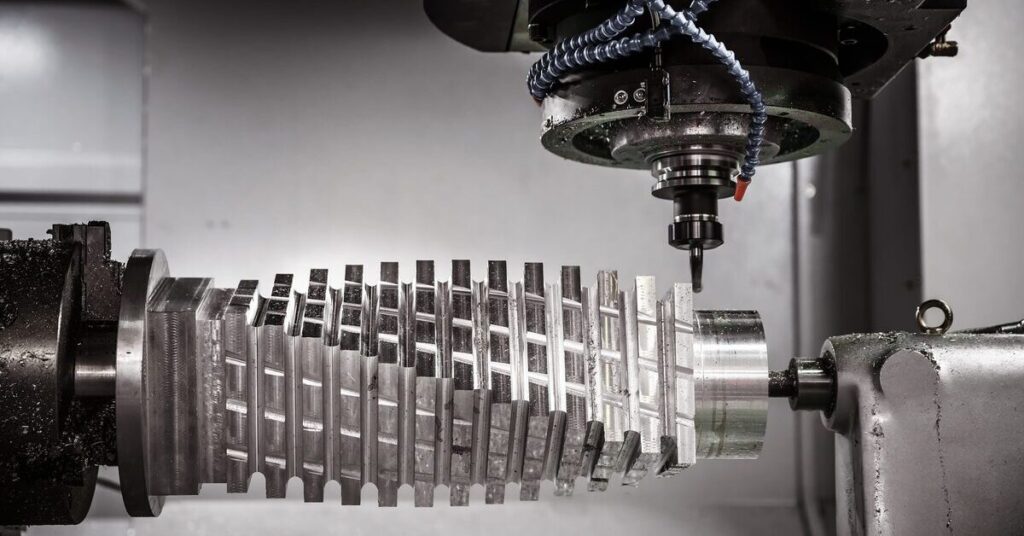
Our environment is surrounded by highly sophisticated technology that is advancing rapidly. In everyday life, we encounter several sophisticated elements, such as gears and components inside equipment, which makes us wonder what goes into making them.
For the most part, the answer to how these things are created is the same – precision CNC machining. CNC methods have been the foundation stone for modern businesses, making parts in an automated fashion at unbelievable production speeds.
Precision CNC machining has taken it further, increasing accuracy and streamlining the manufacturing process. This comprehensive guide will explain all the details about precision CNC machining, including its applications and processes.
Everything You Should Know About Deep Hole Drilling
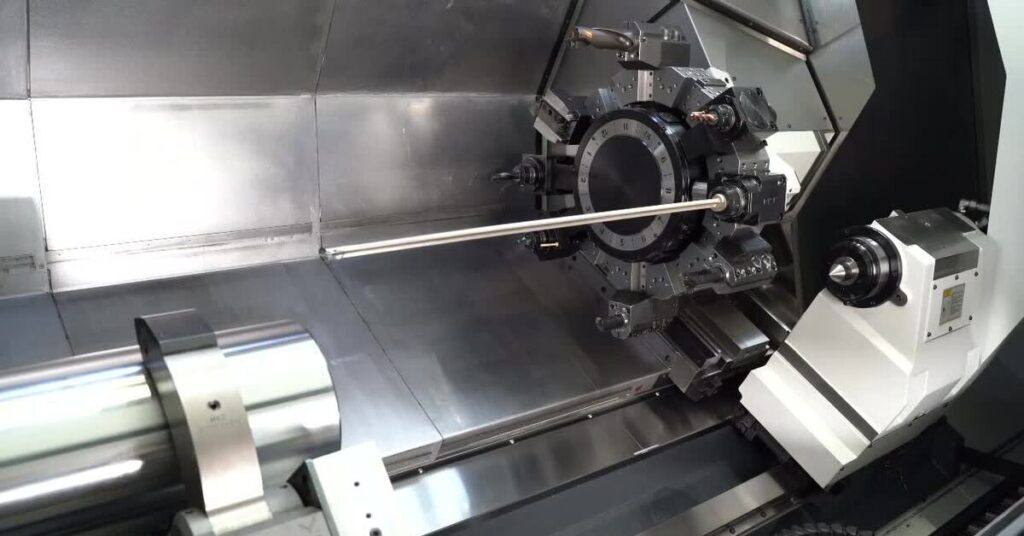
Deep hole drilling is a popular metal-working process in many fields, especially in producing firearms or heavy ordinances. This operation is perfect for most high-precision drilling projects because it provides highly accurate, repeatable holes with superior surface finishes. Therefore, it is crucial to understand everything about deep hole drilling to achieve the best results.
This guide discusses everything you need to know about deep hole drilling, its benefits, applications, and standard techniques. You’ll also learn helpful tips for effective deep-hole drilling. Let’s dive in!
