Custom Micro Screws: 7 Factors to Consider for Your Precision Projects
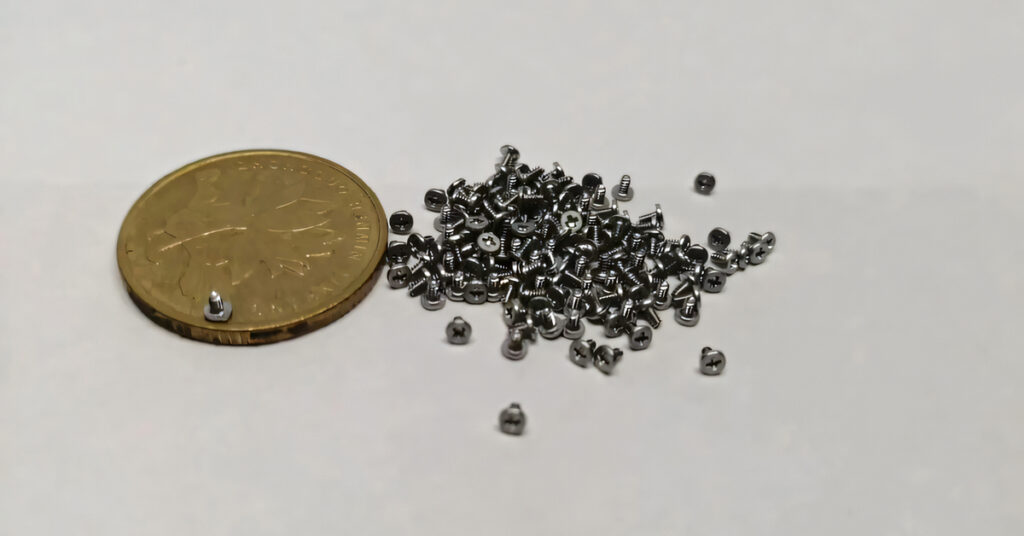
When executing precision projects, the choice of fasteners can make or break the outcome. Among the plethora of options, custom micro screws stand out as the cornerstone of many high-tech assemblies.
In this guide, we’ll explore seven critical factors that demand your attention when incorporating custom micro screws into your precision projects.
From material selection to understanding supplier capabilities, AT-Machining insights ensure that your project’s integrity is never compromised.
How Does CNC Programing Work to Improve Custom Machining Results?
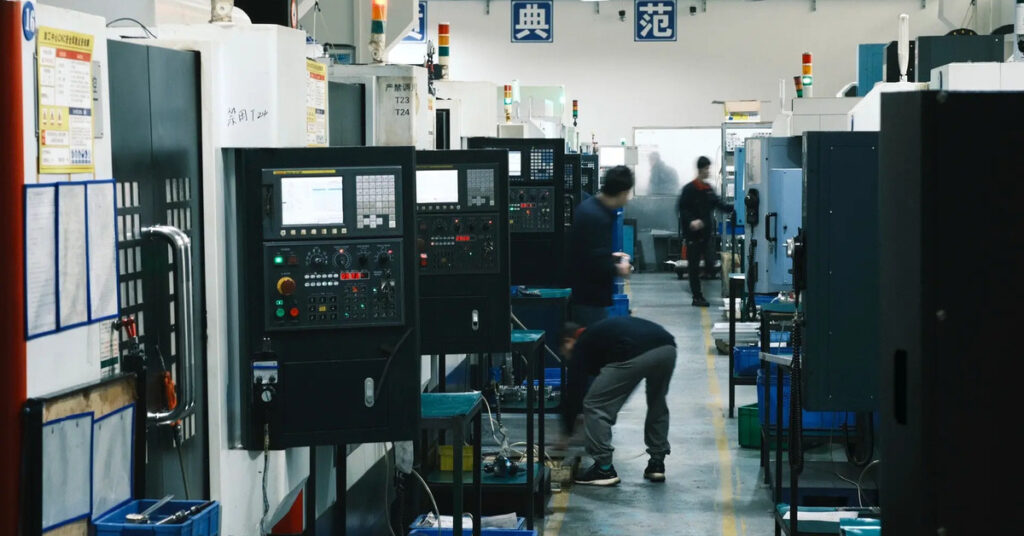
Achieving precision in manufacturing processes often involves the use of advanced technologies. One such technology that plays a crucial role is CNC (Computer Numerical Control) programming.
CNC programming is the key to unlocking the full potential of CNC machines, enabling businesses to produce intricate and accurate components with efficiency and consistency. It is the code that breathes life into complex designs. It guides machines to meticulously shape raw materials into intricate parts that are useful in several industries.
But what exactly is CNC programming, and how does it play a vital role in custom machining? This article answers all the important questions. We will explore CNC programing intricacies, applications, and the immense value it brings to the custom machining process.
Everything You Should Know about Custom Motorcycle Parts Manufacturing
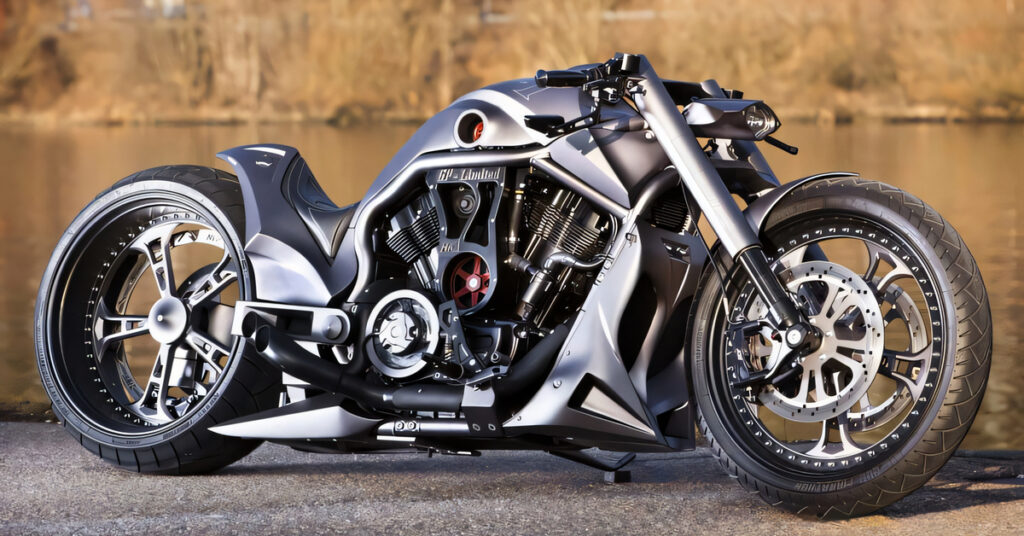
Welcome to the intricate world of custom motorcycle parts manufacturing, a realm where artistry and engineering seamlessly intertwine.
This blog offers an in-depth look at the entire process, from the imaginative design of custom parts to the meticulous selection of materials and advanced manufacturing techniques.
Prepare to delve into the precision and challenges of creating bespoke motorcycle components, culminating in the essential guide to selecting a trustworthy manufacturer.
Understanding Transmission Shafts: Types, Materials, Design, and Manufacture
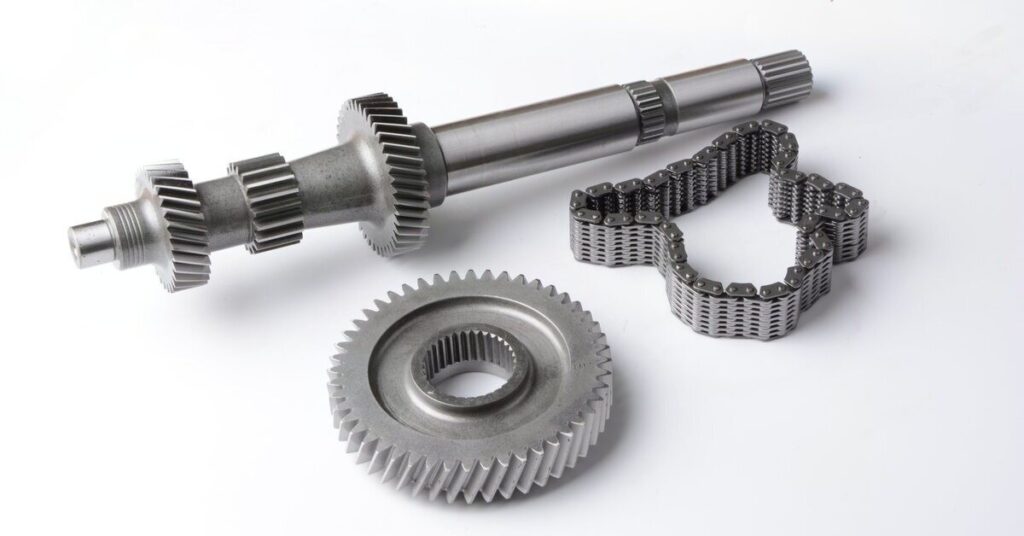
Shafts are versatile engine components with varying applications across industrial manufacturing, consumer products, transportation, and mining industries. Transmission shafts are one of the commonly used shafts.
Transmission shafts have a circular cross-section and are responsible for transferring power or motion within engines or machines. Transmission shafts transfer power from one part producing power to another which receives it. Hence, transmission shafts are core to all rotating machinery.
This guide provides an in-depth discussion of transmission shafts meaning, types, manufacturing processes, and materials used. You will also learn helpful transmission shaft design considerations by reading to the end. Let’s get to it!
How to Select the Perfect Custom Screws for Your Project: A Comprehensive Guide
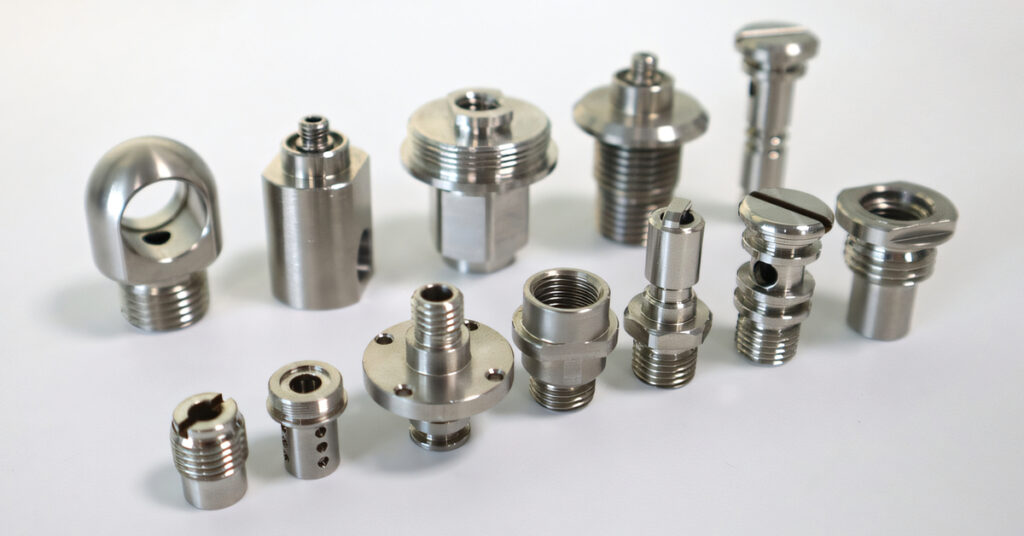
Selecting the perfect custom screws is crucial for the success of any project.
This guide offers a deep dive into materials, sizes, and precision manufacturing, providing expert insights to inform your choices.
Discover how the right screw can enhance your project’s durability, functionality, and efficiency in just a few well-informed steps.
Everything You Should Know About Slot Milling in Machining
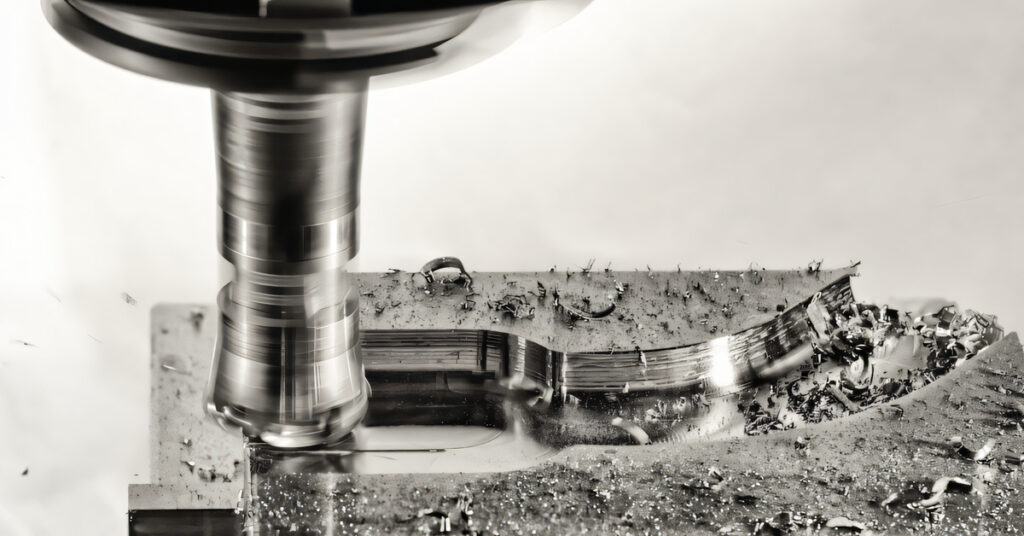
Machining processes such as CNC milling are central to the modern manufacturing industry, offering reliable and flexible production techniques with unique capabilities. Slot machining is one of the most versatile and widely used processes in machining grooves with limitless shapes and sizes.
This process uses various slotting tools to make precise pockets, grooves, or slots in different components, meeting strict quality standards and tight tolerances. Understanding the slot milling process is advisable to fully exploit its vast benefits.
This guide provides a detailed introduction to slot milling technology and its techniques. Read on to learn more about best practices for optimal slot milling!
A Comprehensive Overview of Galvanization Metal and Its Applications
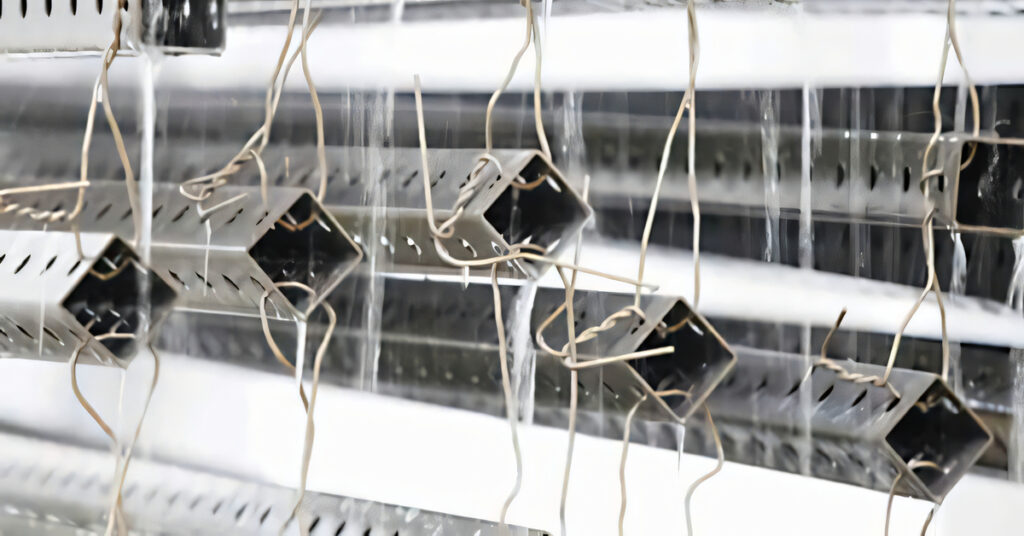
By means of galvanization, a zinc coating is applied to the exterior of iron or steel. By functioning as a sacrificial element, the surrounding zinc coating safeguards the underlying steel or iron. As a result, it potentially prolongs the operational lifetime of metallic components.
Galvanized metal provides sufficient protection against corrosion and damage and ensures a prolonged lifespan. In addition, galvanized steel and iron are compatible with various , including CNC machining and sheet metal fabrication. This makes galvanization a standard procedure in the manufacturing industry.
This article addresses fundamental questions regarding galvanization metal. We’ll cover its definition, intended purpose, and how galvanization enhances metal components.
Aluminum Injection Molds in Plastic Manufacturing: A Complete Guide
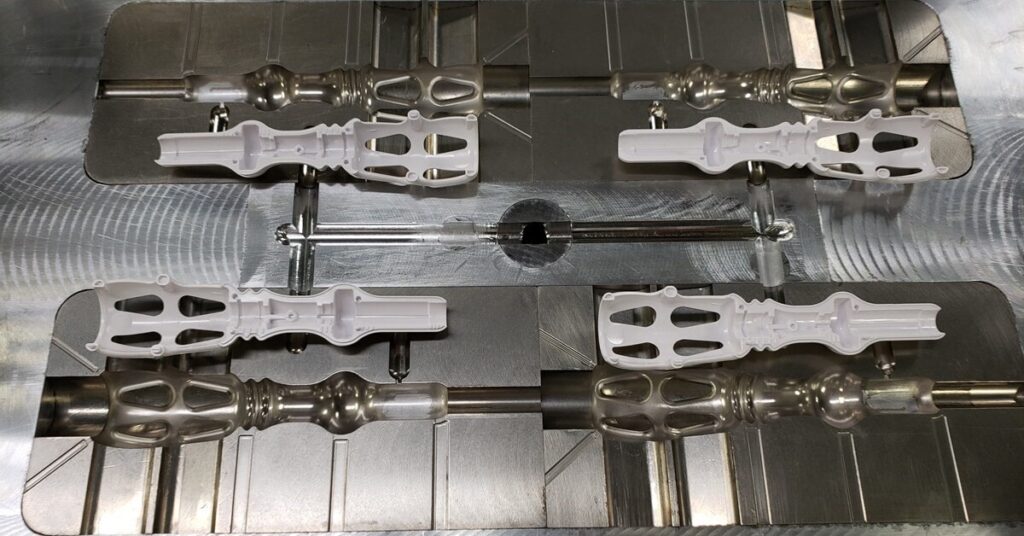
Conventional steel molds have long been the mainstay for mass production of plastic parts. However, with increasing demand for smaller production runs and faster turnaround times, aluminum injection molds have emerged as a compelling alternative.
Aluminum injection molds have gained favor among manufacturers seeking a balance between cost-effectiveness, product quality, and production speed. Advances in aluminum alloys have significantly enhanced their strength and hardness, making them suitable for longer-lasting molds. This extends their applicability beyond plastic prototyping and bridge tooling to full-fledged production runs.
This article delves into the details of aluminum injection molds, exploring their advantages, key features, and applications. We will also provide a design guide to help you get superior aluminum molds.
Everything You Should Know about CNC Engrave
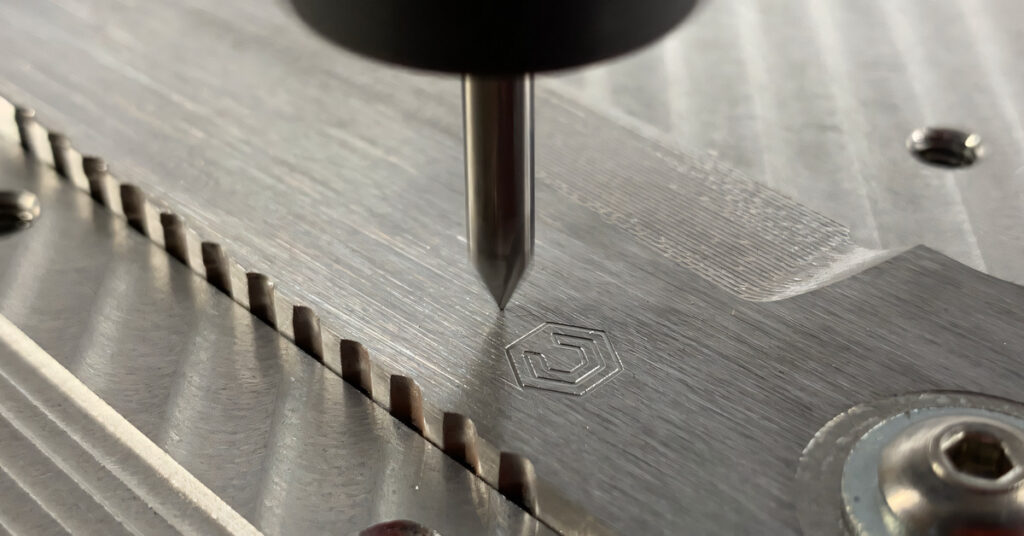
Ever wondered how intricate designs are etched into materials with unmatched precision?
Welcome to the world of CNC engraving, a fusion of art and technology. In this comprehensive guide, we delve into the nuances of CNC engraving, from its fundamental principles to advanced applications. Discover how AT-Machining harnesses this technology to transform your projects, ensuring precision and quality that stand out.
Get ready to explore everything you should know about CNC engraving, a technique that’s reshaping the manufacturing landscape.