The Ultimate Guide to Understanding Aluminum CNC Machining
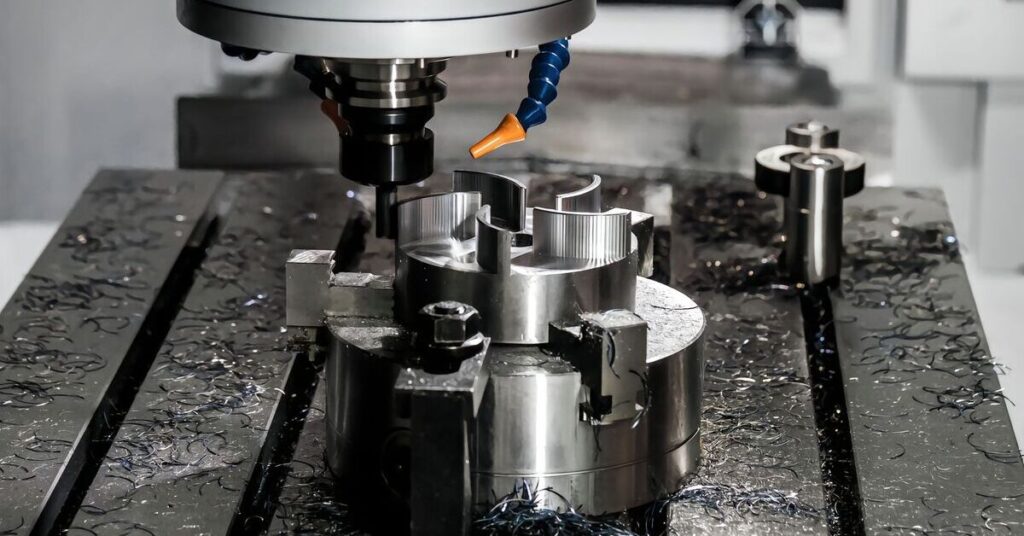
Aluminum is a non-ferrous metal commonly used in different applications. Manufacturers often utilize aluminum for various products because it is inexpensive, non-toxic, recyclable, and machinable, making it ideal for CNC machining. However, it is crucial to understand aluminum CNC machining to exploit its full potential of aluminum.
This article discusses aluminum CNC machining, the benefits of using aluminum for CNC machining, and the different grades of aluminum used in CNC machining. You’ll also learn about the standard aluminum CNC machining techniques and applications. Let’s get to it!
Safety First: Everything You Need to Know About Magnesium Machining
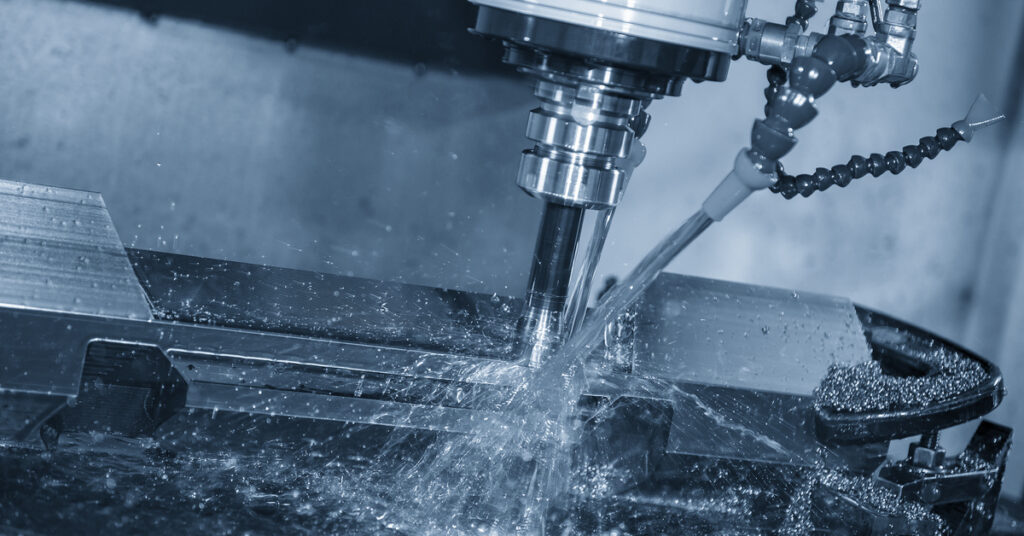
As industries increasingly turn to magnesium for its lightweight and robust properties, understanding the intricacies of safely machining this metal becomes paramount.
The highly flammable nature of magnesium, coupled with the hazards of its dust and chips, makes it a challenging material to work with.
Delve into this guide to uncover the essence of magnesium, the risks it presents during machining, and the quintessential safety protocols that can safeguard your projects.
Mastering CNC Lathe Parts: A Comprehensive Guide to 9 Essential Components
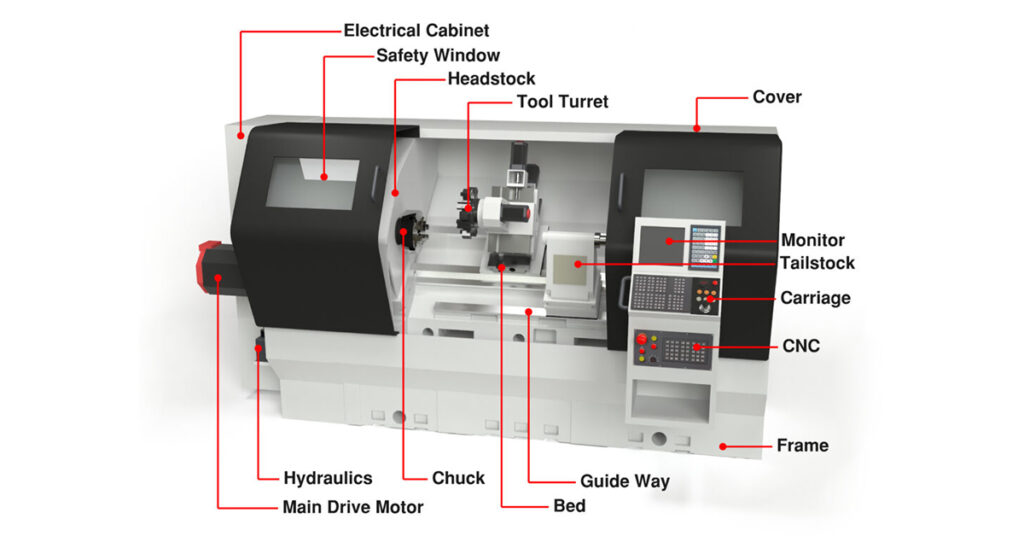
CNC lathe machines have revolutionized the manufacturing landscape with their precision and efficiency.
While many admire the end products these machines produce, few delve deep into their core.
In this guide, we’ll preview the 8 pivotal parts of a CNC lathe machine, provide proof of their significance, and give you a preview of their integral role in the machining process.
The Ultimate Guide to Understanding Centerless Grinding
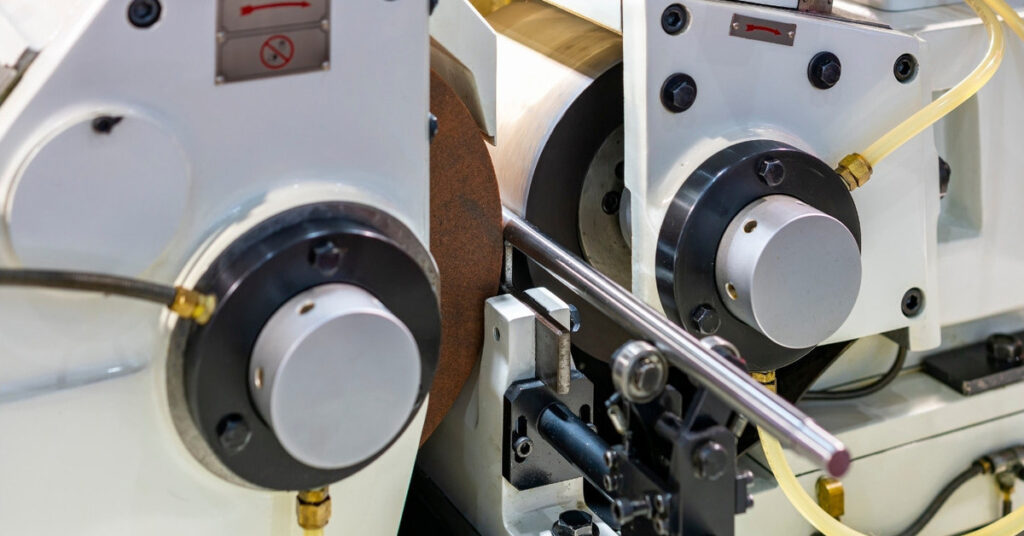
Centerless grinding is a versatile and adaptable technology ideal for machining cylindrical parts for different applications. Centerless grinding technology uses abrasive cutting to remove raw material from a workpiece.
Machinists use this cylindrical grinding technology to produce long, slender cylindrical components with consistent dimensional accuracy and finer surface finishes. However, it is essential to understand this technology to achieve the best grinding results.
This guide discusses the basics of centerless grinding, the core components of centerless grinders, how precision centerless grinding differs from traditional grinding, and its modern evolution. Keep on reading to learn more about the topic!
The Comprehensive Guide to Plastic Prototyping: Methods, Costs, and Considerations
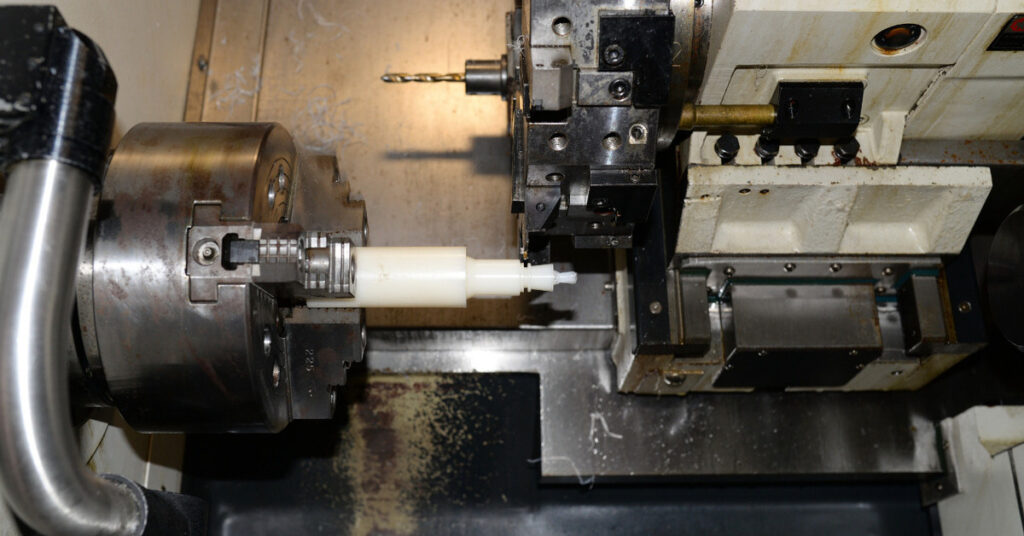
Plastic parts hardly get the deserved credit for the role played in product manufacturing despite being everywhere and having multiple applications in various industries.