PVD Coating Explained: Benefits and Applications in Modern Industries
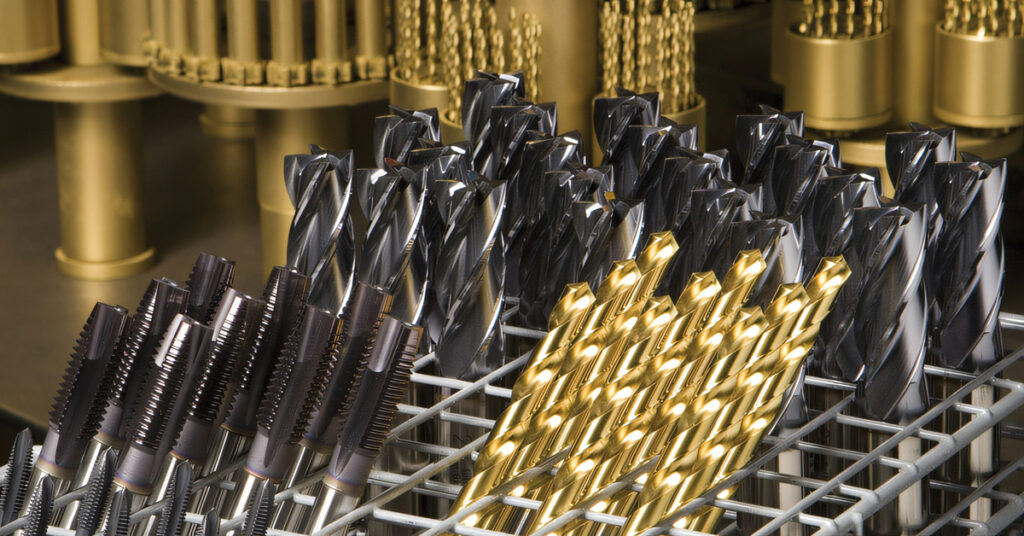
Since its initial discovery, Physical Vapor Deposition (PVD) coating has discovered various new applications. This process was Initially explored for military purposes to enhance cannon durability and minimize spin in ballistics.
The PVD coating technology involves altering the molecular properties of a metal’s surface by depositing thin films of materials on a part’s surface. The distinctive blend of appearance and functionality establishes this process as a unique element in metalworking.
This guide takes you through the PVD coating process, detailing its key benefits and applications. You will also learn the differences between PVD and other coating methods and how you can get the best from this process.
The Ultimate Guide to Tolerance Press Fit: What You Need to Know
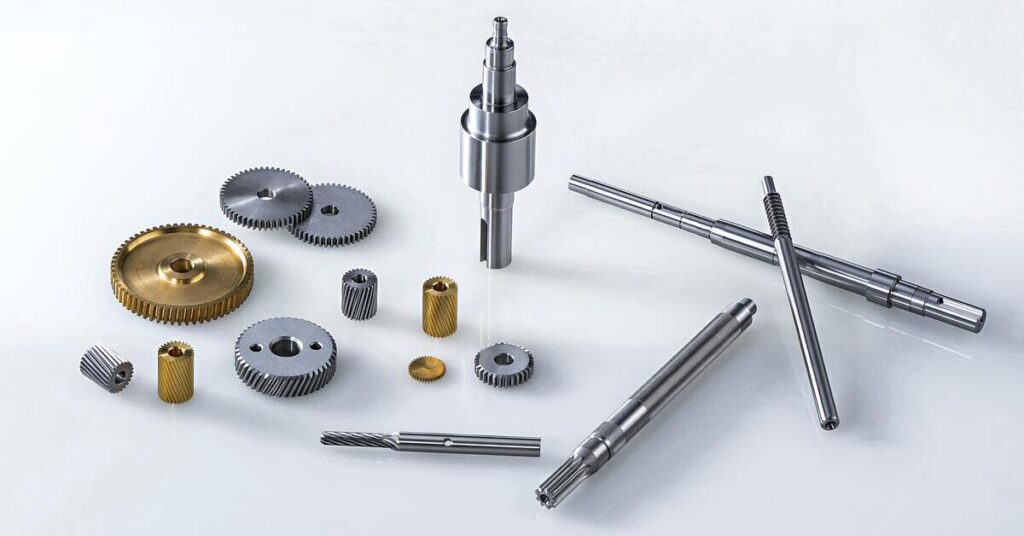
In mechanical engineering, tolerance press fit is the permissible deviation from the assigned dimensions or nominal size of mating parts. Tolerances are crucial in engineering fits to ensure two components of an assembly slide freely into each other.
Besides, tolerances define the allowable range of measurements for two parts in an assembly. However, it is essential to understand tolerance in press-fit design to ensure the reliability of the assembly.
This article discusses everything you need to learn about tolerance in press fit, factors influencing tolerances in press fits, calculations for press fit tolerances, and practical tips for optimal tolerance in press fit design. Read on to learn more about the topic!
Medical Device Manufacturing: Everything You Need to Know
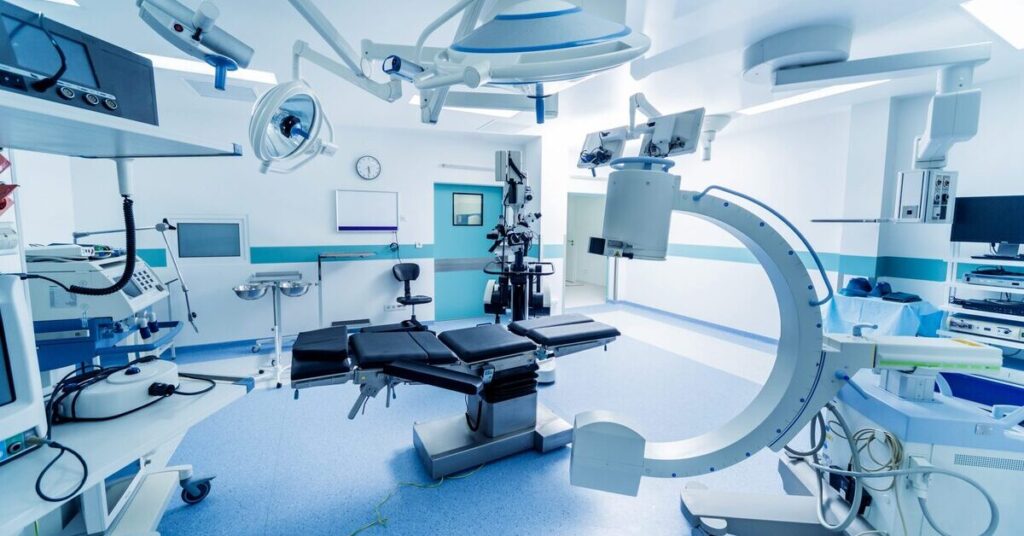
This article provides a comprehensive overview of medical device manufacturing, including key processes like CNC machining, 3D printing, injection molding, and casting.
It covers design, prototyping, materials selection, quality control, regulatory compliance, and cost management considerations. Specific examples illustrate the precision and customization enabled by modern manufacturing technologies.
The article highlights the critical factors contributing to developing safe, effective, innovative medical devices. Read this article to learn everything you need about Medical Device Manufacturing!
CNC Fixture: Types, Applications, and Design Tips
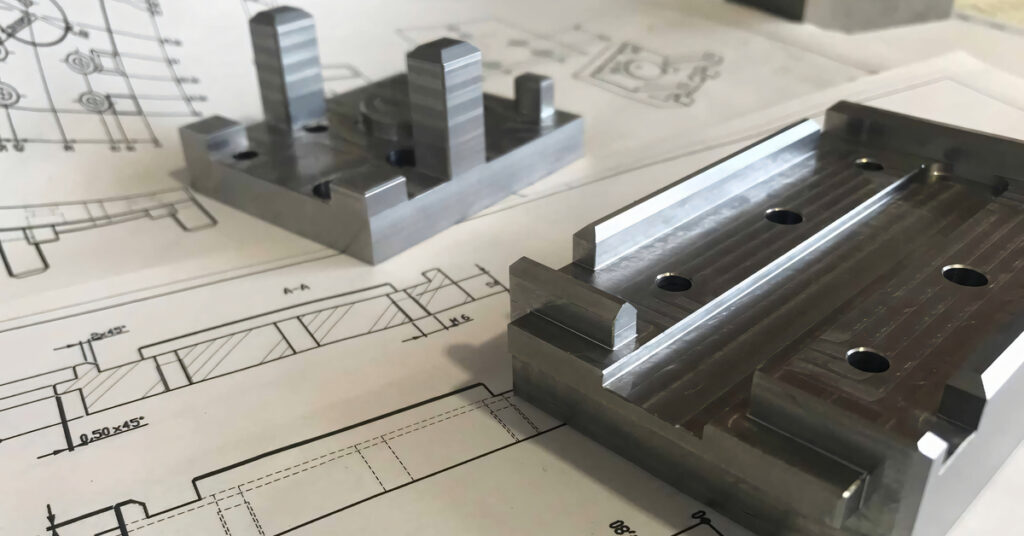
CNC fixtures are essential tools that play significant roles in CNC machining, allowing quicker operation and production of precise parts according to design specifications. The appropriate use of a CNC fixture guarantees coherence and interchangeability in CNC machining processes.
This allows you to meet the demands of your machining project with no human effort. Although these tools are of different types and have diverse uses, it is essential to understand the types of CNC fixture and their use to identify the right one for your project.
This guide provides a comprehensive overview of CNC fixtures and types. You’ll also learn about helpful CNC fixture design considerations in this article. Read on to learn more about the topic!
4-Axis CNC Machining: A Comprehensive Guide
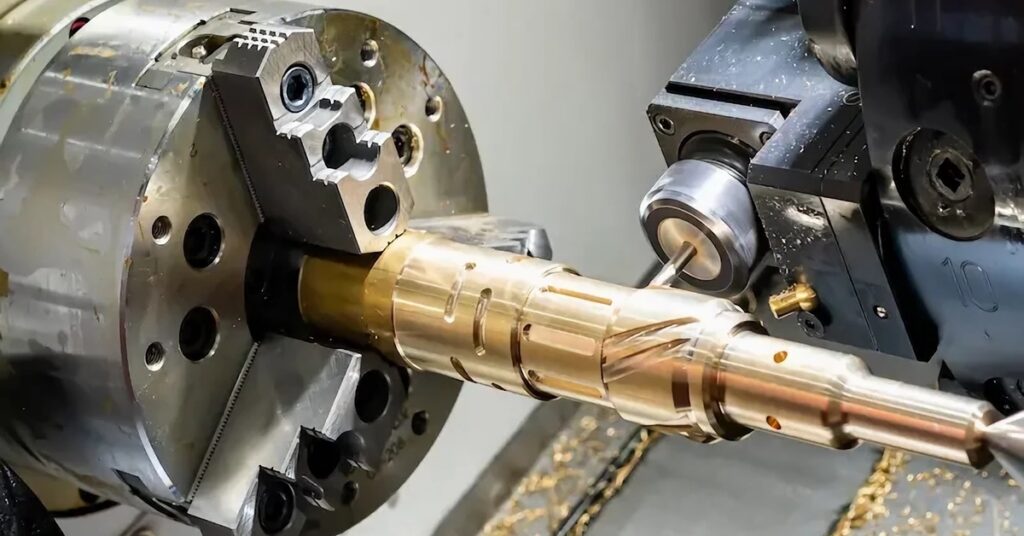
In this innovative era of automation in product manufacturing, 4-axis CNC machining offers reliable machining capabilities across various industries. It is an economical manufacturing process with greater machining flexibility and efficiency. Therefore, manufacturers utilize 4-axis machining as a means to eliminate human errors, ensuring tight tolerances in CNC part machining.
In this guide, you will learn everything about 4-axis CNC machining, including its basic process, advantages, and limitations. You’ll also learn the comparison between 3-, 4-, and 5-axis machining. Read on to learn more!
CNC Plastics: Choosing the Right Plastic for Your Project
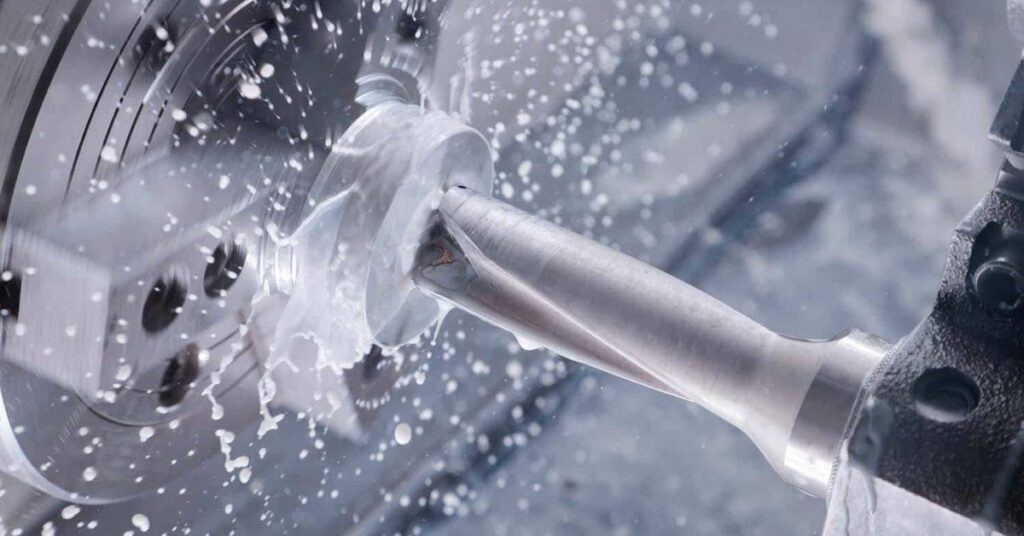
CNC plastics are indispensable to the modern manufacturing industry. Each machining plastic offers unique mechanical properties that make it suitable for either prototypes, engineering models, or end-use products. These plastics are practical alternatives to metals for a wide range of applications.
With an extensive list of plastics to choose from, it is crucial to select one with the right properties for the intended applications and industry. Therefore, you must understand the various properties of the available plastics in the market.
This guide discusses everything you should know about CNC plastics. You’ll also learn helpful tips to consider during material selection.
Everything You Should Know About Stainless Steel Passivation
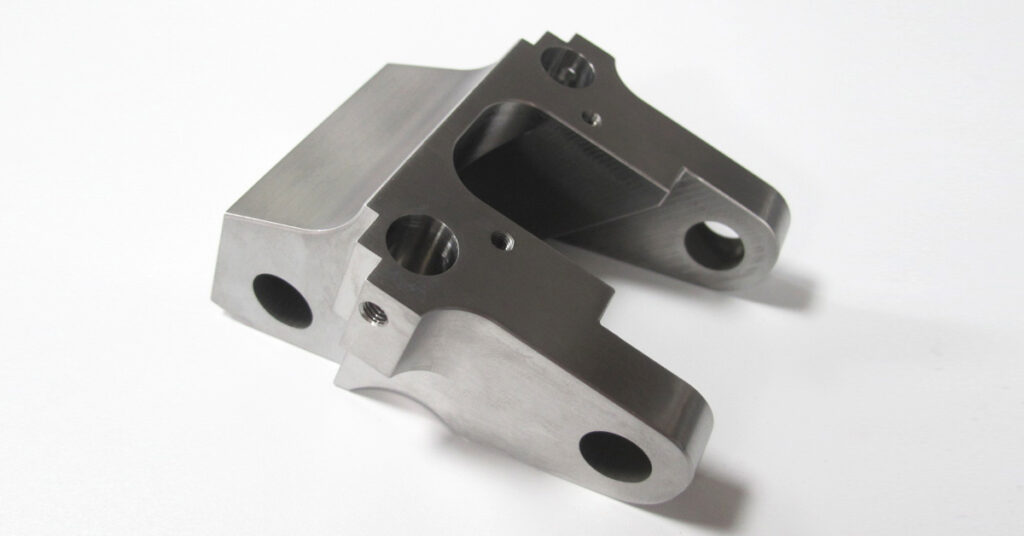
Passivation is a fundamental post-machining process for making corrosion-resistant steel parts and components. Stainless steel passivation creates a passive layer on the metal’s surface that prevents it from chemical reactivity.
This procedure eliminates contaminants like iron and dirt by producing a passive oxide layer on the stainless steel’s surface. However, various alloys and applications demand different passivation methods and techniques.
This guide discusses everything you need to understand about stainless steel passivation, its methods and techniques, benefits, and challenges of passivation. You’ll also learn helpful tips for effective stainless steel passivation. Read on to learn more about the topic!
Why You Should Consider 3D Printing Ceramic for Your Next Projects
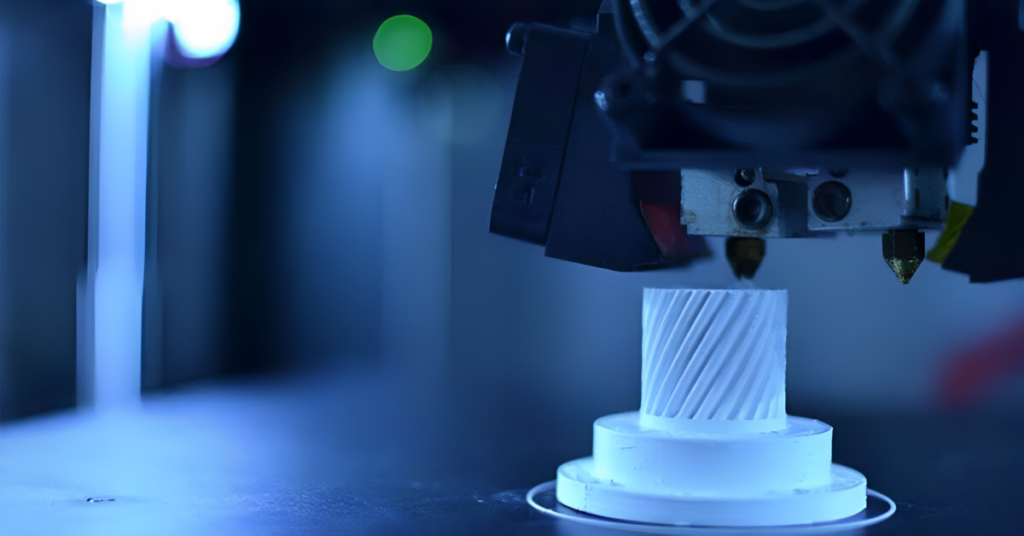
3D printing ceramics offers significant advantages over traditional methods, including Rapid Prototyping and Iteration, cost-effectiveness, and design flexibility.
As industries seek innovative and efficient production methods, ceramic 3D printing emerges as a top contender.
This technology revolutionises ceramic production and paves the way for new applications in art, aerospace, and beyond. Let’s dive in Ceramic 3D printing technology.
Bronze vs. Brass vs. Copper: Exploring Their Differences
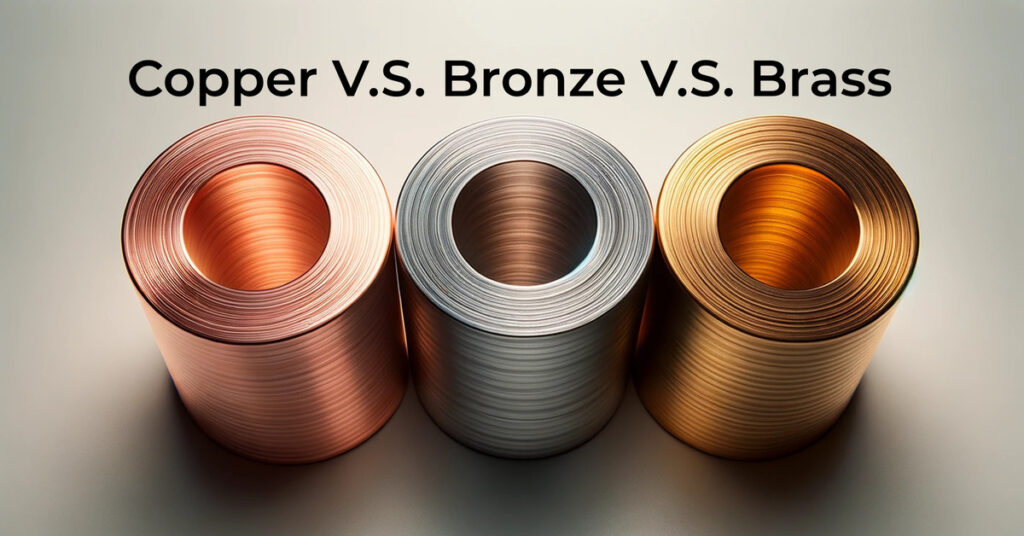
Bronze, brass, and copper are non-ferrous metals with a slight red tint; manufacturers generally label them “red metals.” Although these metals possess identical elemental composition and appearance, they have surprisingly unique properties, including corrosion resistance, high electrical/thermal conductivity, and malleability.
These properties differentiate them, making them suitable for several purposes in various industries like architecture, electronics, marine, construction, etc. Therefore, it is essential to understand the comparison of these metals to determine the right one for your projects.
This article discusses the differences between brass, bronze, and copper, exploring their available alloys, applications, material properties, and helpful tips for choosing the right material for your project.
Steel CNC Machining: A Comprehensive Guide
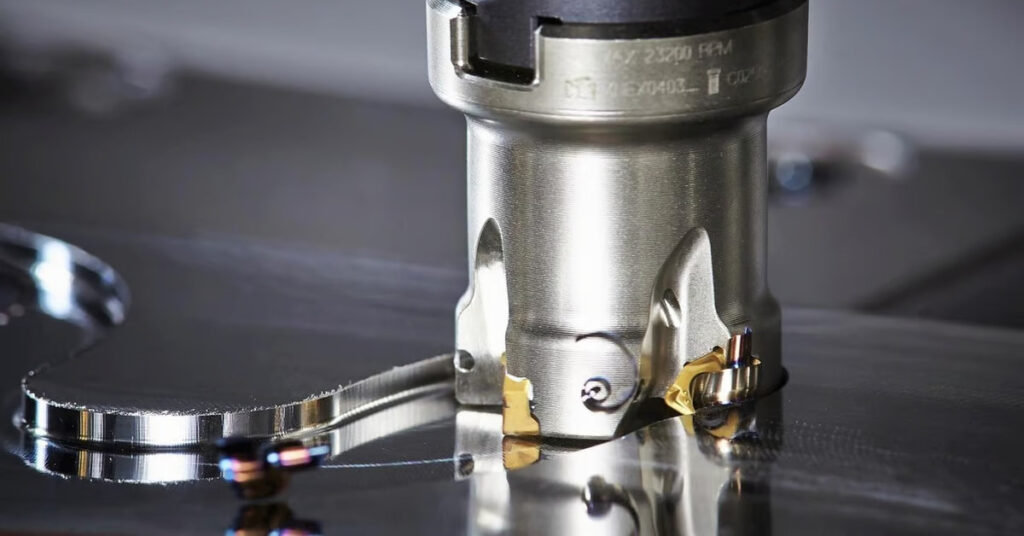
Steel is a good choice for various CNC machining operations because of its excellent machinability and homogeneity. It also offers strong workability, weldability, high ductility, and formability to fulfill any project’s specifications and is well-suited to your particular machining demands.