Manufacturers and product developers often utilize plastic parts for different purposes, ranging from lids for coffee cups to computer keyboards, cable insulation, surgical gloves, and window frames. However, it would help to note that all plastic products started as prototypes.
This guide discusses the comprehensive guide to plastic prototyping. You’ll learn everything about the significance of plastic prototypes, plastic prototype development, methods for plastic prototyping, costs, and essential tips. Let’s get to it!
What’s the Difference? A Machining Guide to CNC Roughing and Finishing
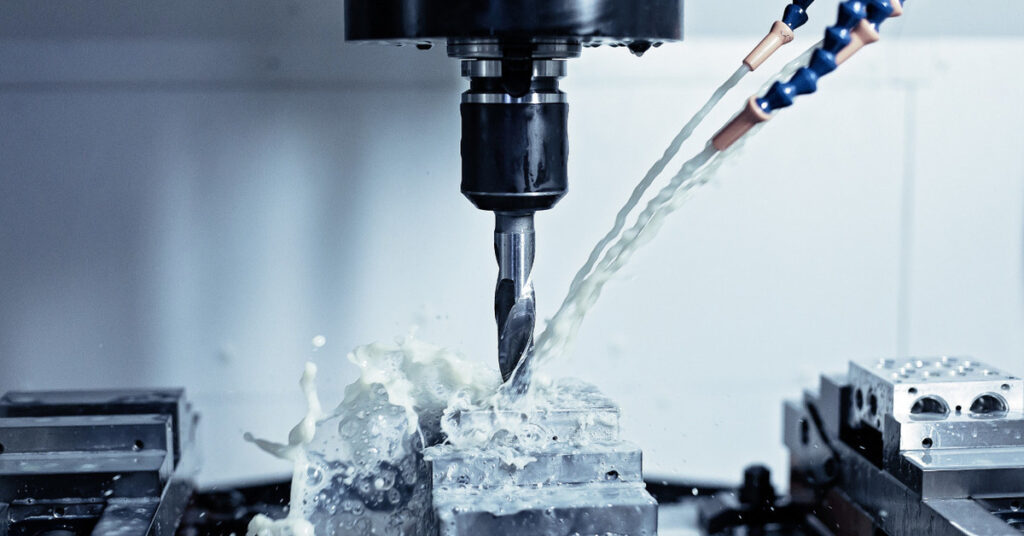
Welcome to the intricate realm of CNC machining, where rough and finish machining stands as pillars of precision, efficiency, and accuracy.
This guide delves deep into these two pivotal processes, aiming to demystify their integral roles in the industry.
Dive in as we uncover their distinct advantages and essential considerations when you’re in the market for top-notch machining services. Let’s embark on this insightful voyage to the core of CNC craftsmanship.
Everything You Need to Know About Gears Machining
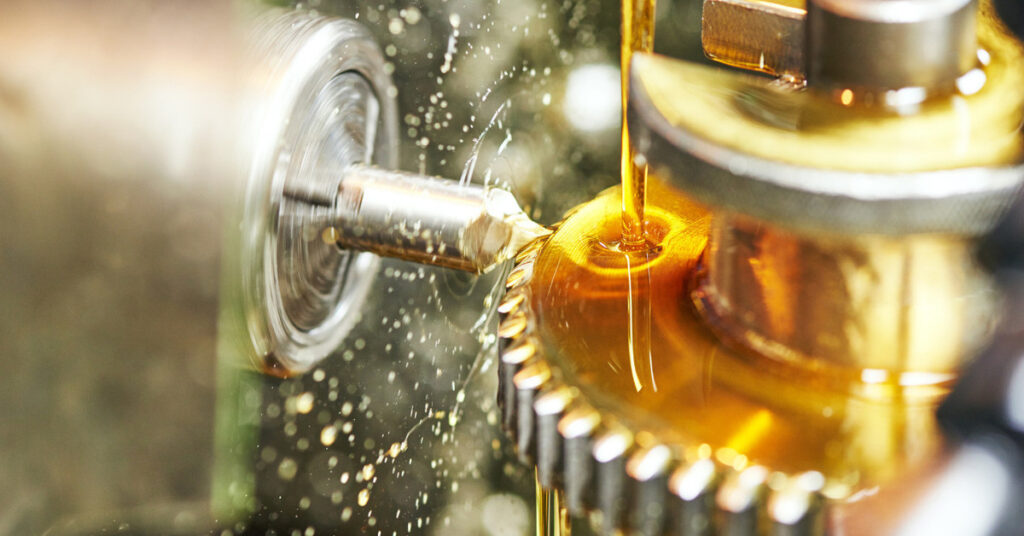
The concept of gears machining has been around for a while because they are among the oldest mechanical components still in use today. Gears offer several benefits in a wide range of applications. They are used in various products and industries, including automotive, aerospace, industrial, and more.
Gears can be created using techniques such as casting, forging, extrusion, powder metallurgy, blanking, and gear milling. However, the machining process is crucial in achieving the final gear size, shape, and surface smoothness.