Steel has emerged as one of the more common industrial alloys for CNC machining projects due to its favorable physical qualities. The metal has a high tensile strength and excellent corrosion resistance, adding to the durability and part longevity of the product. This comprehensive guide explains all you need to know about steel CNC machining, including its surface finishes.
Engineering Tolerances: Definition, Types, and Fits
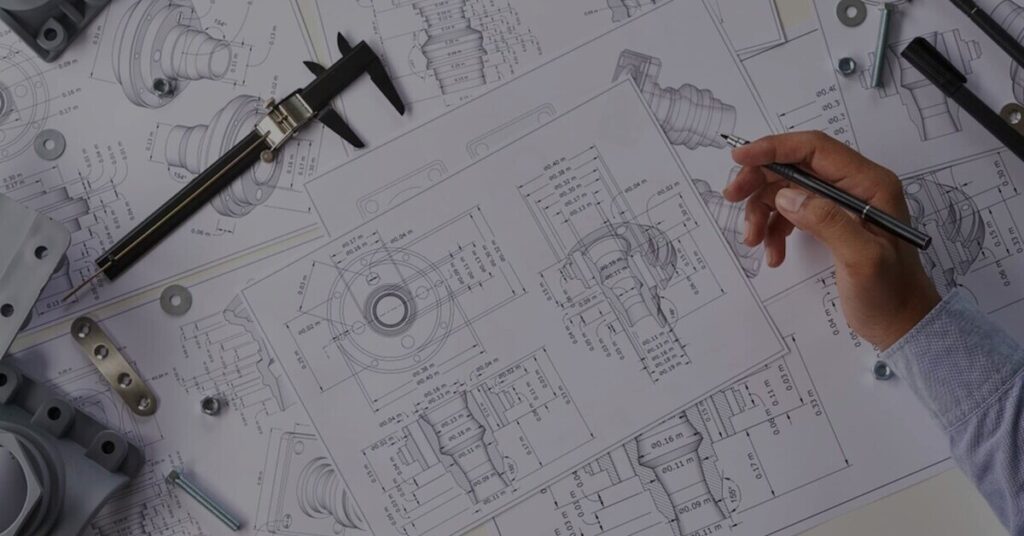
Tolerances establish the permissible deviation from the assigned dimensions or measured value in mechanical engineering. Manufacturers often use tolerances in product engineering to ensure the interchangeability of components in mechanical manufacturing.
A product may become unusable based on the design intent when the production parts’ dimension is not within the preferred tolerance limits since each fabrication process has a certain degree of inaccuracy. Therefore, it is pivotal to understand engineering tolerances and their types to achieve quality and usable products.
This article discusses what tolerance engineering is and its different types. You’ll also learn about fits and helpful considerations for part tolerancing. Let’s dive in!
Why Should Consider Wire EDM Cutting for Your Precision Project
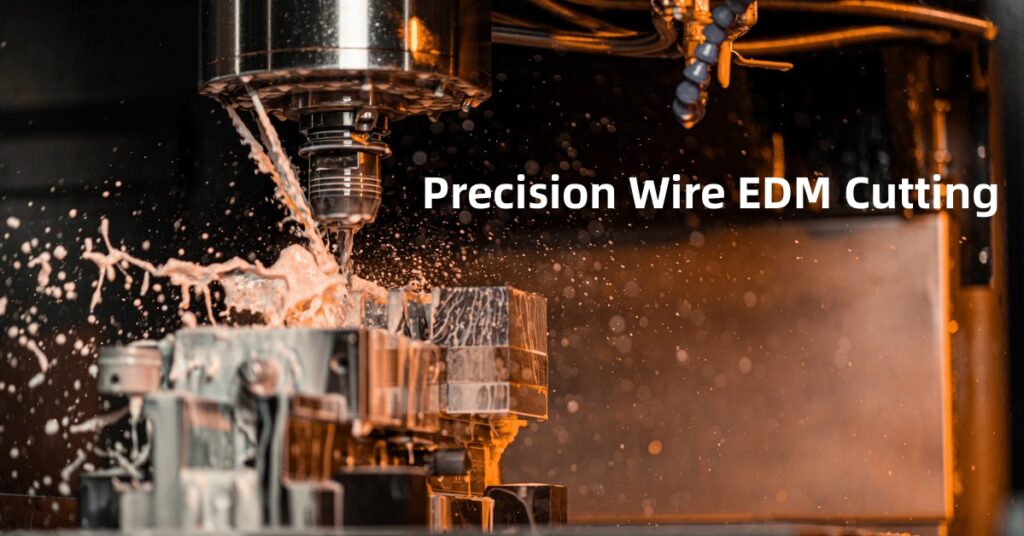
Wire Electrical Discharge Machining (EDM) emerges as a pivotal tool in precision machining, offering unparalleled accuracy and intricate design capabilities.
This article delves into the mechanics and essential components of Wire EDM, juxtaposing its advantages with limitations and drawing comparisons to Conventional EDM.
With insights into industries reaping its benefits and guidance on project-specific decision-making, this piece serves as an essential read for those exploring precision machining avenues.
Precision CNC Machining: Meaning, Advantages, and Applications
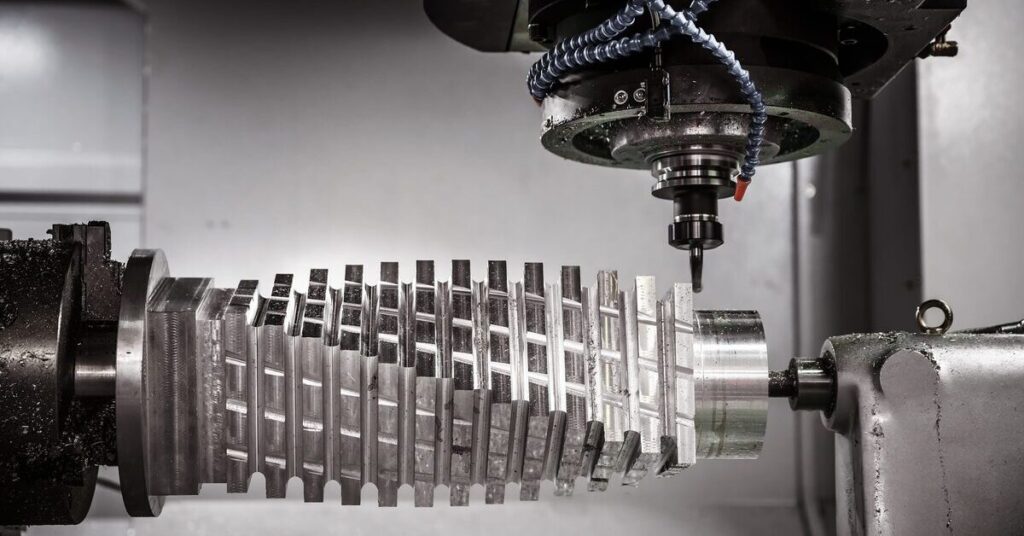
Our environment is surrounded by highly sophisticated technology that is advancing rapidly. In everyday life, we encounter several sophisticated elements, such as gears and components inside equipment, which makes us wonder what goes into making them.
For the most part, the answer to how these things are created is the same – precision CNC machining. CNC methods have been the foundation stone for modern businesses, making parts in an automated fashion at unbelievable production speeds.
Precision CNC machining has taken it further, increasing accuracy and streamlining the manufacturing process. This comprehensive guide will explain all the details about precision CNC machining, including its applications and processes.
Everything You Should Know About Deep Hole Drilling
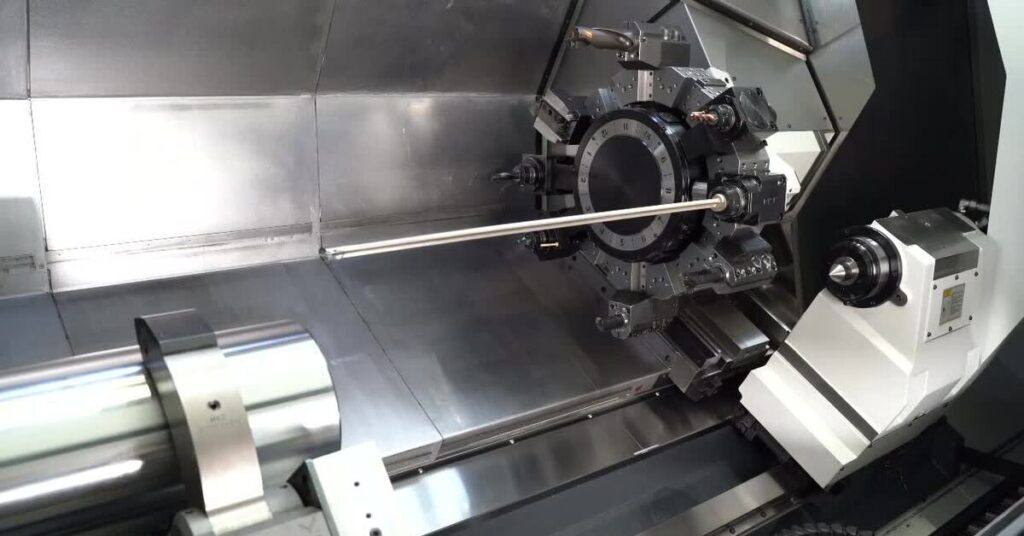
Deep hole drilling is a popular metal-working process in many fields, especially in producing firearms or heavy ordinances. This operation is perfect for most high-precision drilling projects because it provides highly accurate, repeatable holes with superior surface finishes. Therefore, it is crucial to understand everything about deep hole drilling to achieve the best results.
This guide discusses everything you need to know about deep hole drilling, its benefits, applications, and standard techniques. You’ll also learn helpful tips for effective deep-hole drilling. Let’s dive in!
Aluminum Coating: Choosing the Right Finishes for Your Aluminum Parts
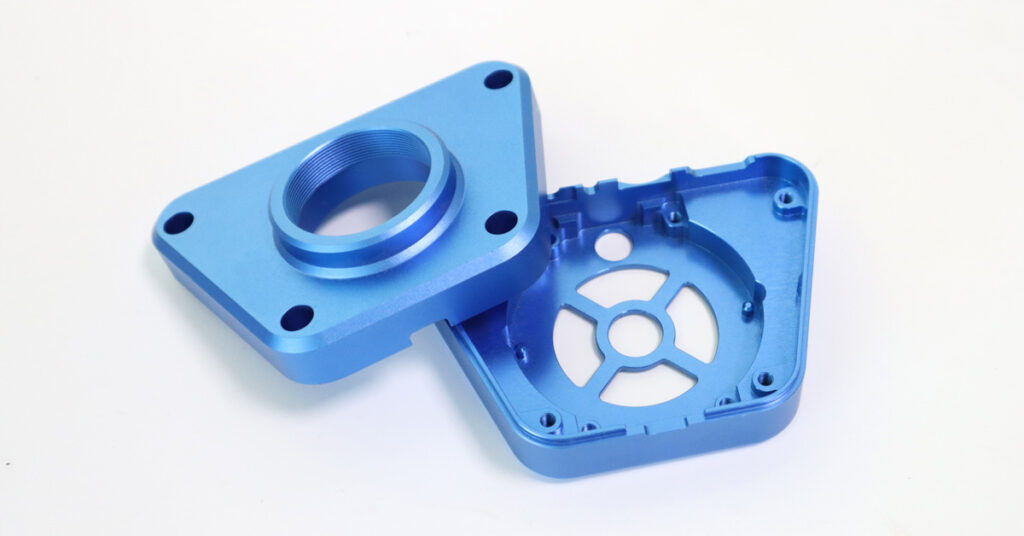
Aluminum is a versatile metal with excellent mechanical properties and extensive applications in various industries that require precision CNC-machined aluminum parts. Aluminum components often come with good surface quality.
However, manufacturers often improve the quality of these components with quality aluminum coating. For optimum results, you must choose the right surface finish to enhance these parts with better aesthetic enhancement, better physical properties, resistance to rust, wear, and chemicals, etc.
This guide discusses the common aluminum finishes and helpful considerations for choosing the ideal surface finish for your aluminum machined parts. Let’s get to it!
The Ultimate Guide to Understanding Aluminum CNC Machining
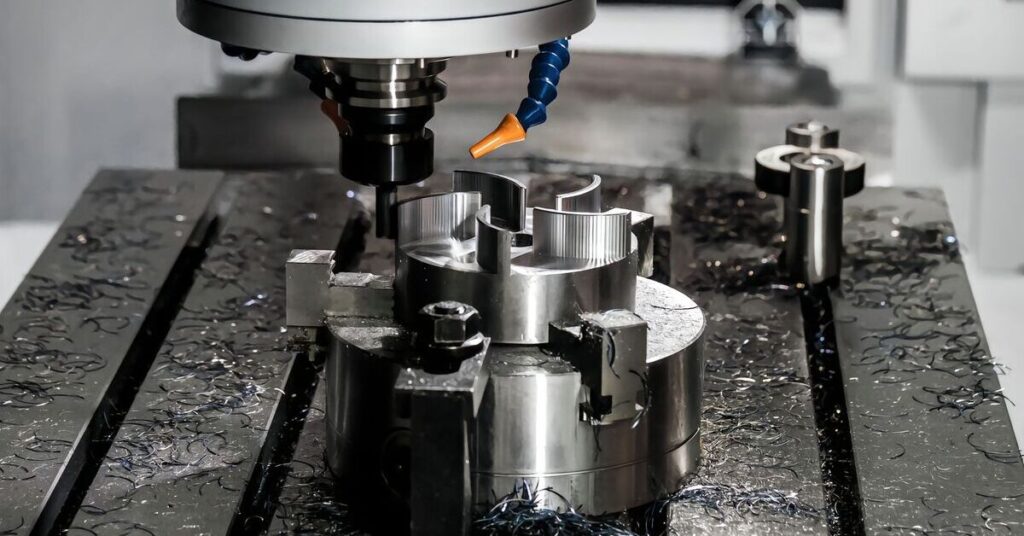
Aluminum is a non-ferrous metal commonly used in different applications. Manufacturers often utilize aluminum for various products because it is inexpensive, non-toxic, recyclable, and machinable, making it ideal for CNC machining. However, it is crucial to understand aluminum CNC machining to exploit its full potential of aluminum.
This article discusses aluminum CNC machining, the benefits of using aluminum for CNC machining, and the different grades of aluminum used in CNC machining. You’ll also learn about the standard aluminum CNC machining techniques and applications. Let’s get to it!
Top 7 Types of Aluminum Finishes To Elevate Your CNC Parts
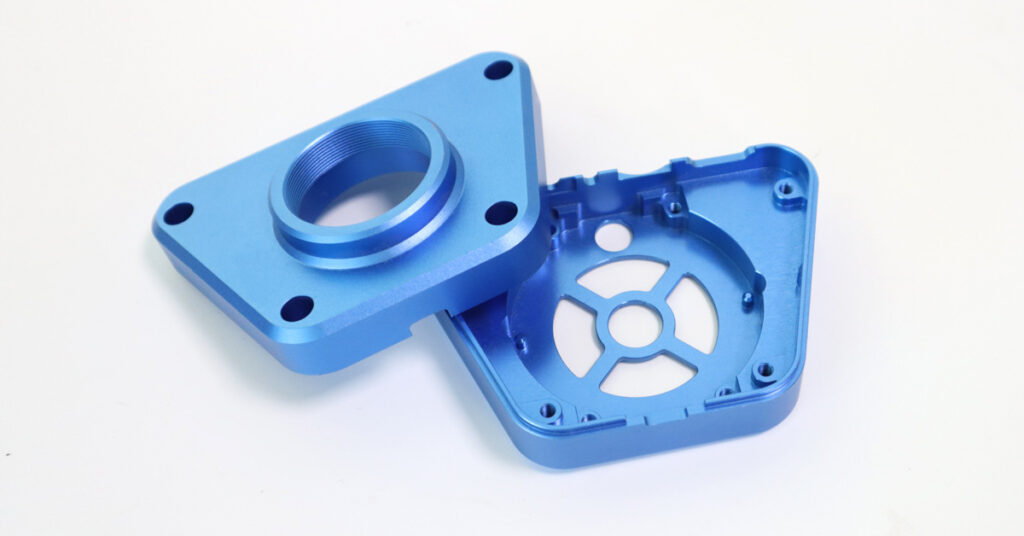
Aluminum finishes are crucial in enhancing the performance and aesthetics of CNC parts made from this versatile metal. Designers and manufacturers widely favor aluminum for its remarkable strength-to-weight ratio, good thermal and electrical conductivity, and excellent corrosion resistance.
However, aluminum parts often require additional finishing procedures to ensure optimal functionality in various applications. By selecting the right aluminum finish for your products, you can elevate their cosmetic appearance, performance, and wear resistance, among other benefits.
This guide explores the importance of aluminium finishes, the common types, and helpful tips for choosing the ideal finish for your aluminum products. Read on to learn more about the topic!
Alodine Finish: The Complete Guide to Chromate Conversion Coatings
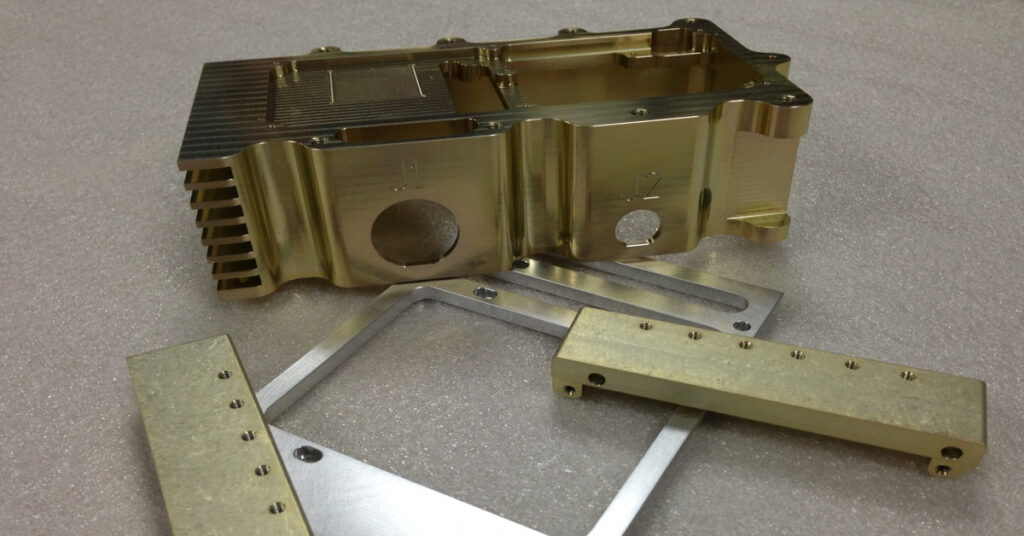
Manufacturers usually prevent surface damage and failure in precision machined parts with different measures, such as the alodine finish. The alodine finish or chemical conversion coating improves metal products’ functionality, aesthetic appeal, and other properties. Therefore, it is crucial to understand the alodine finishing process to achieve the best results for machined parts.
This guide provides detailed information on alodine finishing, why it is essential for precision-machined parts, the science behind this finish, and its types. You’ll also learn about the pros and cons of alodine finish and its application. Let’s dive in!
Safety First: Everything You Need to Know About Magnesium Machining
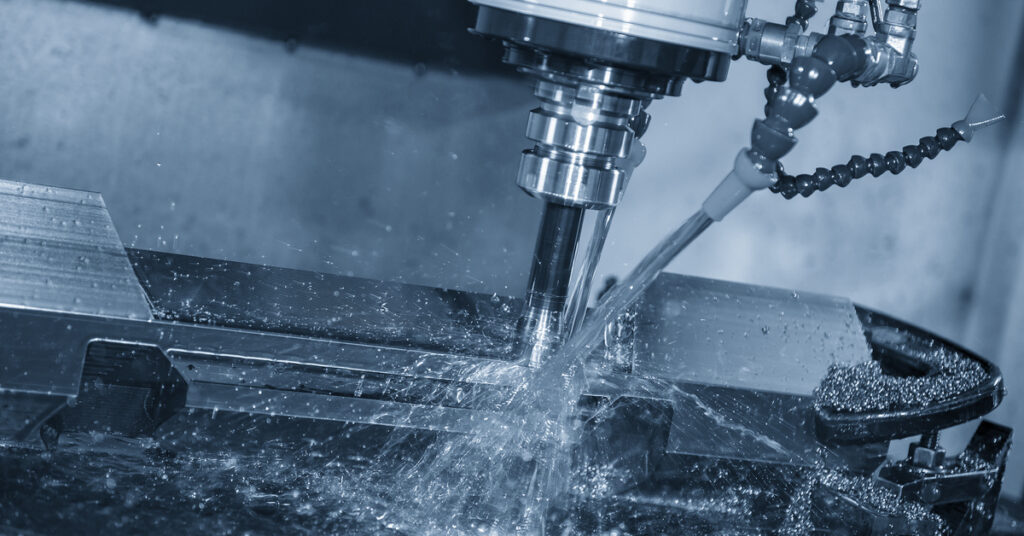
As industries increasingly turn to magnesium for its lightweight and robust properties, understanding the intricacies of safely machining this metal becomes paramount.
The highly flammable nature of magnesium, coupled with the hazards of its dust and chips, makes it a challenging material to work with.
Delve into this guide to uncover the essence of magnesium, the risks it presents during machining, and the quintessential safety protocols that can safeguard your projects.
Mastering CNC Lathe Parts: A Comprehensive Guide to 9 Essential Components
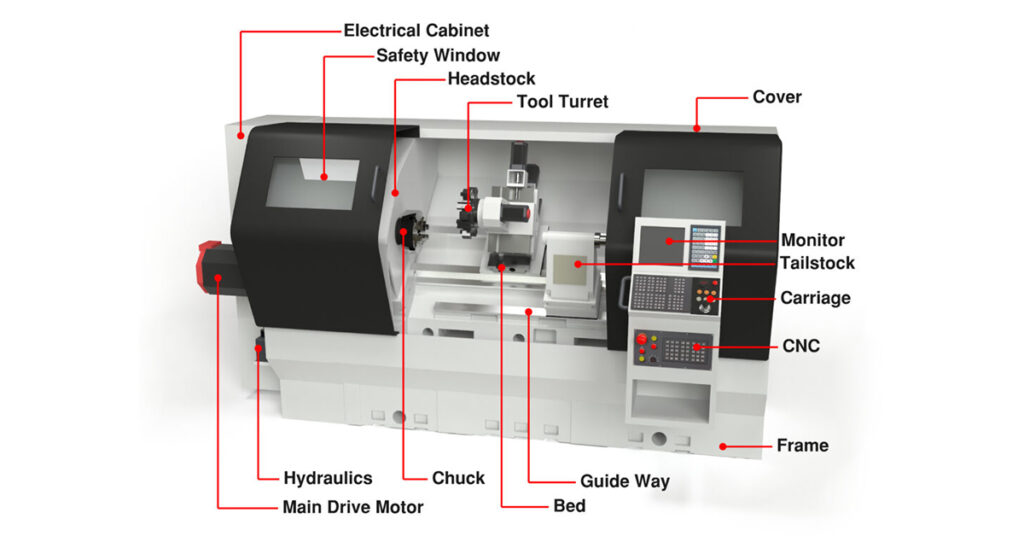
CNC lathe machines have revolutionized the manufacturing landscape with their precision and efficiency.
While many admire the end products these machines produce, few delve deep into their core.
In this guide, we’ll preview the 8 pivotal parts of a CNC lathe machine, provide proof of their significance, and give you a preview of their integral role in the machining process.
Knurling Tools and Techniques: A Comprehensive Guide
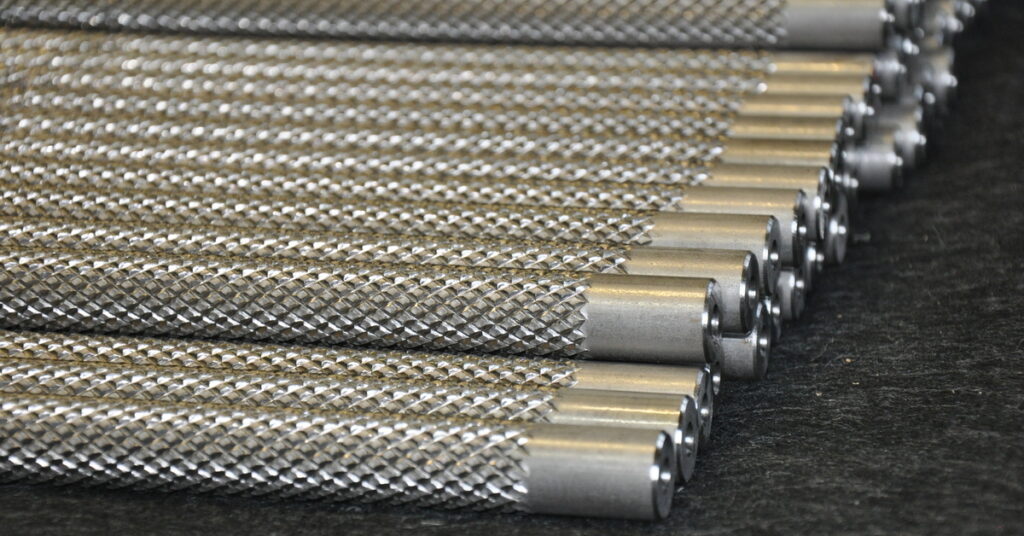
Manufacturers use different post-finishing techniques to give machined components special characteristics. Knurling is among these secondary processing methods. It can impart attractive surfaces to custom parts by creating distinctive patterns, such as ridges and indentations on machined surfaces.
This distinctive guide explains everything you need to know about knurling, including its different variations and the common problems during knurling processes. Let’s get to it.
The Ultimate Guide to Understanding Centerless Grinding
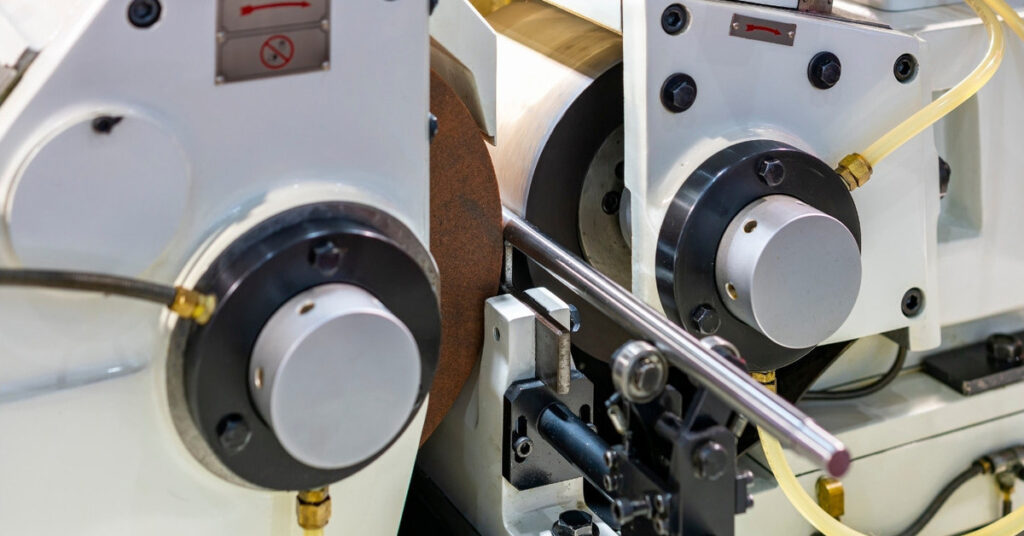
Centerless grinding is a versatile and adaptable technology ideal for machining cylindrical parts for different applications. Centerless grinding technology uses abrasive cutting to remove raw material from a workpiece.
Machinists use this cylindrical grinding technology to produce long, slender cylindrical components with consistent dimensional accuracy and finer surface finishes. However, it is essential to understand this technology to achieve the best grinding results.
This guide discusses the basics of centerless grinding, the core components of centerless grinders, how precision centerless grinding differs from traditional grinding, and its modern evolution. Keep on reading to learn more about the topic!
CNC Robotics Meets CNC Machining: Maximize Production Efficiency
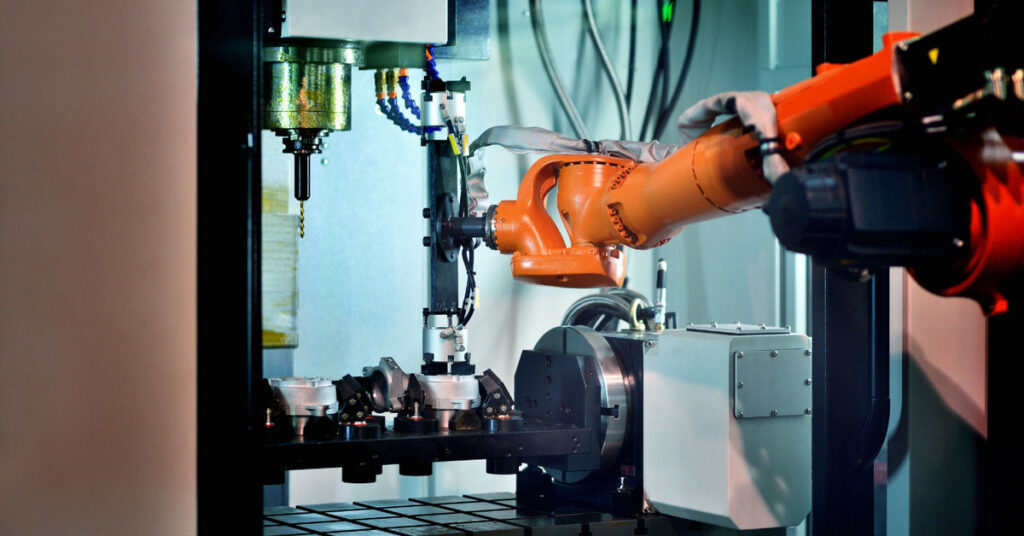
CNC robotics are fast becoming an indispensable part of modern manufacturing, transforming how CNC machine shops operate over the past years. Incorporating CNC robotics into the machining industry contributes significantly to its success. More so, CNC technology incorporation is one of the pivotal factors contributing to the success of the robotics industry today.
Even though these two technologies continue to overlap, their differences gradually become insignificant—the manufacturing sector benefits from this robotics integration. Also, robotics are the ideal option for automation in product manufacturing. CNC manufacturing robotics help industrial companies overcome manufacturing complications, maintain quality control, and reduce waste.
This guide explores the essence of CNC robotics, why CNC machining is ideal for producing robotic parts, and the symbiotic relationship between Robotics and CNC machines. You’ll also learn about the robotics used in CNC machining and compare the two technologies. Let’s get to it!
The Comprehensive Guide to Plastic Prototyping: Methods, Costs, and Considerations
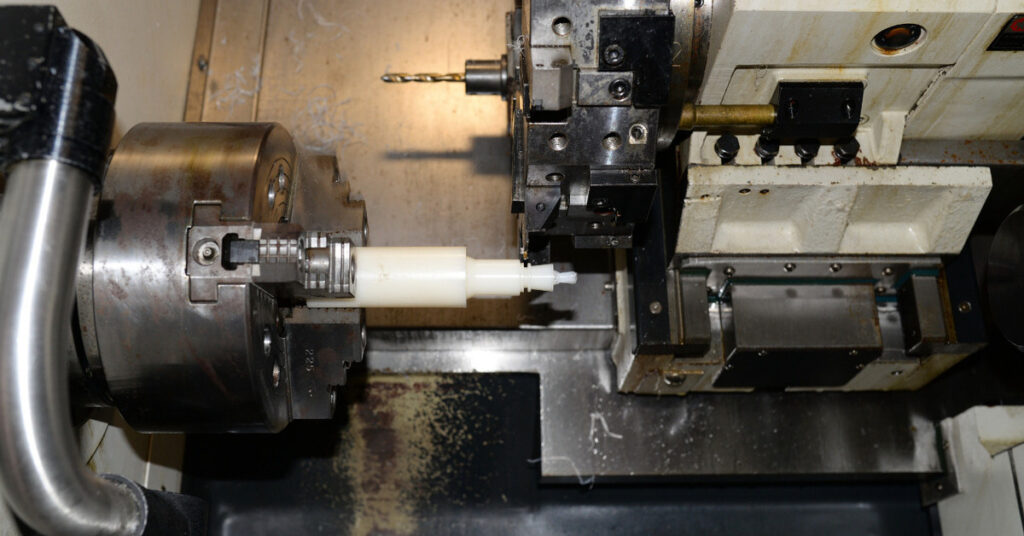
Plastic parts hardly get the deserved credit for the role played in product manufacturing despite being everywhere and having multiple applications in various industries.
Manufacturers and product developers often utilize plastic parts for different purposes, ranging from lids for coffee cups to computer keyboards, cable insulation, surgical gloves, and window frames. However, it would help to note that all plastic products started as prototypes.
This guide discusses the comprehensive guide to plastic prototyping. You’ll learn everything about the significance of plastic prototypes, plastic prototype development, methods for plastic prototyping, costs, and essential tips. Let’s get to it!
What’s the Difference? A Machining Guide to CNC Roughing and Finishing
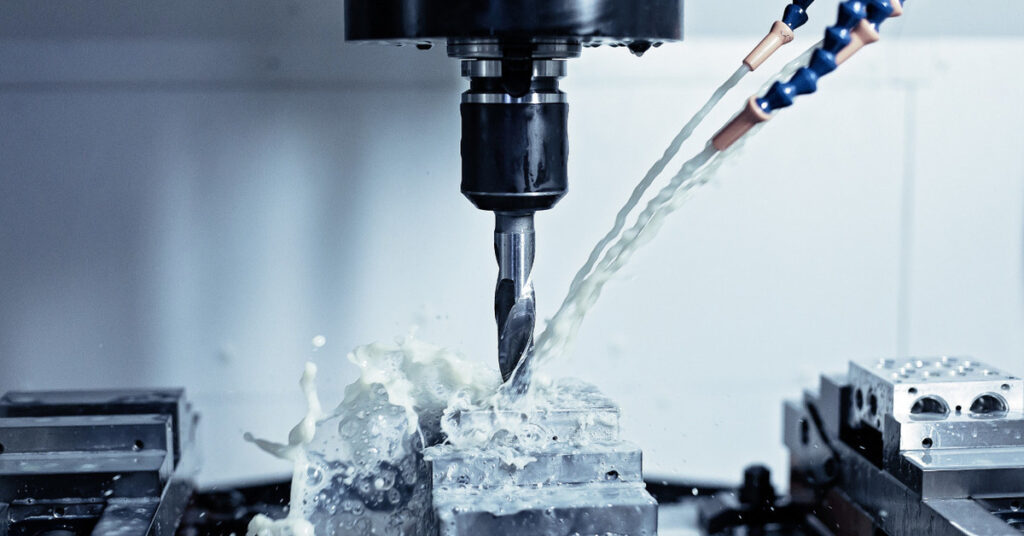
Welcome to the intricate realm of CNC machining, where rough and finish machining stands as pillars of precision, efficiency, and accuracy.
This guide delves deep into these two pivotal processes, aiming to demystify their integral roles in the industry.
Dive in as we uncover their distinct advantages and essential considerations when you’re in the market for top-notch machining services. Let’s embark on this insightful voyage to the core of CNC craftsmanship.
Everything You Need to Know About Gears Machining
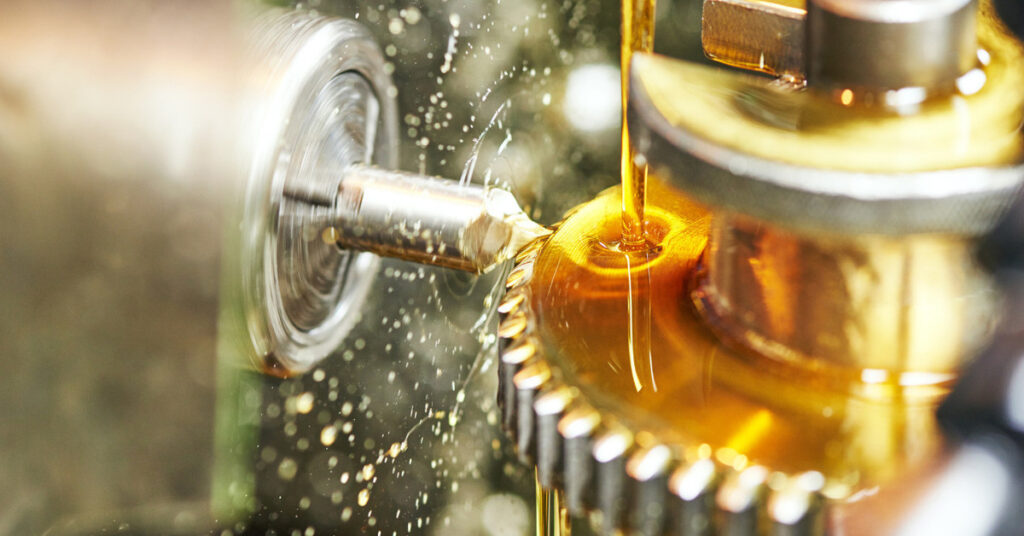
The concept of gears machining has been around for a while because they are among the oldest mechanical components still in use today. Gears offer several benefits in a wide range of applications. They are used in various products and industries, including automotive, aerospace, industrial, and more.
Gears can be created using techniques such as casting, forging, extrusion, powder metallurgy, blanking, and gear milling. However, the machining process is crucial in achieving the final gear size, shape, and surface smoothness.
This distinctive guide will explain all you need to know about gear machining, including its importance. We will delve into the various methods for gears processing, including important tips for material selection.
The Ultimate Guide to Understanding Splined Shaft Machining
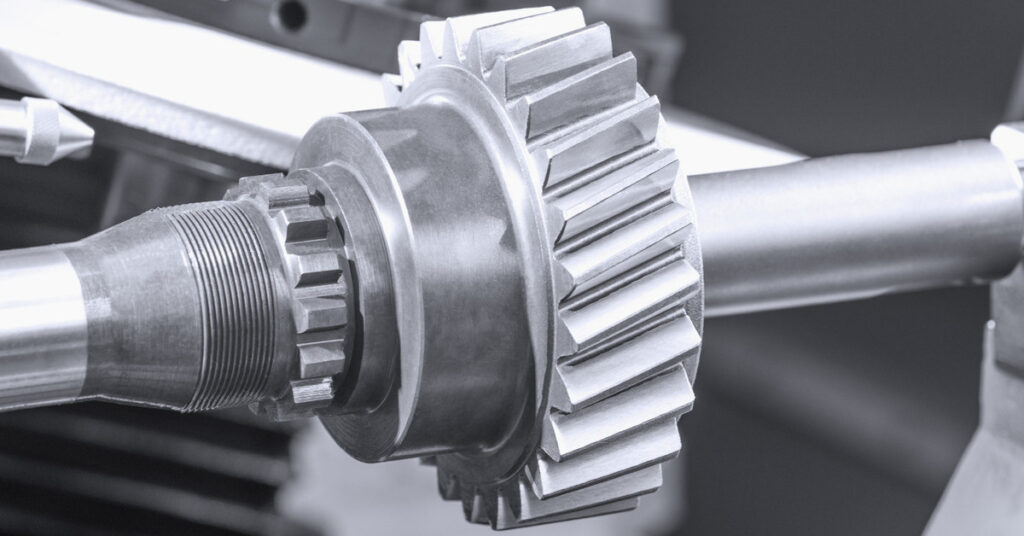
Splined shafts, intricate yet robust, play a pivotal role in modern machinery, ensuring seamless power transmission and rotational precision.
Whether you’re an engineer, a manufacturer, or someone curious about these mechanical marvels, “The Ultimate Guide to Understanding Splined Shaft Machining” is tailored for you.
Dive in to unravel the intricacies of splined shafts, their advantages, the craftsmanship behind them, and their myriad applications.
The Ultimate Guide to Machining Parts & Components
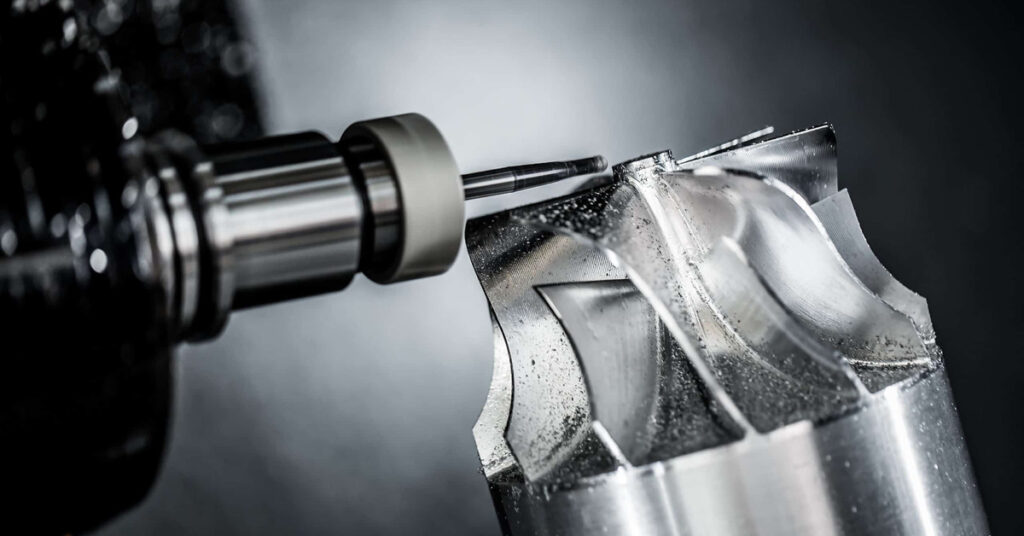
CNC machining parts is pivotal to all industries due to their high accuracy, repeatability, and precision. These machined parts are prevalent across industries because they are cost-effective for demanding applications. CNC machinists and product engineers manufacture parts with cutting-edge CNC technology, which involves automated machining operations.
This guide discusses machined parts and components, their compatible machining techniques, advantages, and design principles. You’ll also learn about the materials used for machined parts, their applications, and helpful tips on choosing the proper machined parts manufacturer.