This distinctive guide will explain all you need to know about gear machining, including its importance. We will delve into the various methods for gears processing, including important tips for material selection.
Copper CNC Machining: Everything You Want to Know
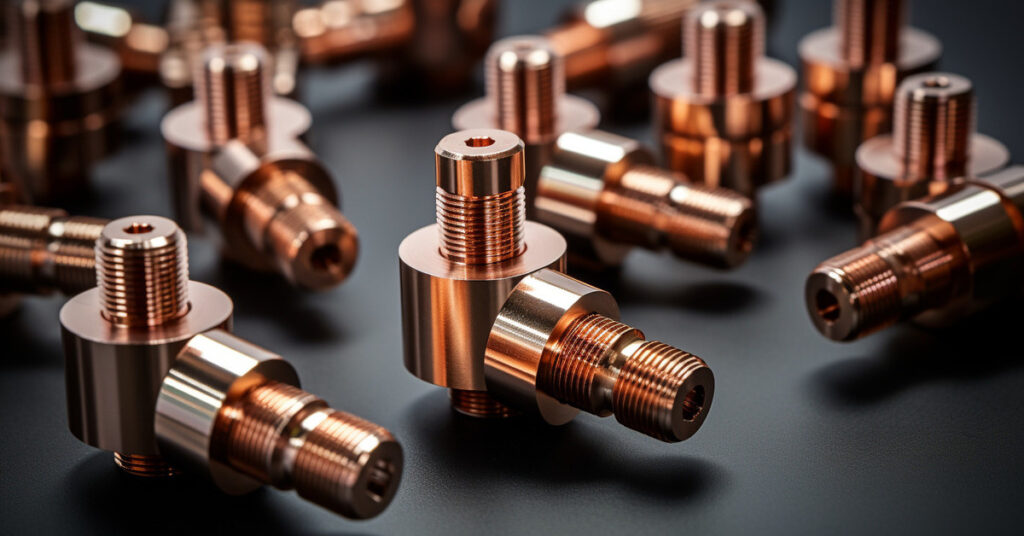
Copper is a multipurpose metal and one of the oldest metals commonly used in modern mechanical engineering—engineers utilize copper materials due to its exceptional characteristics. Most especially, copper and its alloys are valuable for different applications due to their remarkable thermal and electrical conductivity and excellent corrosion resistance.
Copper CNC machining is one of the most resourceful and precise metal machining processes industries use to create copper parts. This specialized precision machining provides high precision, compatibility, and accuracy in handling various parts’ high demands. However, it is essential to examine the factors associated with copper parts machining to determine the ideal one for your copper machining projects.
This guide explores everything you want to know about copper CNC machining, different grades of copper, advantages, and challenges of machining copper. If you also want to learn about the key considerations, machining methods, and typical applications of copper-machined parts, this guide is for you!
Guide to Small Batch CNC Machining: Tailored Manufacturing Solutions
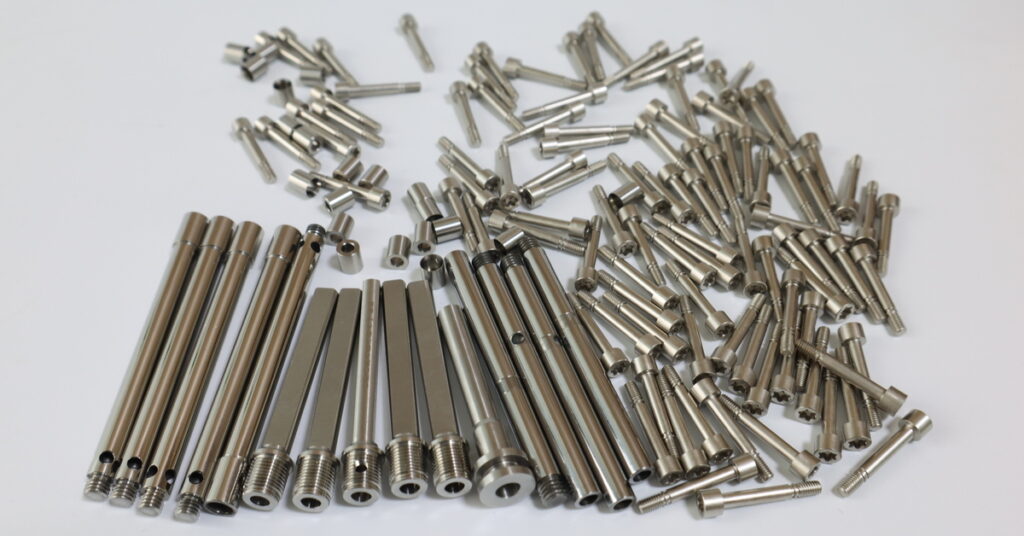
Welcome to the precision path of small batch CNC machining! In this rapidly evolving manufacturing landscape, one aspect that stands out is the increasing relevance of small batch production.
In this blog, we’ll explore this important facet of modern manufacturing and dive into how small batch CNC machining transforms how we produce goods.
Boring Machining 101: Everything You Need to Know
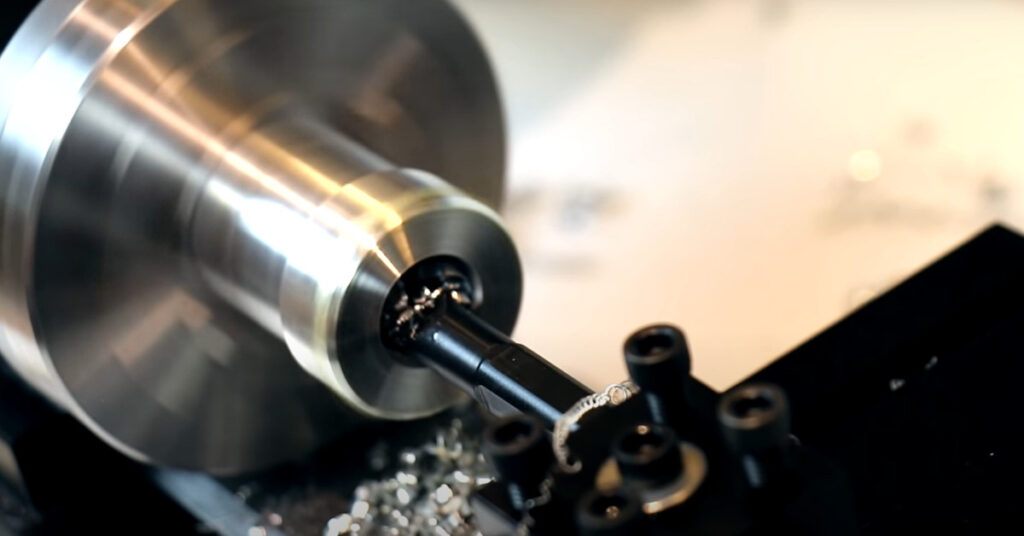
Boring Machining is a precise and versatile method used in manufacturing industries to enlarge a hole that has already been drilled or cast.
This technique is employed when an application requires a hole of accurate size and finish, often achieved with single-point cutting tools or a boring head containing several such tools.
Boring is an operation that enlarges a hole and improves its concentricity and surface finish.
Get the Perfect Finish: A Guide to Metal Surface Finishing
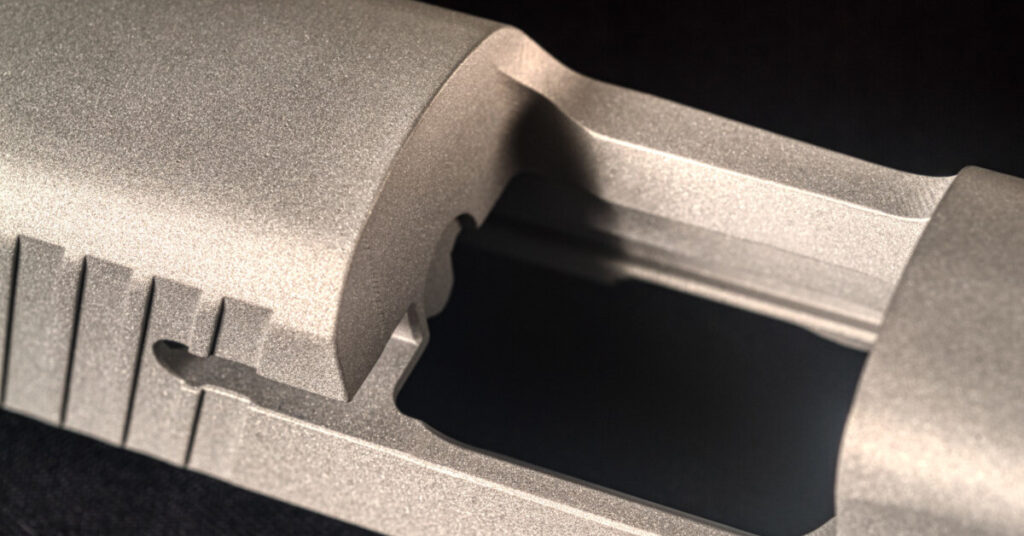
Are you seeking to enhance the performance or appearance of your metal components?
Metal surface finishing is an essential part of the manufacturing process. It helps to protect metals from corrosion and can even add aesthetic appeal. From standard methods like bead blast and powder coating to more specialized procedures such as anodizing and plating, metal surface finishing can provide various benefits depending on the application.
In this blog post, we’ll explore the benefits and common types of metal surface finishing. By the end of this post, you will better understand how metal surface finishing can help protect and enhance your metal parts. So let’s get started!