PTFE CNC Machining: What You Need to Know for Your Project
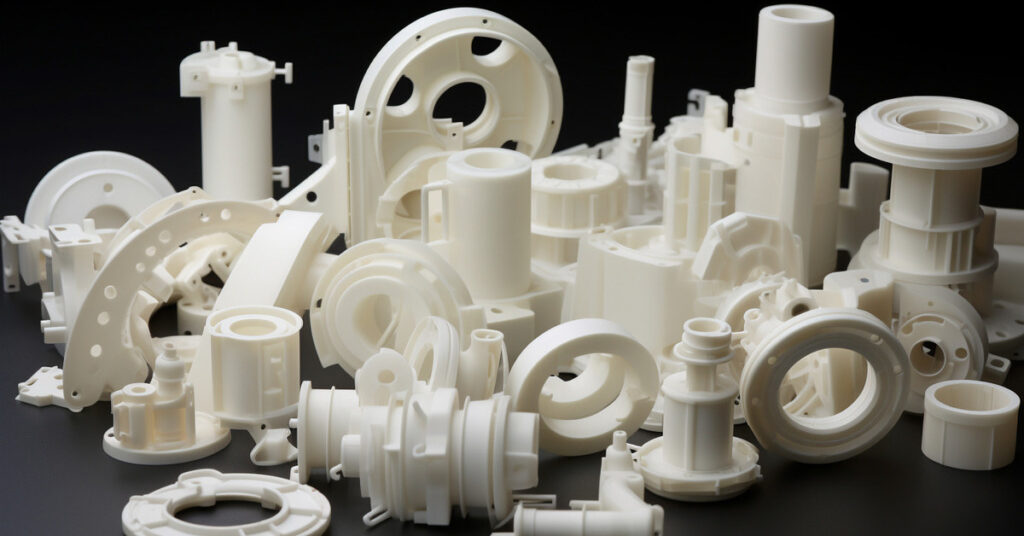
Teflon or Polytetrafluoroethylene (PTFE) is a synthetic fluoropolymer thermoplastic. It is one of the engineering plastics used in several industrial applications. Manufacturers often use PTFE due to its chemical inertness, high melting point, and low friction coefficient.
PTFE CNC machining is ideal for fabricating parts for different applications requiring good resistance to chemicals and stability at high temperatures.
This guide discusses everything you need to know about Teflon CNC machining and the common machining methods. Likewise, you’ll learn about Teflon CNC machined parts applications and the essential considerations for successful PTFE machining. Let’s dive in!
Comprehensive Guide to Stainless Steel CNC Machining
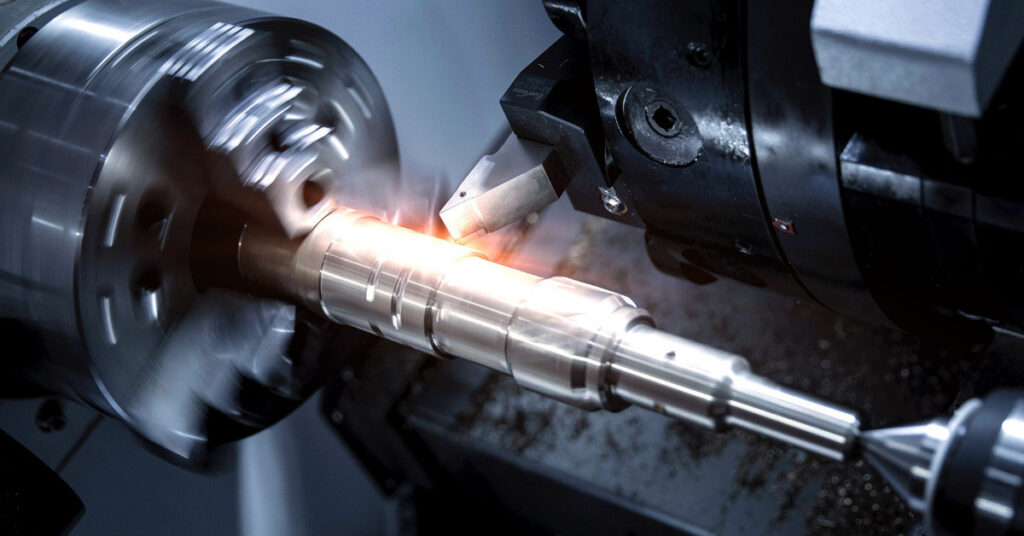
Stainless steel is a versatile and common material in many industries. Durability, high strength, and corrosion resistance are just a few of its excellent attributes. CNC machining creates intricate and precise stainless steel components through computerized automation.
This article will delve into the different grades of stainless steel available, covering their advantages and applications. You’ll also learn how to overcome various challenges associated with CNC machining of stainless steel material.
Your Automotive Prototyping Comprehensive Guide to Turning Ideas into Reality
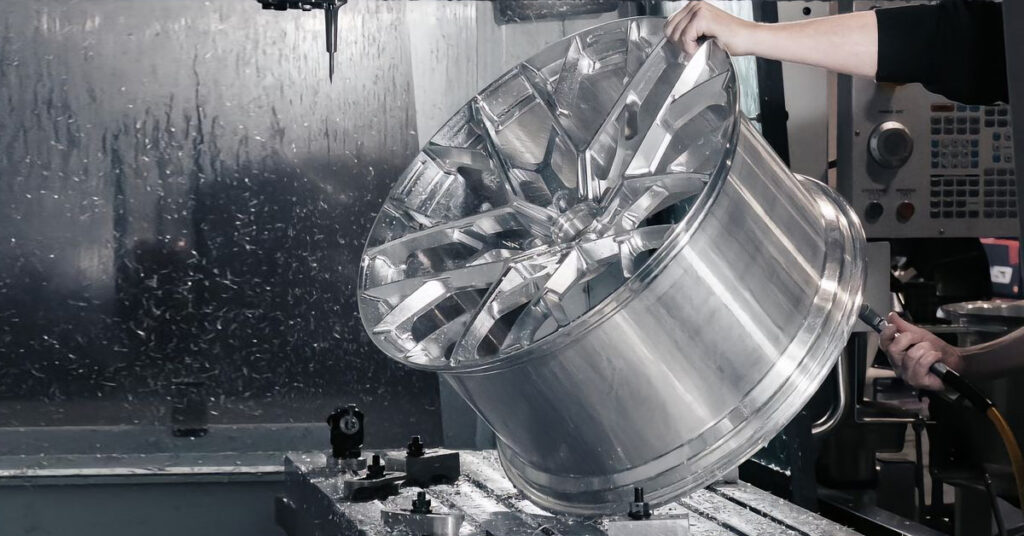
In the automotive manufacturing industry, prototyping is a cornerstone of vehicle development. It transforms design concepts into tangible models for rigorous testing, empowering manufacturers to guarantee excellence, curtail expenses, and sidestep potential pitfalls.
Venture into this blog post as we journey through the expansive domain of automotive prototyping. We’ll spotlight its innovative tools, dive into material considerations, assess cost factors, and showcase its multifaceted applications. Additionally, we’ll underline the crucial choice of aligning with the right automotive prototype services provider for your endeavor.
Copper CNC Machining: Everything You Want to Know
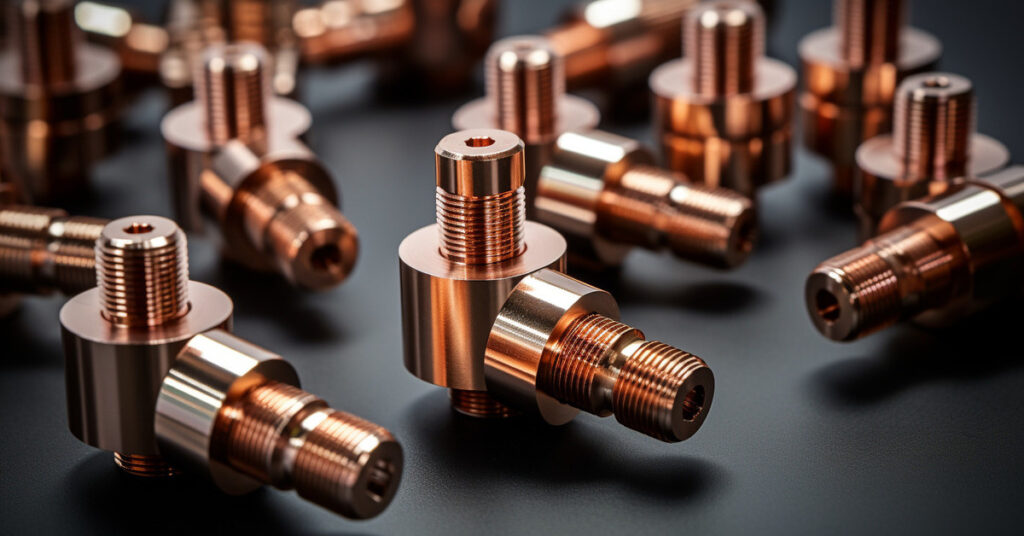
Copper is a multipurpose metal and one of the oldest metals commonly used in modern mechanical engineering—engineers utilize copper materials due to its exceptional characteristics. Most especially, copper and its alloys are valuable for different applications due to their remarkable thermal and electrical conductivity and excellent corrosion resistance.
Copper CNC machining is one of the most resourceful and precise metal machining processes industries use to create copper parts. This specialized precision machining provides high precision, compatibility, and accuracy in handling various parts’ high demands. However, it is essential to examine the factors associated with copper parts machining to determine the ideal one for your copper machining projects.
This guide explores everything you want to know about copper CNC machining, different grades of copper, advantages, and challenges of machining copper. If you also want to learn about the key considerations, machining methods, and typical applications of copper-machined parts, this guide is for you!
Mastering CNC Prototype Machining: Your Guide to Success
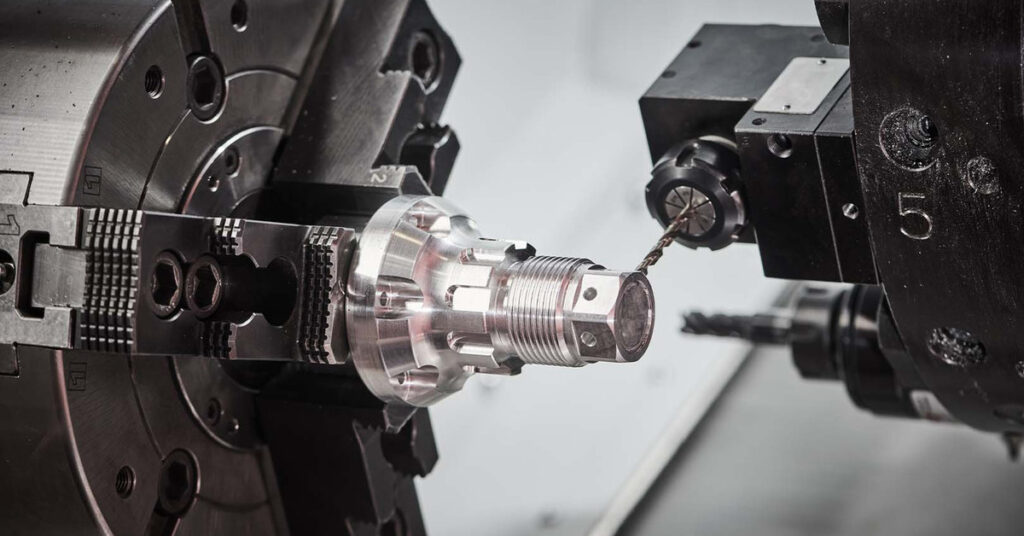
CNC machining has transformed the manufacturing of prototypes and final products. It continues to gain popularity in various industries because it offers prototypes in small volumes and more quickly than most alternative prototyping processes.
CNC prototype machining, however, is an aspect in which CNC technology has proven most beneficial with indispensable solutions in every industry. As a result, manufacturers and product developers often master CNC prototype machining to achieve effective CNC prototyping operations.
This guide explains prototype machining, why it is crucial, and different prototyping operations. You’ll also discover the applications and essential tips for successful CNC prototyping. Let’s dive in!
Micro CNC Machining: Everything You Need to Know
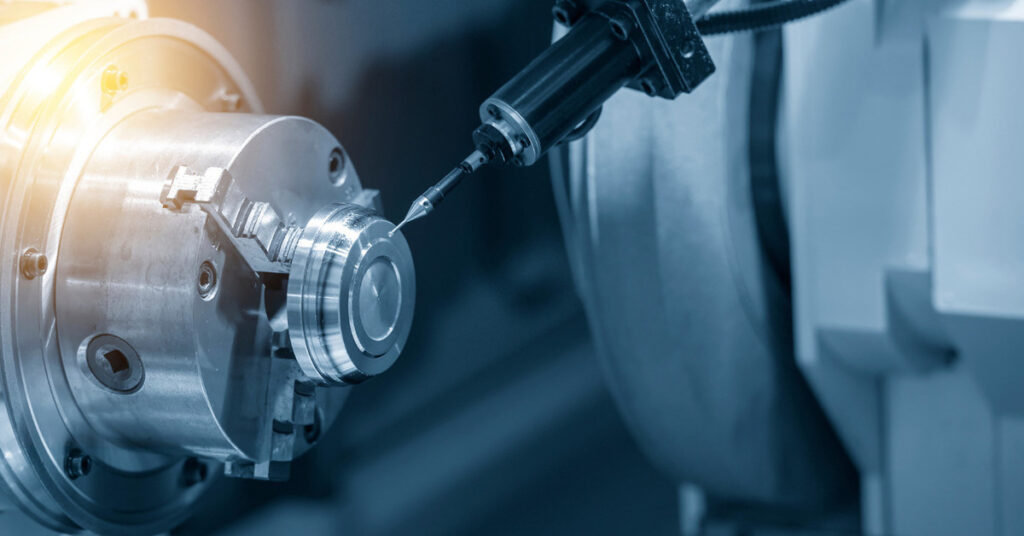
Welcome to a world where precision and technology merge to create miniature masterpieces.
This blog post uncovers everything you need to know about Micro CNC Machining.
This technology has taken center stage with the rise of industries demanding small, intricate, and complex parts. Let’s dive in.
Aerospace CNC Machining: Your Comprehensive Guide
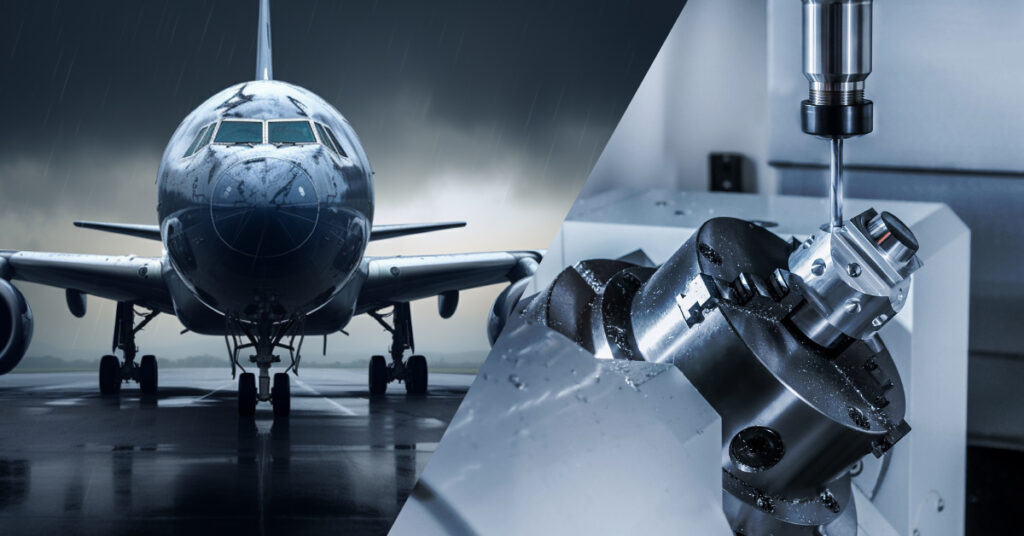
The global aerospace industry has developed significantly, utilizing innovative technologies and new manufacturing practices to produce aerospace components from an extensive engineering materials range. Aerospace CNC machining remains crucial, ensuring aircraft components meet the highest industry standards.
There is no room for errors in CNC-machined aerospace parts because these parts require the highest accuracy, precision, and speed. As a result, it is crucial to understand everything about aerospace machining to get the best out of the process.
This article explains what aerospace CNC machining is and the typical materials used in aerospace manufacturing. You’ll also learn about precision and tight tolerances in aerospace machining, multi-axis CNC machines for aerospace parts, and suitable finishing options. Let’s dive in!
Guide to Small Batch CNC Machining: Tailored Manufacturing Solutions
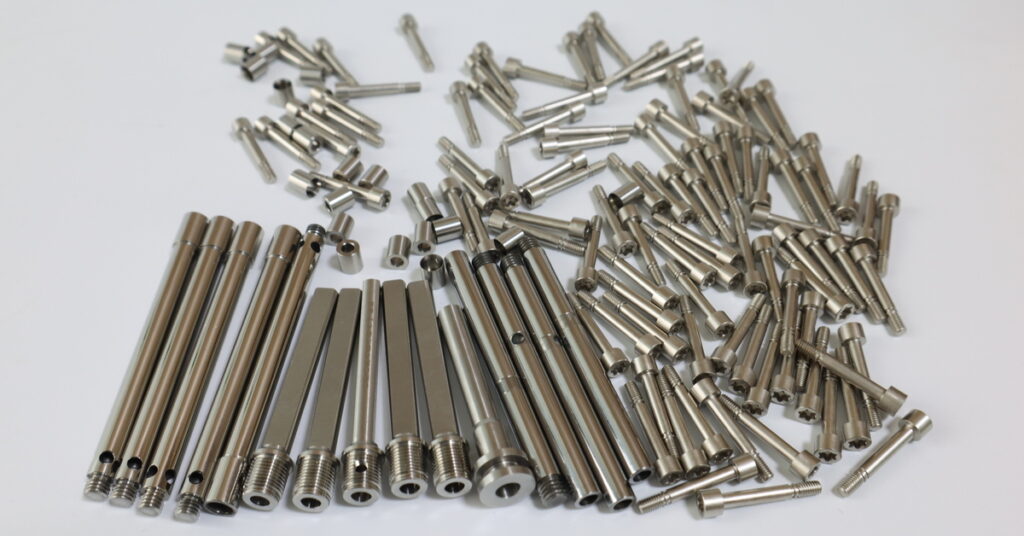
Welcome to the precision path of small batch CNC machining! In this rapidly evolving manufacturing landscape, one aspect that stands out is the increasing relevance of small batch production.
In this blog, we’ll explore this important facet of modern manufacturing and dive into how small batch CNC machining transforms how we produce goods.
Hard Coat Anodizing Aluminum: Your Ultimate Guide
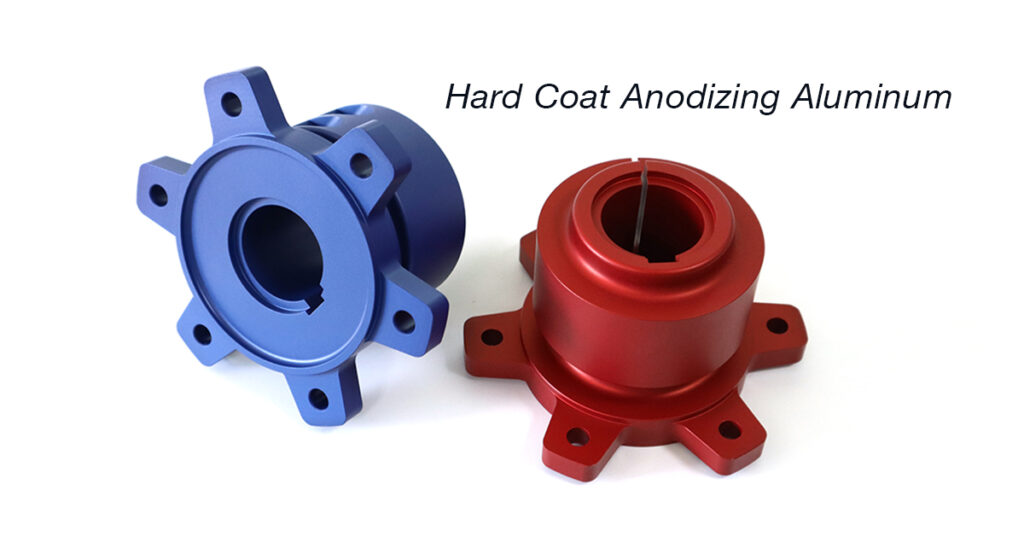
In the vast world of metal finishing and protection, one process that continually stands out for its exceptional durability and multifaceted advantages is Hardcoat Anodizing.
Ever since the early 20th century, when the potential of transforming the surface of aluminum through electrolytic passivation was first discovered, the industry has seen significant advancements.
Among these, hard coat anodizing has cemented its position as a highly valued treatment in numerous sectors.
Face Milling: Everything You Need to Know
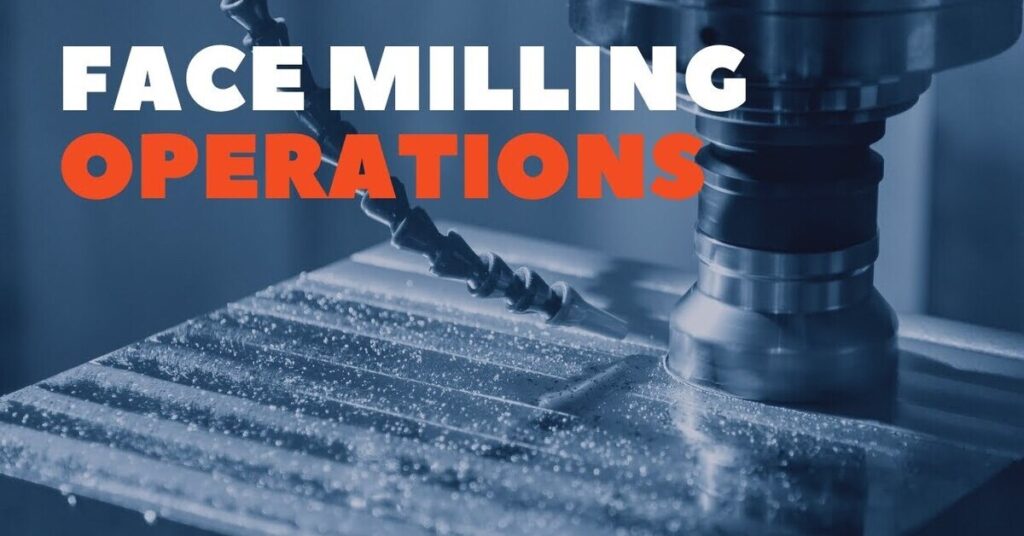
Machinists use different CNC machining procedures to enhance the surface quality of products. Face milling is one of the many finishing operations commonly used in CNC machining to meet various product design requirements.
However, different face milling operations require cutting tools with varying cutting speeds and capabilities to remove material from the surface of a workpiece. Therefore, you must understand the face milling process to determine your project’s ideal procedures and tools!
This article explains the face milling process, how it works, and its primary types. You’ll also be exposed to the comparison between face milling vs. peripheral milling and practical tips for successful face milling. Let’s dive in!
The Engineer’s Guide to Blind Holes in Machining
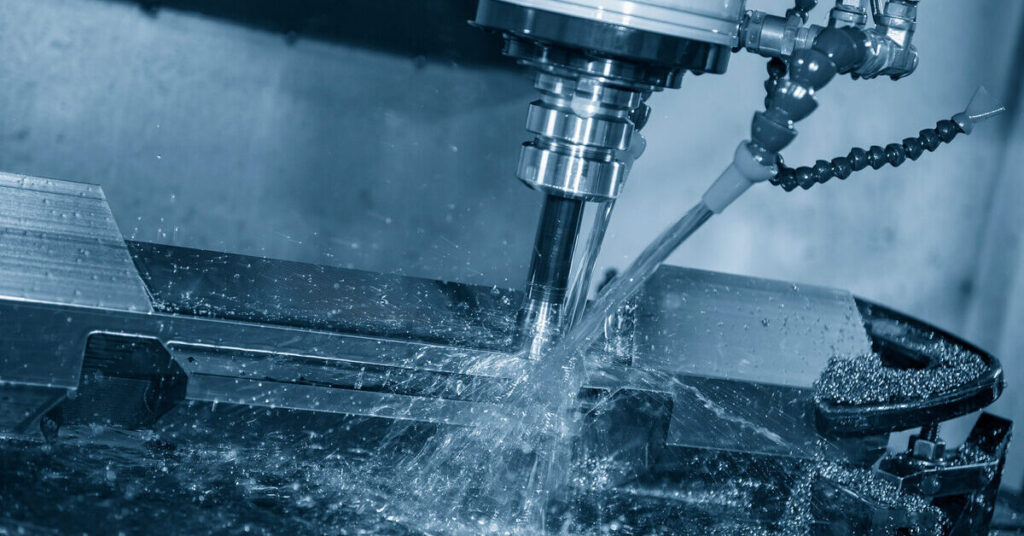
Blind holes are essential elements in machining which engineers use to add recesses, safe attachment points, or aesthetic purposes in different components. However, machining blind holes can present certain challenges hence the need to understand the machining of blind holes in various parts.
Nonetheless, it is advisable to consider variables such as alignment, depth, and debris buildup, which could affect the functionality of the hole in blind hole machining.
This article will explore what a blind hole is, how to make blind holes, and why they are essential in machining. You’ll also learn about drill depth clearance in blind hole machining, other types of holes, and tips for machining the perfect blind holes. Let’s get to it!
Understanding Grooving: The Art of Precision Machining
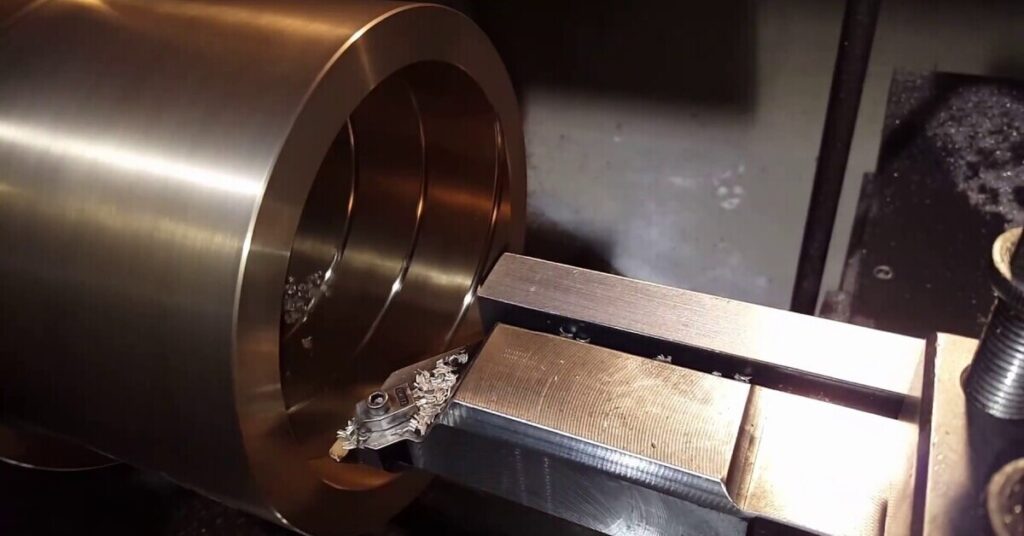
Welcome, machining enthusiasts! Today, we’re diving into the intriguing world of grooving machining.
Renowned for its precision and efficiency, this technique has made a lasting mark in the machining industry.
But what is grooving machining exactly, you ask? Let’s explore.
The Essentials of Aluminum Anodizing
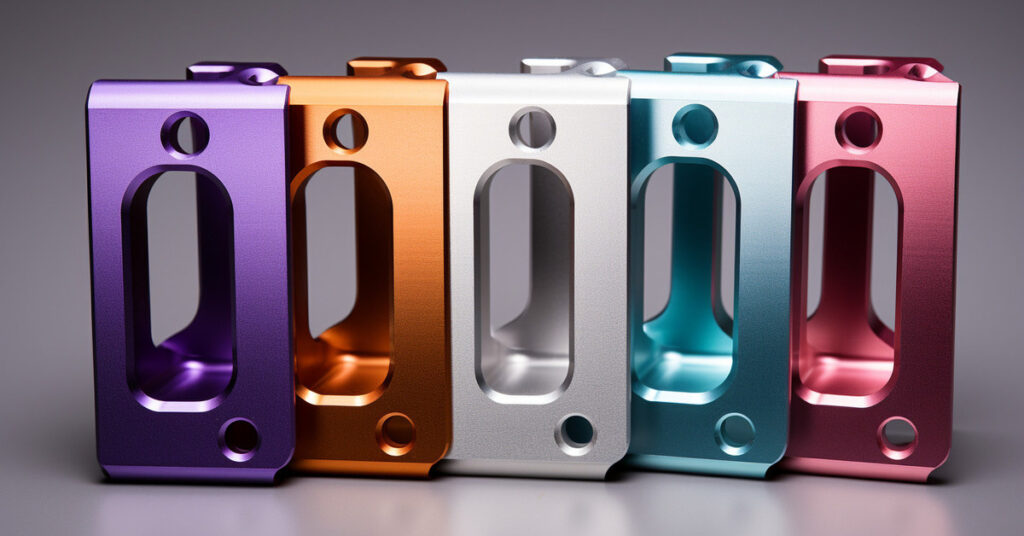
Aluminum anodizing dates back to the early 20th century as an electrochemical process providing corrosion protection. Anodizing creates a protective aluminum oxide layer by passing an electric current through an electrolyte solution.
The technology evolved over decades, improving wear resistance, durability, and color dye abilities. Today aluminum anodizing is widely used in automotive, aerospace, medical, and many other industries.
This blog will cover the anodizing process, types, color options, advantages, limitations, design tips, and applications of aluminum anodizing.
Titanium Anodizing: Everything You Should Know
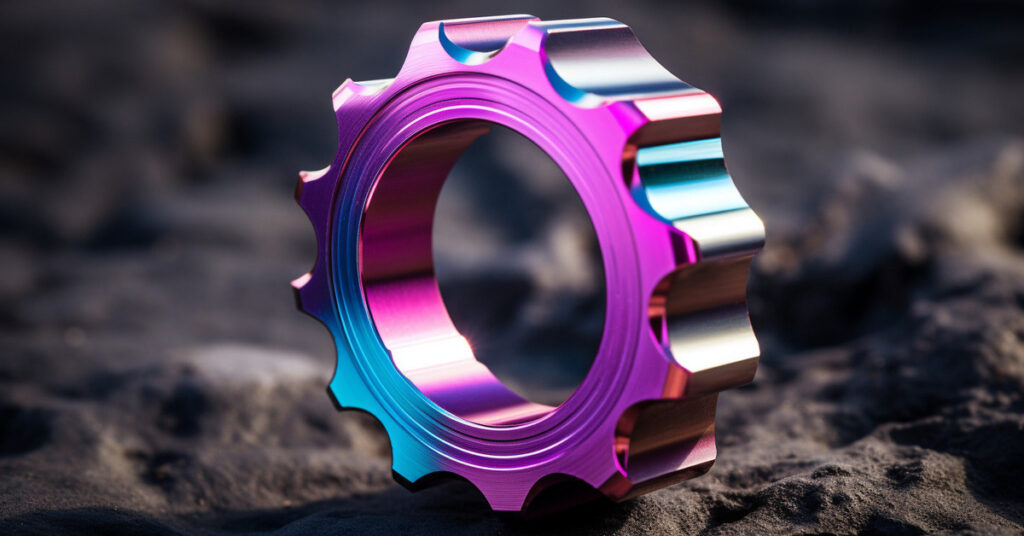
Titanium anodizing is an electrochemical surface treatment that alters the metal’s oxide layer to alter its properties.
This comprehensive guide will cover everything you need to know about the process, including the steps involved, its advantages, challenges to overcome, and various applications.
Whether you are new to titanium anodizing or looking to expand your knowledge, this blog provides key information to help you master this technology.
The Best 7 Types of UV-Resistant Plastics for Custom Manufacturing
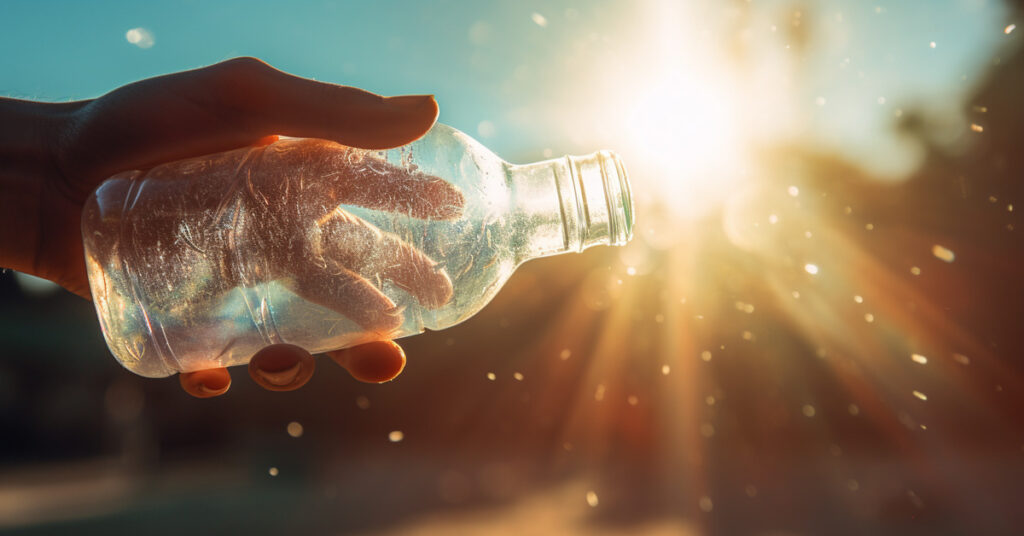
In the vibrant world of custom manufacturing, choosing the suitable material is critical. Among the multitude of considerations, one aspect often overlooked is UV resistance.
This quality can dramatically affect the longevity and visual appeal of a product.
Today, I will explore UV-resistant plastics, their importance, and how they can offer robust solutions for custom manufacturing.
Bearing Type: An Overview of Bearings and Their Applications
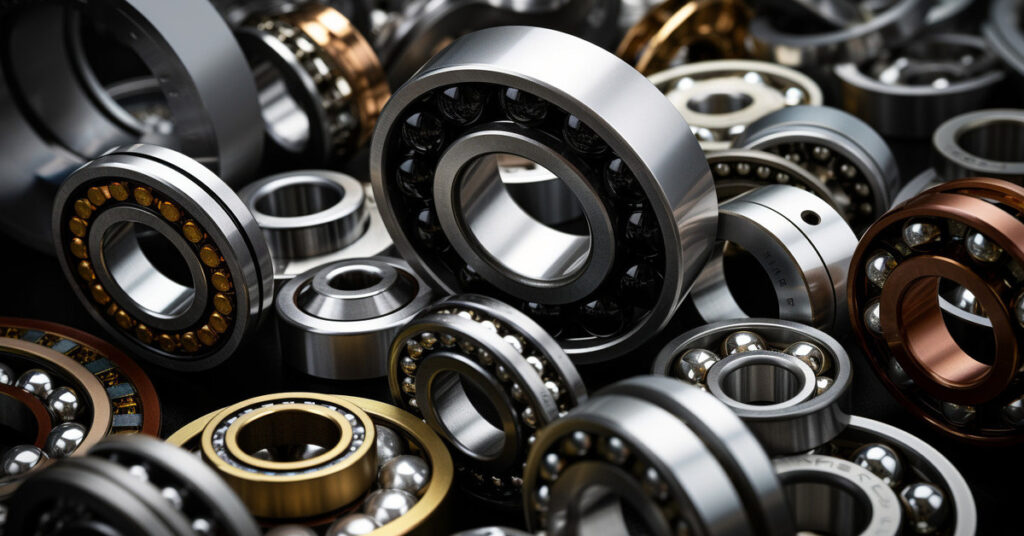
Bearings are fundamental parts of machinery widely utilized in simple household appliances and advanced industrial machinery. Bearing support axial loads in various machines and industrial equipment, ensuring reliable and smooth operation. These elements restrain the degree of freedom of different parts, giving a predefined direction to a particular component.
Engineers use these bearings to prevent direct contact between two parts or surfaces, mitigating friction in moving machinery and parts. There are different types of bearings, each with peculiar characteristics and serving different purposes.
This article discusses what a bearing is, how bearings work, why they are important, and the different types. You’ll also learn various applications of bearing and helpful considerations for choosing suitable bearings successfully. Let’s get to it!
The Ultimate Solution for Your Production Needs: CNC Machine Shop
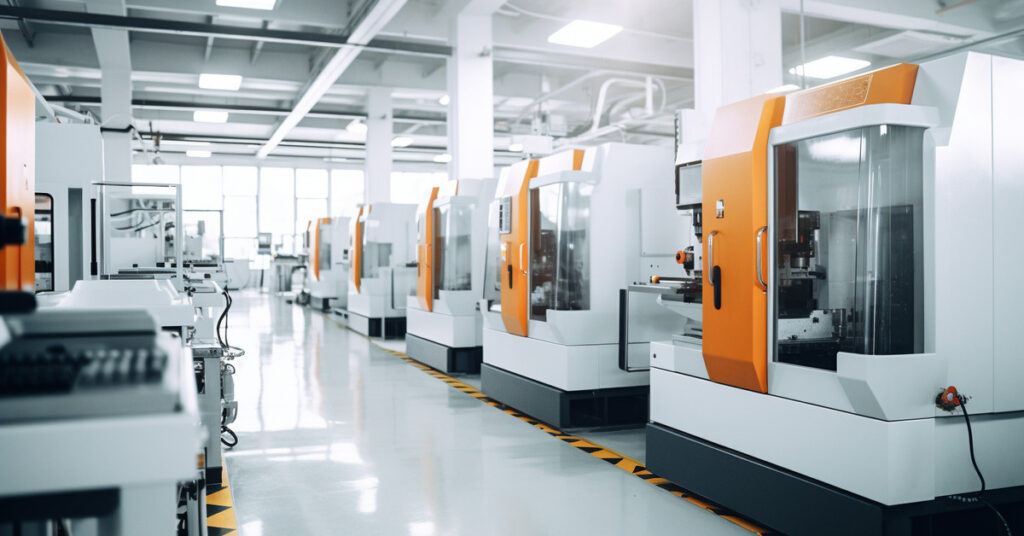
Welcome! If you’re reading this, chances are you’ve heard of CNC machine shops, but you might be wondering just how important they are for your business.
In today’s world, where precision and efficiency are the name of the game, CNC machine shops are no longer just an option—they’re an absolute necessity for a wide array of industries.
Boring Machining 101: Everything You Need to Know
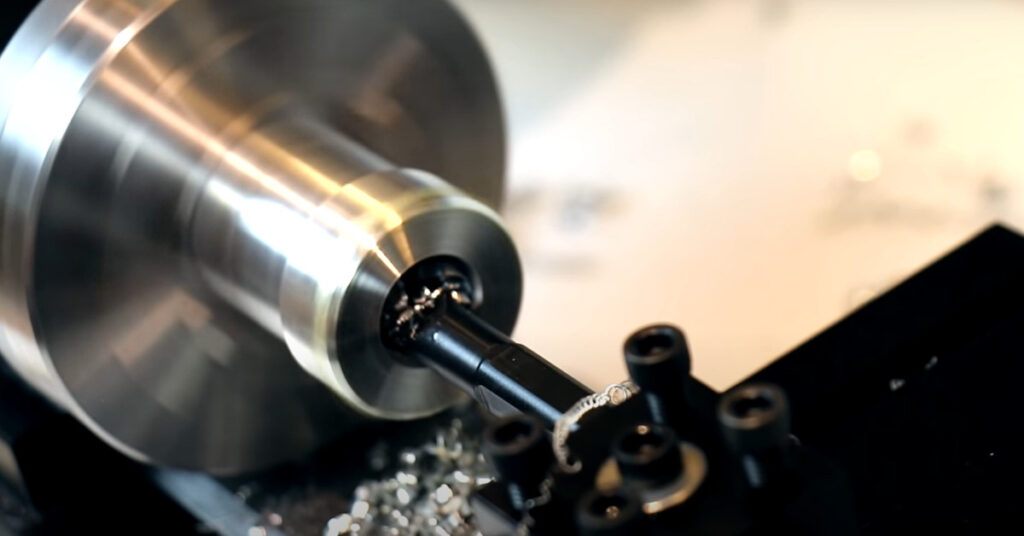
Boring Machining is a precise and versatile method used in manufacturing industries to enlarge a hole that has already been drilled or cast.
This technique is employed when an application requires a hole of accurate size and finish, often achieved with single-point cutting tools or a boring head containing several such tools.
Boring is an operation that enlarges a hole and improves its concentricity and surface finish.
Understanding the Essentials of Motor Shaft Machining
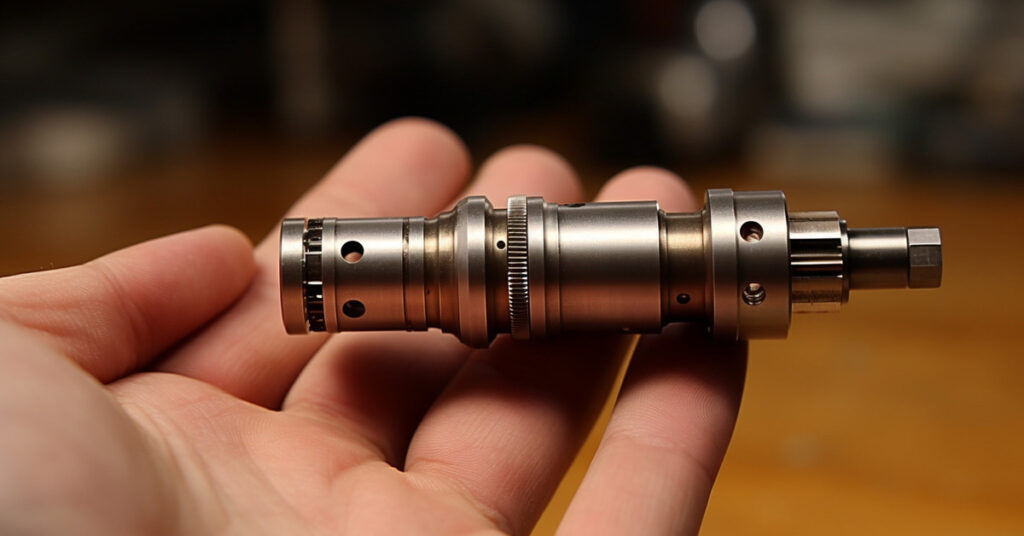
Motor shaft machining, a cornerstone of numerous industries, shapes metal into precise shafts for motor-based applications.
This intricate and often overlooked process significantly influences operational efficiency across the automotive and aerospace sectors.
Our journey today unpacks the world of motor shaft machining, revealing its critical impact on everyday machinery performance.