A Comprehensive Guide to Brass CNC Machining
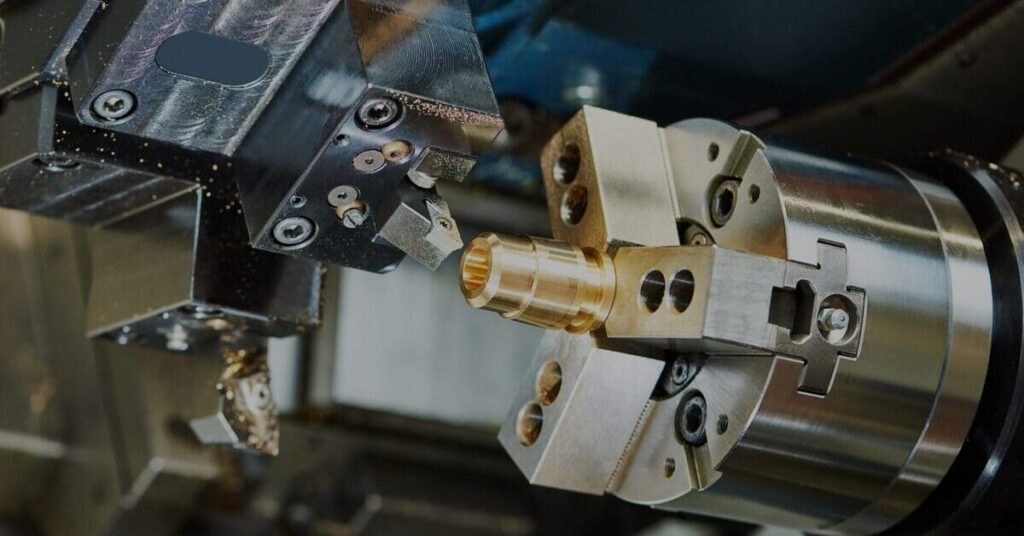
Brass is a metal alloy of copper which used across various industries, such as electrical, plumbing, and medical. Its excellent mechanical properties, such as corrosion resistance and low friction point,make CNC machining an excellent option for manufacturing parts using this alloy.
Brass is one of the easiest materials to machine due to its high machinability, good ductility, flexibility, and high feed rate. CNC machining brass produces quality brass components with extreme precision and aesthetic surface finish. It facilitates the production of parts like light fixtures, pipes, fittings, flare fitting, gears, etc.
What other properties make brass excellent for CNC brass machining? What are the commonly used brass grades for brass CNC machining? Which surface finish is ideal for use when CNC machining brass? Read on as we answer these questions while explaining CNC machining Brass in more detail.
Acrylic CNC Machining: Everything You Need to Know
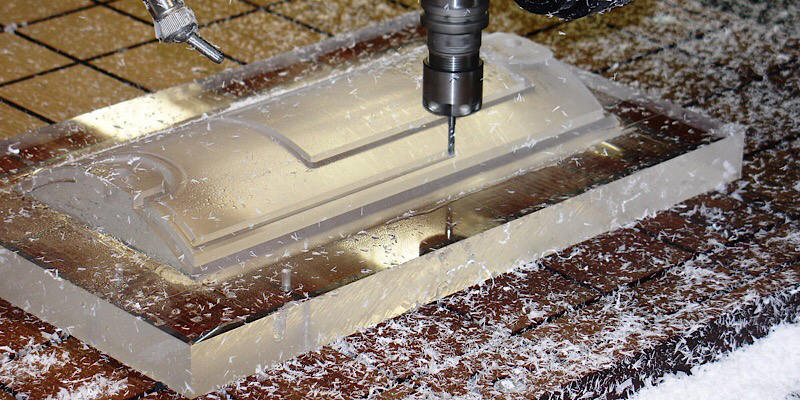
Acrylic, known chemically as plexiglass, has excellent optical clarity, strength, and rigidity. Due to its high transparency, manufacturers use it heavily as a glass replacement. Although many processes are used for acrylic production, acrylic CNC machining is the most common.
CNC machining acrylic leads to the production of acrylic parts with highly accurate shapes and sizes. It does this by using optimal force during the cutting process, which helps prevent damage to acrylic material while speeding up the process. Rough-cut lathes and cut mills are the two major machines used by manufacturers to cut acrylic.
So, how is Acrylic CNC machined? What are the properties of this plastic? Are there advantages of using acrylic for parts over other transparent plastic materials? Keep reading as we answer these questions and give you an in-depth understanding of CNC acrylic machining.
PEEK Machining: A Quick Guide to Machining PEEK
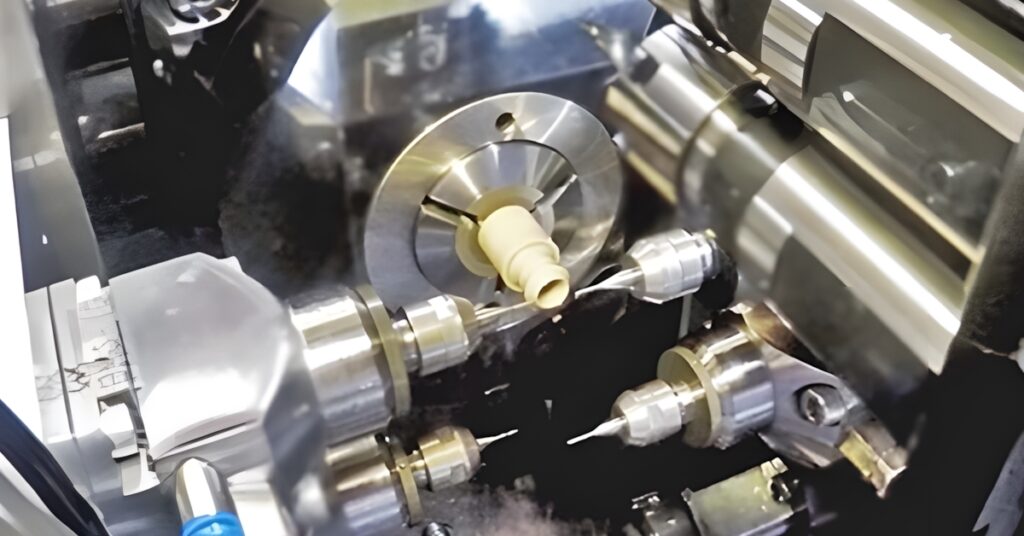
PEEK is a well-known thermoplastic polymer found in various objects, such as medical implants and insulations for electric cables.
The popularity of PEEK stems from its excellent mechanical properties and high resistance to corrosive substances products. Furthermore, its high melting point makes it suitable for subtractive processes such as CNC machining.
This article guides you through PEEK properties, components, and industry applications. Here, we’ll share tips to help you get the best from your PEEK machining process. Let’s go right to it!
6 Things You Need to Know About Plastic CNC Machining
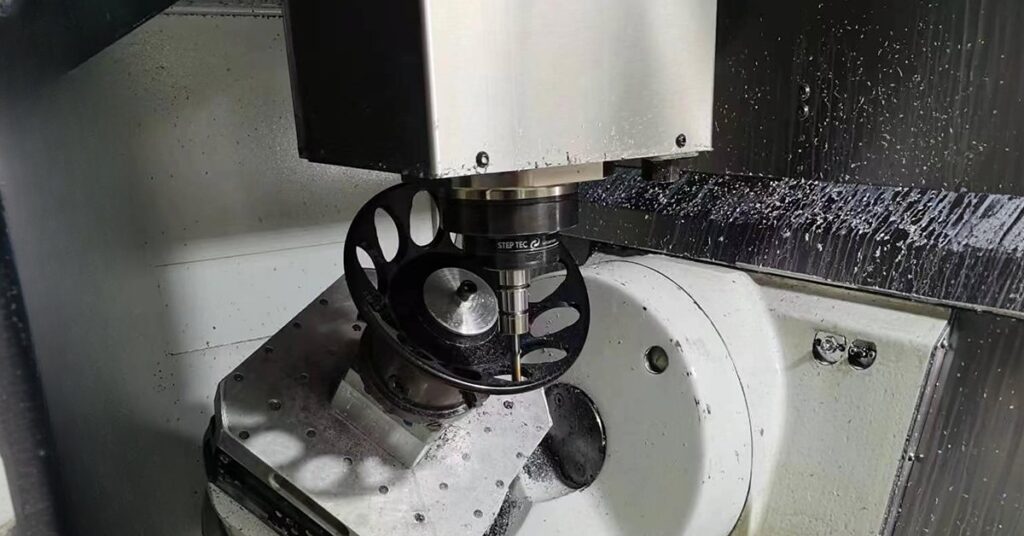
CNC machining is a common rapid prototyping manufacturing process due to its accuracy, precision, compatibility with complex design, etc. It is a subtractive process that involves a computer controlling a CNC tool via techniques such as milling, turning, etc., to remove part of a workpiece used to form the required product.
CNC machines are compatible with many materials such as metals, plastics, and wood. However, With the telling development of polymer plastics, many plastic products manufacturers now use plastic CNC machining, which involves manufacturing plastic products using different CNC machine techniques.
There are many things to plastic CNC machining. Therefore, this article will introduce seven essential things you need to know about the process.
Mastering the Concept of Thread Machining
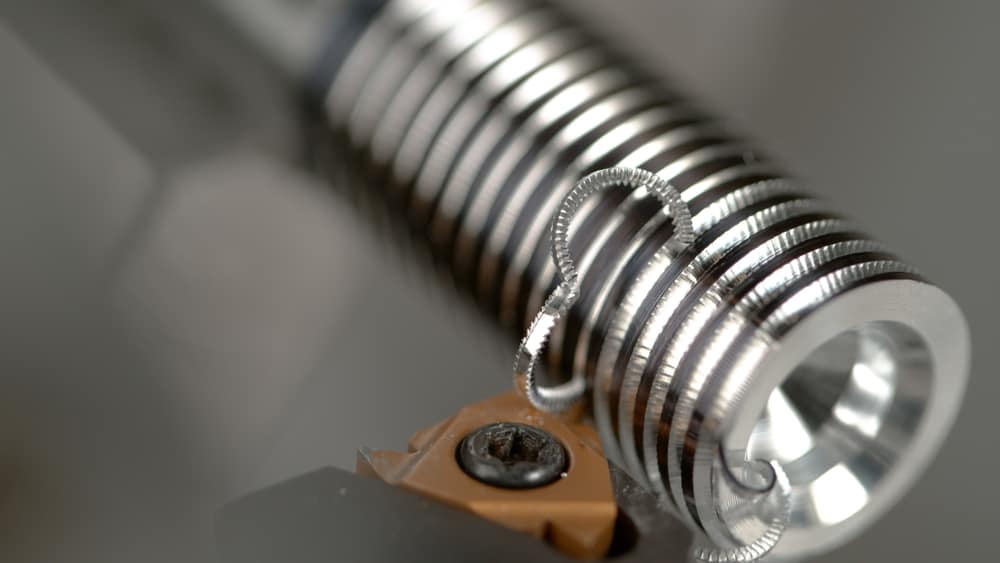
With a rise in complex and intricate assemblies in the world of engineering, the role of threads has become indispensable. Everywhere from your water bottle to an engine assembly, threads are existent.
Thus, for you as our reader, we would deliver the concept of thread machining as comprehensively as possible in this article. This information would be vital for you to choose your next CNC machining service provider wisely.