A Comprehensive Guide to Effective Snap Fit Design
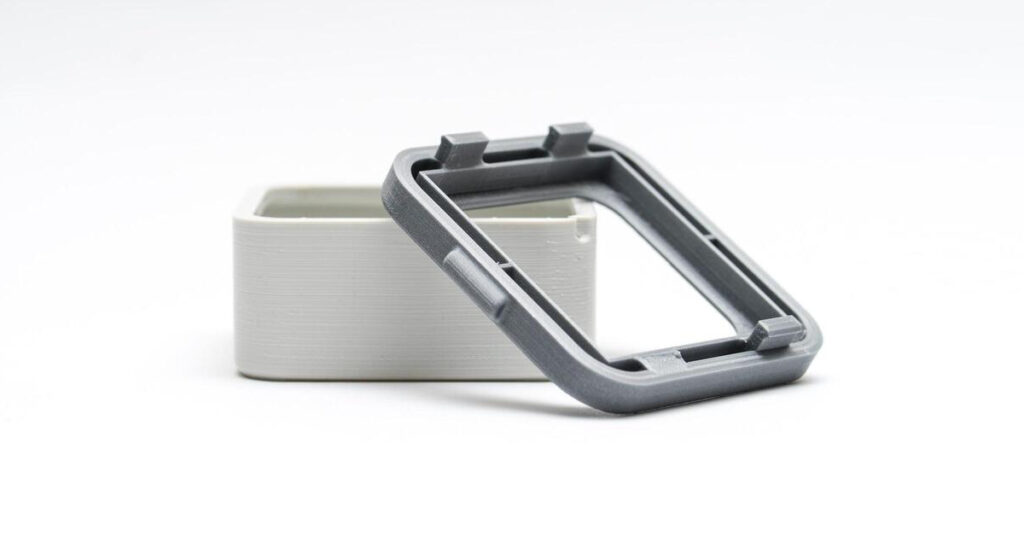
If you carefully look at the components around you, you’ll discover snap fit joints are vital elements in the design of different parts. An effective snap fit joint is an essential design feature that improves aesthetics and reduces manufacturing costs for high-quality parts.
These joints have high application in plastic fittings and can quickly assemble two flexible parts without using bolt mechanics or exposed joints. Nevertheless, understanding the snap fit design concept is essential to know the perfect one for your products.
This article explores everything you need to know about snap-fit joint design. You will learn about its types, design calculations, common challenges, and best practices for a practical snap fit design. Let’s get to it!
Heat Treatment of Metals: Everything You Need to Know
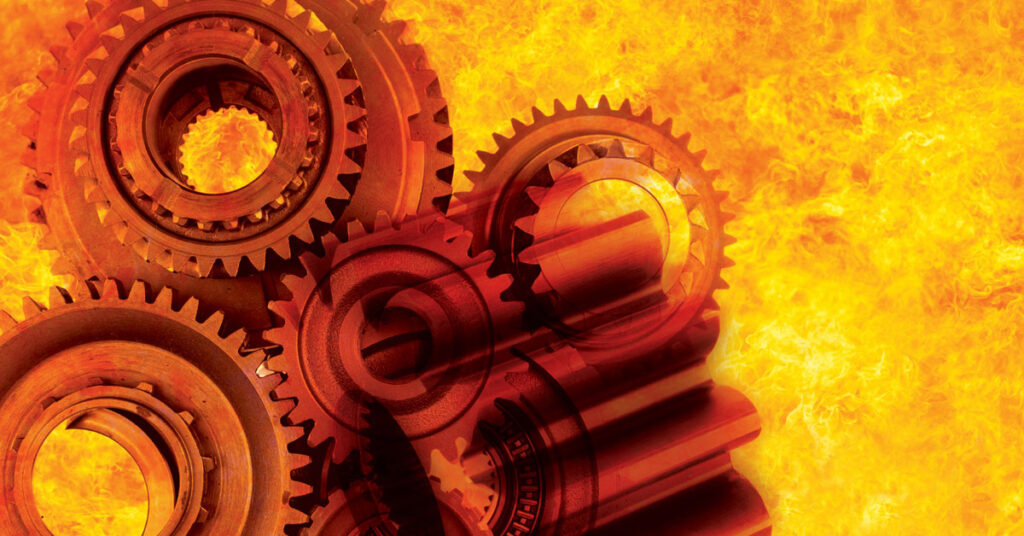
This blog post takes an in-depth look at the ancient yet ever-evolving process of heat treatment of metals, which has spurred significant technological advancements. It explores the role of heat treatment in altering metals’ physical and sometimes chemical properties for diverse industrial applications.
Heat treatment has played a crucial role from ancient times to today’s cutting-edge technologies used in various machining and metallurgical processes. This post comprehensively explores different heat treatment methods, mainly focusing on steel and the benefits these processes offer.
Join us as we delve into the fascinating world of heat treatment, its techniques, and its lasting impact on industry and technology.
Plasma Cutting 101: The Ultimate Guide to Choosing Your Machining
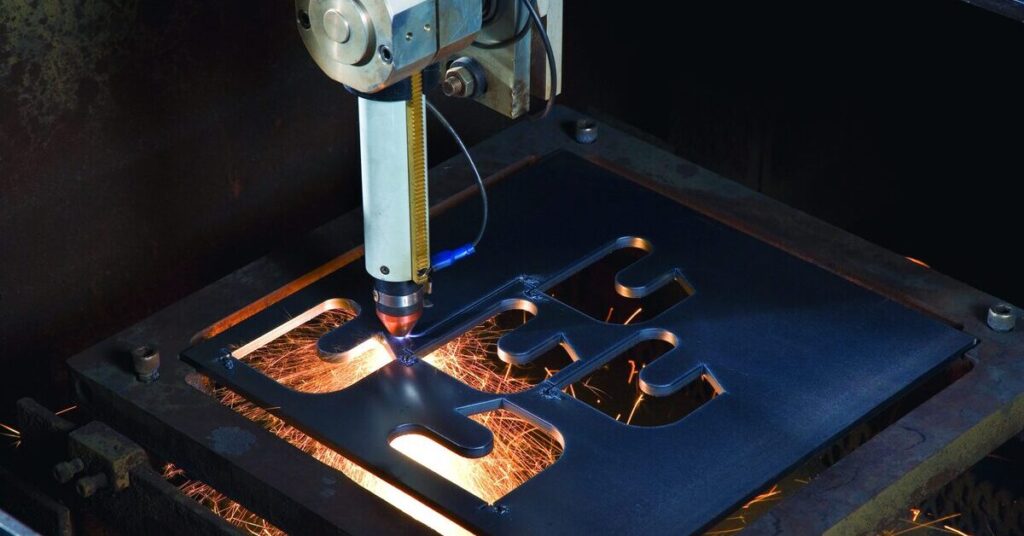
As manufacturing processes become more sophisticated, plasma cutting becomes crucial.
With its ability to cut through various materials efficiently, Plasma cut process plays a critical role in the automotive, construction, and aerospace industries.
This cutting method’s precision, speed, and versatility are unparalleled, providing manufacturers with a competitive edge in an increasingly demanding market.
Types of Machining Processes: Which One is Right for You?
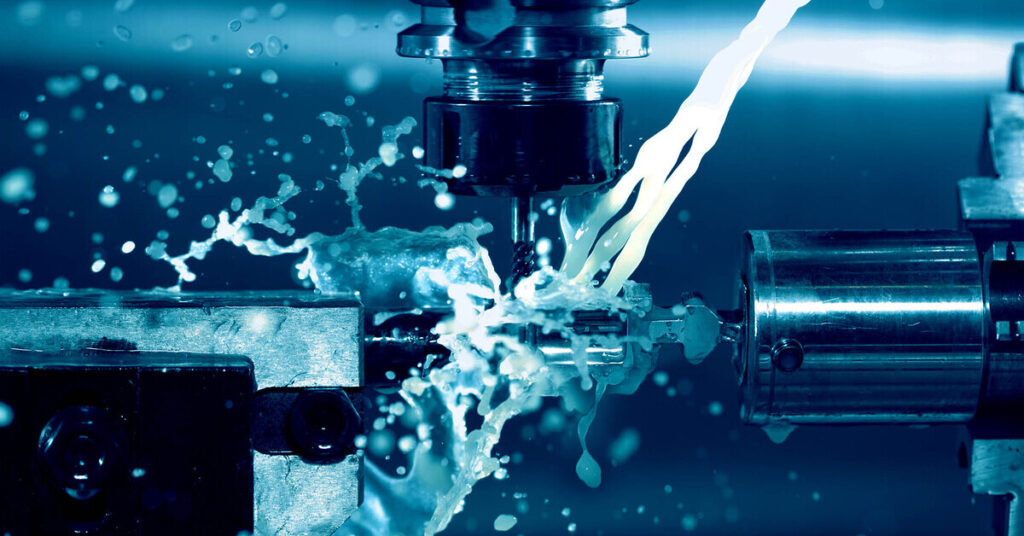
The industrial sector continues to experience innovative developments in machining due to the constant evolution of machining operations. Product engineers and manufacturers in different industries use various types of machining processes and tools to customize and fabricate different components.
These processes come with unique features and properties. Therefore, they are best suited to specific applications. Since there are various machining processes, it can be challenging to differentiate between them.
This article discusses the types of machining operations and their intricacies. You’ll also find out the differences between conventional and non-conventional machining processes to help you choose the best one for your project. Let’s dive in!
A Guide to Understanding Marine Grade Aluminum
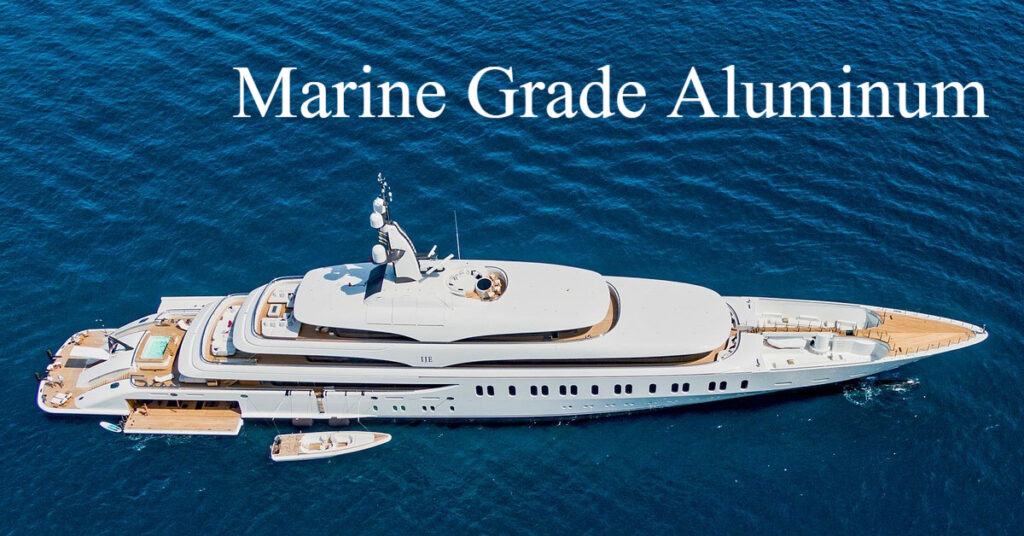
Dive into the world of marine-grade aluminum in this comprehensive blog post.
Explore its unique alloy composition, understand the various types and their applications, and learn why it surpasses other materials regarding durability and resilience in marine environments.
This post is your ultimate guide to why marine-grade aluminum alloy truly is your best defense against harsh ocean elements.
Which grade of Torlon would be optimal for your CNC project?
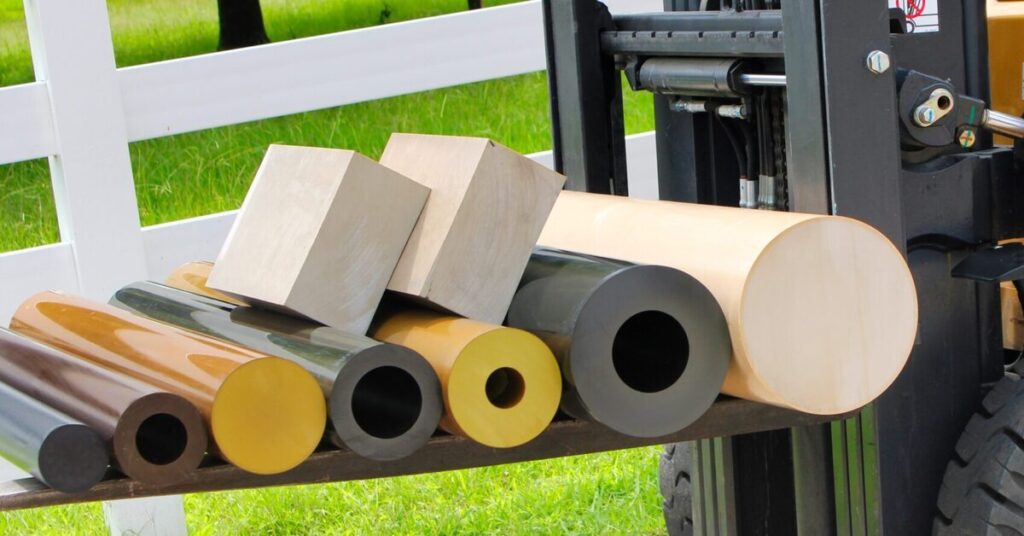
Whether you’re a hobbyist or a seasoned professional, selecting the right materials for your CNC projects is crucial.
One high-performance plastic that often comes up in these discussions is Torlon.
Known for its exceptional strength, stability, and resistance to harsh environments, Torlon can be the secret ingredient to a successful CNC project.
But it’s not just about choosing Torlon; it’s about choosing the right grade of Torlon.
Torlon CNC Machining: Unleashing the Potential of Advanced Plastics
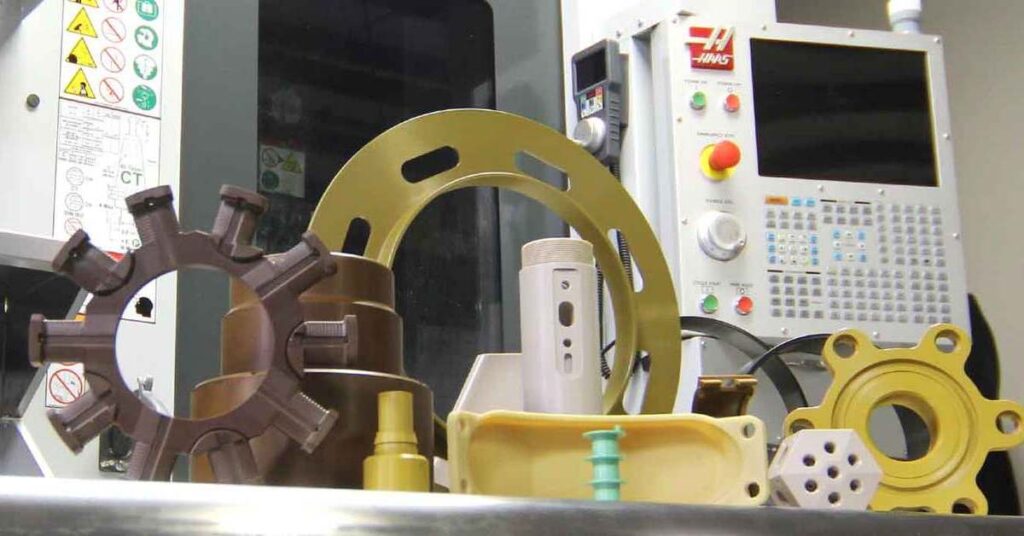
Welcome, readers, to the captivating world of advanced plastics, where materials like Torlon are revolutionizing the CNC machining industry.
In this blog post, we’re diving into Torlon – a standout among advanced engineering plastics. We’ll uncover why Torlon holds a prestigious position in this category and how its unique properties are revolutionizing the CNC process, enabling the production of superior components that outperform those made from traditional materials.
CNC Grinding 101: Everything You Need to Know
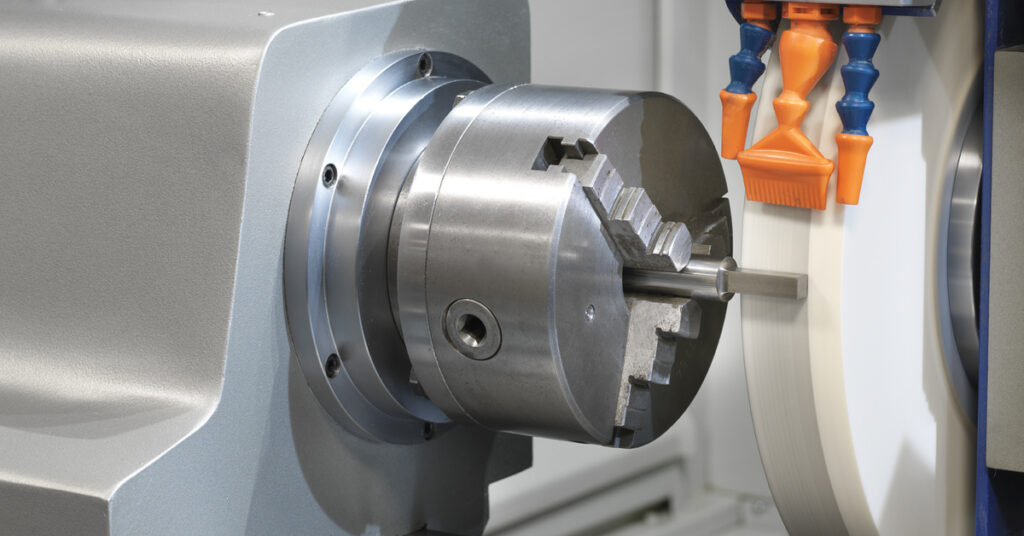
Welcome to the intriguing world of CNC grinding in the machine tool industry, where precision, speed, and efficiency amalgamate to craft perfection in metalworking.
CNC grinding, renowned for its ability to yield high precision and superior quality, has carved out an irreplaceable niche in numerous industries.
Let’s dive into this captivating subject to comprehend the reasons behind its significant prominence.
CNC Machining Renewable Energy Industry: Detailed Overview
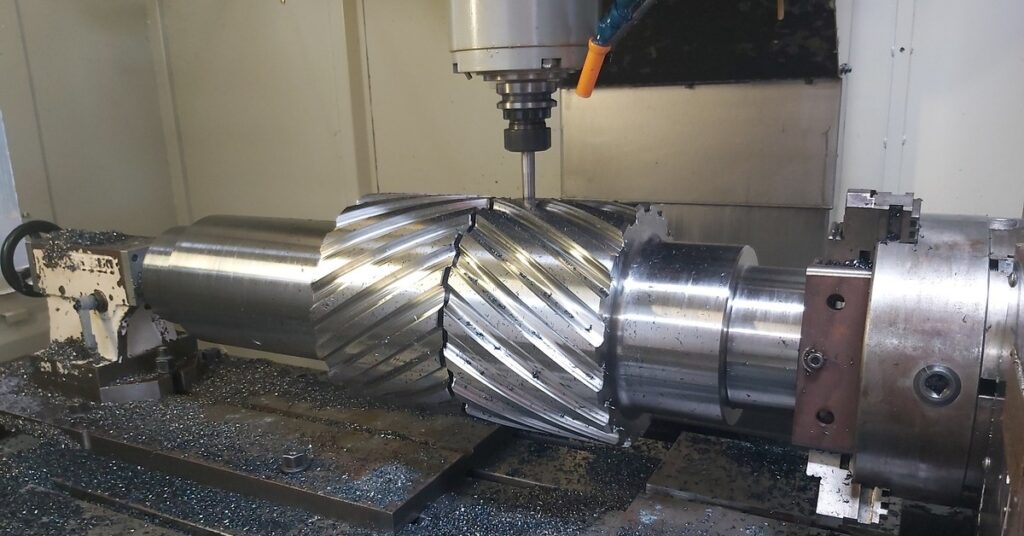
The demand for greener energy alternatives has increased considerably since the harmful effects of carbon emissions have raised concerns for modern society. Green/renewable energy sources have consistently become more accessible to industries and are primary techniques for several developed countries.
These wind, solar, and hydropower energy commonly use precision parts that perform consistently and sustain greater loads. As such, the CNC machining renewable energy industry efficiently creates functional parts and advanced equipment, from solar cells to hydraulic valves for the oil and gas sector to wind turbine components. Therefore, companies can reduce carbon emissions while maintaining business feasibility and relative economies of scale.
This article discusses how CNC technologies contribute to the renewable energy industry. You’ll also learn about the role CNC machining plays in the future of renewable energy. Let’s get to it!
Ultra Precision Machining Uncovered: Unlocking the Secrets to High-Precision Manufacturing
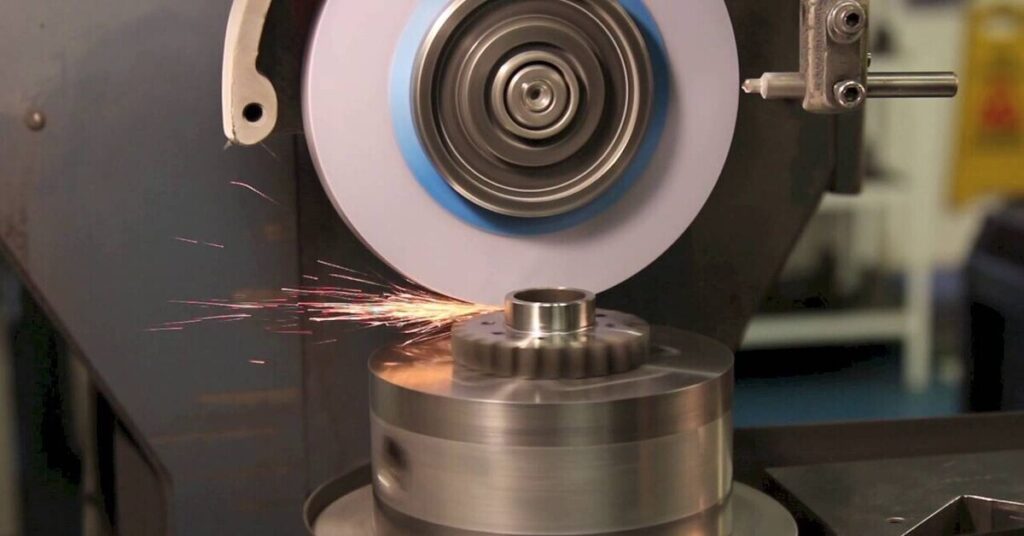
Importance of Ultra Precision Machining in modern manufacturing: Ultra-precision machining plays a crucial role in many industries, including aerospace, medical, automotive, and electronics. It allows for the production of intricate and highly precise parts, which can improve performance, reliability, and efficiency.
A brief overview of high-precision manufacturing techniques: High-precision manufacturing techniques include micro-milling, micro-turning, high-precision grinding, polishing, and ultra-precision laser machining. These techniques enable manufacturers to produce parts with extremely tight tolerances and superior surface finishes.
Plastic CNC Machining: A Comprehensive Overview
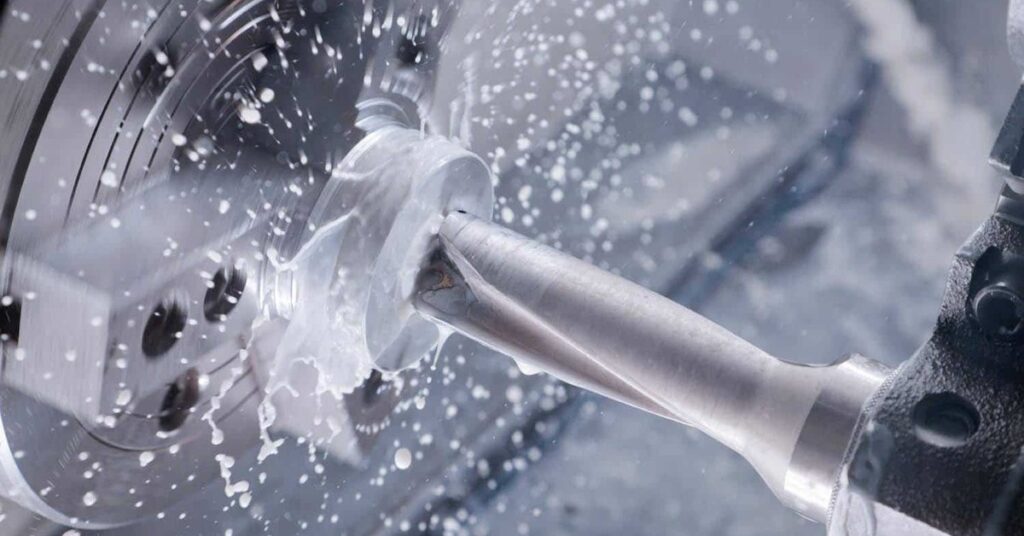
Most product manufacturers often use CNC machining for metallic products more than other materials, including plastics. CNC machining is a standard method in different industries and is highly compatible with various plastic polymers.
Plastic CNC machining involves using automated cutting tools to cut the workpiece into desired shapes. However, you must understand the different plastics for CNC machining and the suitable machining process to determine the suitable one for your project.
This article discusses standard CNC plastic machining, suitable techniques, and various applications. You’ll also learn about the alternatives to plastic CNC machining and when to use plastic for CNC machining. Let’s get to it!
Titanium CNC Machining: Everything You Need to Know
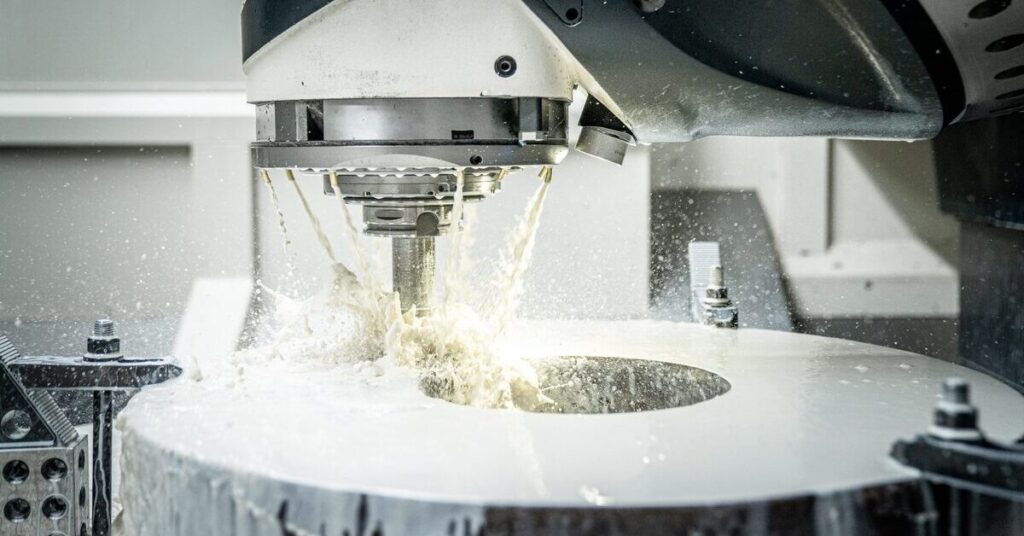
Titanium is one of the most versatile and frequently used CNC machining materials by architects, consumer product designers, and industrial engineers. This lustrous transition metal offers unique properties, including low density, low thermal conductivity, relatively high melting point, and good formability for different applications.
More importantly, many industries create titanium machined parts due to their impressive strength-to-weight ratio and corrosion-resistant properties. This article explores titanium CNC machining, titanium grades for CNC machining, surface finishing treatments, and tips for machining titanium with CNC machines.
Alloy Steel vs. Stainless Steel: A Comprehensive Guide to Choosing the Right Steel
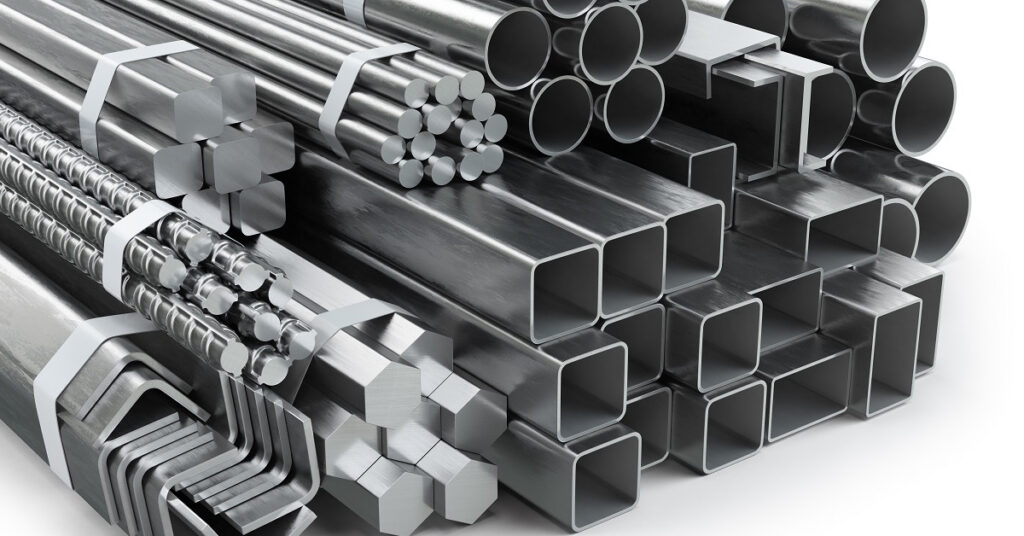
Steel is an essential alloy material used in several industries, from building and construction to the military, because of its fabrication ease, metal strength, customizability, and durability. Alloy steel and stainless steel are the top steel types out of the many available sheets in the market that manufacturers often compare when their intended product requires steel.
However, you can successfully choose the suitable steel amongst these two after understanding their respective properties. This alloy steel vs stainless steel comparison will help you better consider their different properties.
In this guide, we will discuss the differences between alloy steel and stainless steel while examining their various types and applications. Let’s get to it!
Advantages of PEI in CNC Machining: Why It’s the Material of Choice
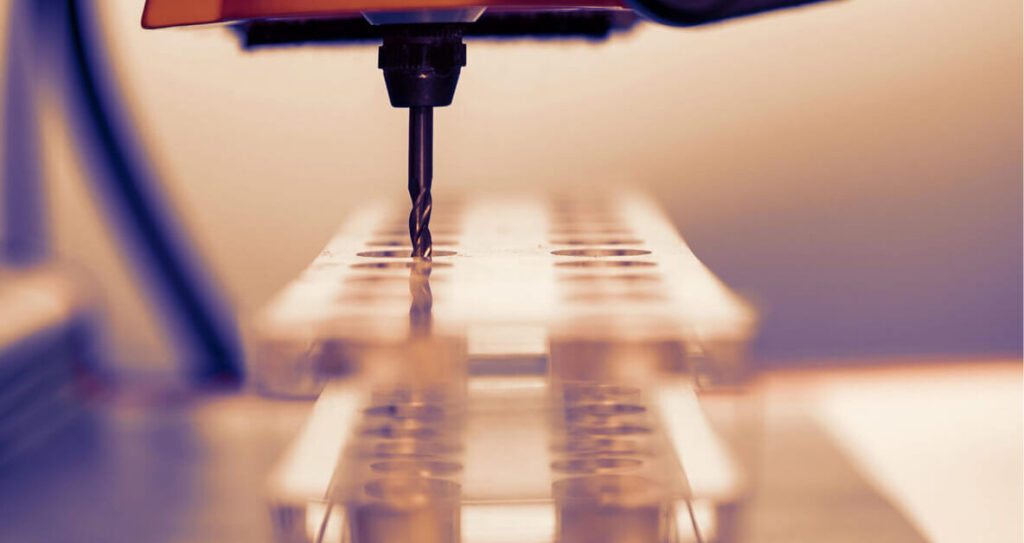
Discover the remarkable properties of Polyetherimide (PEI) in CNC machining and why it’s the material of choice for diverse applications.
This blog post delves into PEI’s unique characteristics, common grades, and its significant advantages in CNC machining.
Learn how industries leverage PEI’s versatility to push the boundaries of innovation and performance.
Motorcycle Parts Customization 101: Mastering CNC Machining
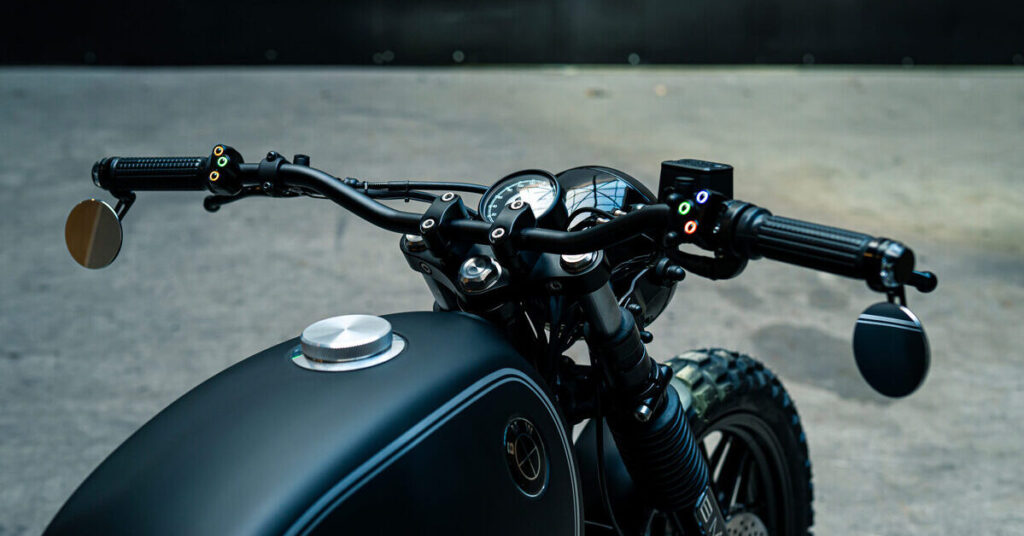
This blog post is an informative guide to customizing motorcycle parts using CNC machining. It covers the advantages of CNC machining for motorcycle parts, popular customization options, suitable materials, and various machining techniques.
The post also gives readers valuable tips on successfully managing their custom CNC machining project, from selecting the right shop to effective communication and time management.
The blog concludes by encouraging readers to explore the world of motorcycle customization using CNC machining.
POM CNC Machining: The Perfect Solution for High-Quality Custom Parts
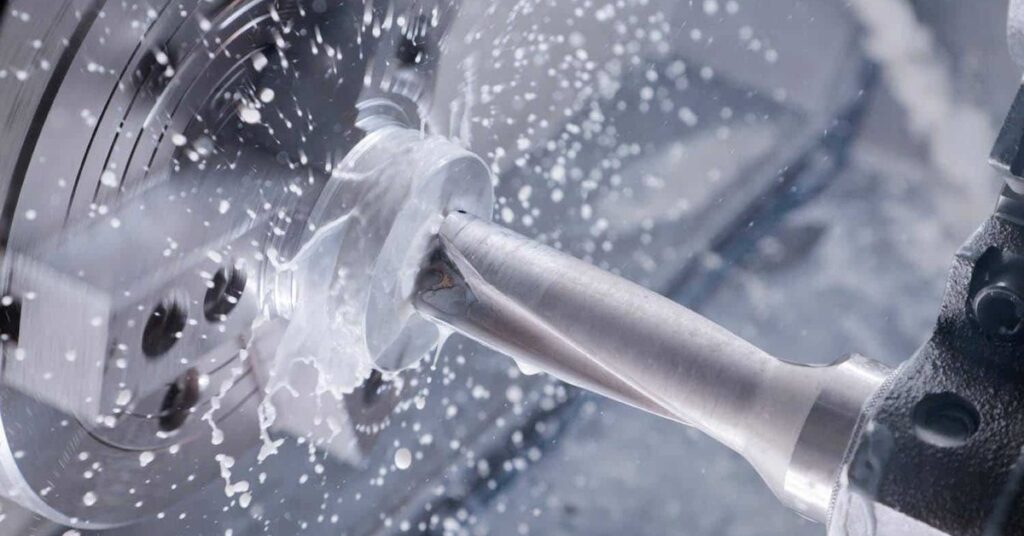
Looking for high-quality custom parts? POM CNC machining may be the answer.
CNC machining POM offers precision, tight tolerances, and Consistent dimensions, making it ideal for large production runs. Our blog showcases its versatility across different industries and provides insights into spindle speed selection for successful POM CNC manufacturing.
Discover the unique properties of POM, such as excellent wear resistance and a low-friction surface, and how they make it an ideal choice for various industrial applications. Learn why appropriate spindle speed selection is crucial for success and why CNC machining POM is the perfect solution for custom parts needs.
STL to STEP: How to Convert STL Files to STEP Format
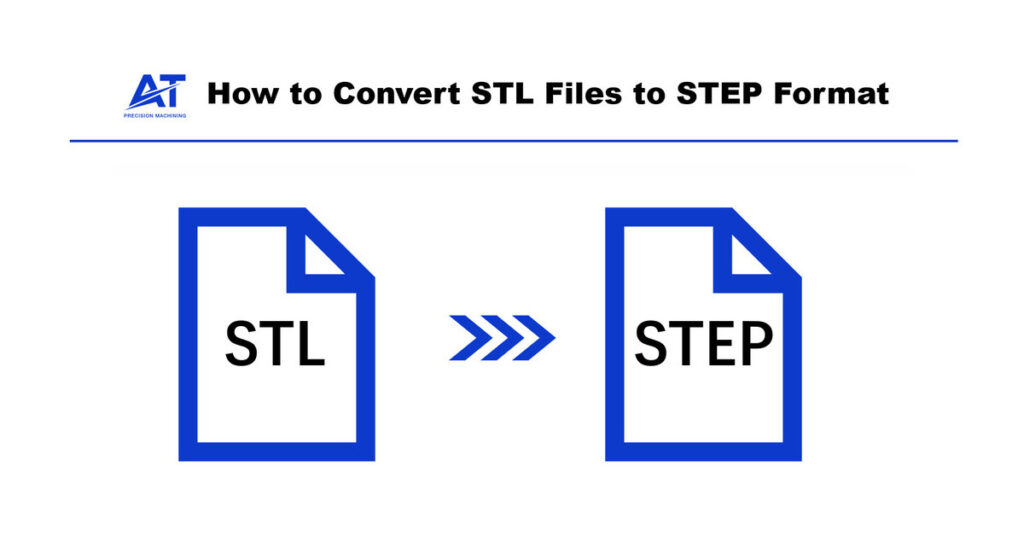
The manufacturing industry is familiar with many file formats, of which STL and STEP are among the most used. Manufacturers commonly use STL files for 3D printing and STEP files for CAD and engineering applications. Knowing how to convert STL to STEP file format is essential for dimensional modifications or design.
Various software tools are available with a download link or access online. Most of these software are more intuitive and relatively easy to use. An excellent example of such is FreeCAD. It allows the easier creation of higher-quality solids than the original mesh file.
This article provides detailed information on STL and STEP files. You will also learn how to convert STL to STEP files with practical tips on the best converters and programs to use. Let’s get to it!
Get the PEEK Advantage: A Comprehensive Look at PEEK Material & Properties
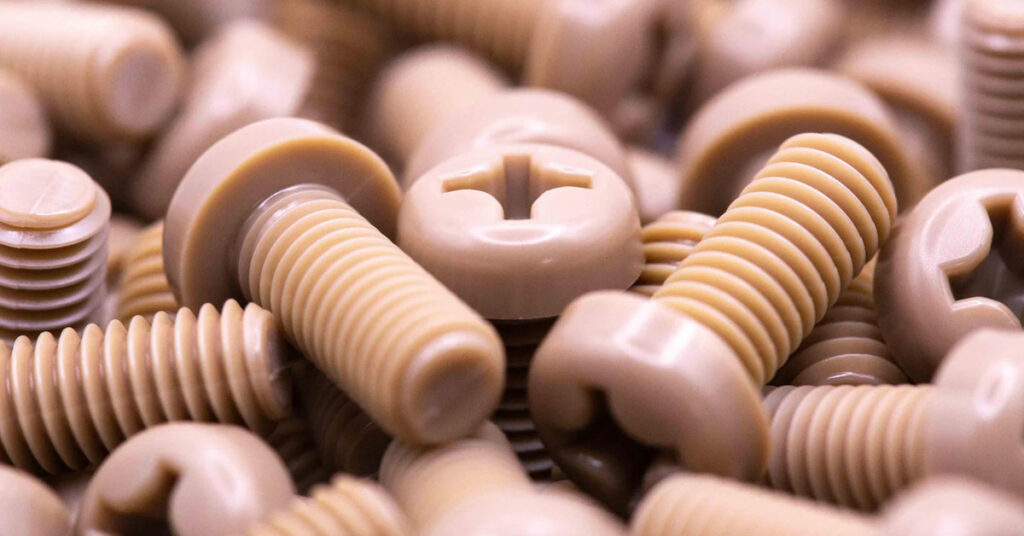
This blog post provides a comprehensive overview of Polyetheretherketone (PEEK) material and its unique properties.
From its exceptional mechanical, thermal, and chemical properties to its ability to perform well in harsh environments and demanding applications, PEEK has become a popular choice in various industries. The post also covers the different PEEK variants and their properties, top processing methods, and a comparison with other materials.
Whether you are looking to learn more about PEEK material or choose the right material for your project, this post is a valuable resource for anyone interested in high-performance engineering thermoplastics.
Low-Volume Manufacturing: A Comprehensive Guide
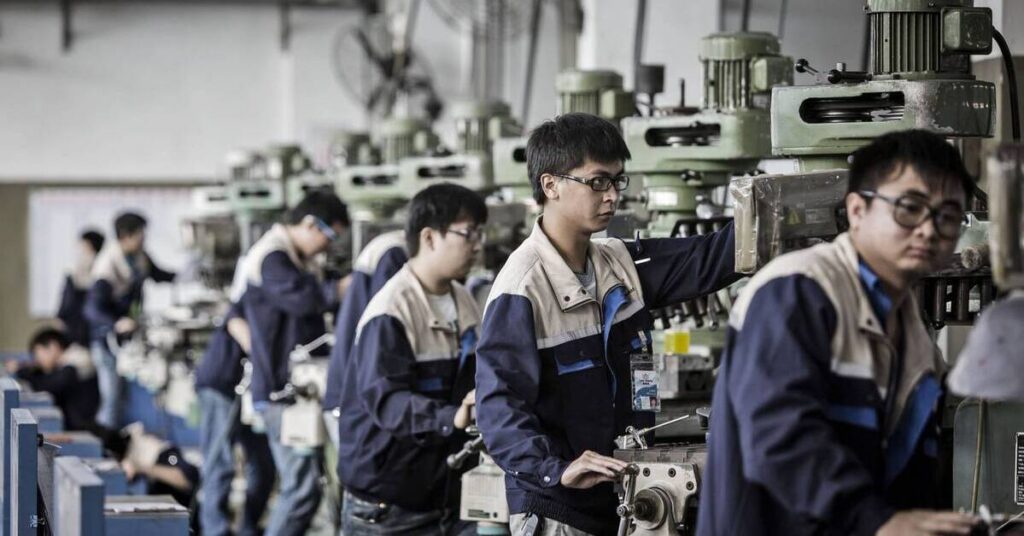
As the product design world evolves, product developers and manufacturers encounter risks and challenges as they launch new products to market. However, innovative companies now use low volume manufacturing to mitigate the occurrence of production risks and uncertainties.
It usually involves manufacturing products in small batches between 10 units to 100,000. Low-volume manufacturing offers several benefits through the various stages of product development, ensuring the cost-effective production of high-quality parts.
This article provides a detailed overview of low-volume manufacturing and how to use this production technique for successful product launches while mitigating risks. You’ll also learn more about the advantages of low-volume manufacturing and find out if it’s the right technique for you. Let’s dive in!
CNC Machining vs. 3D Printing: Which One Is Best for Your Project?
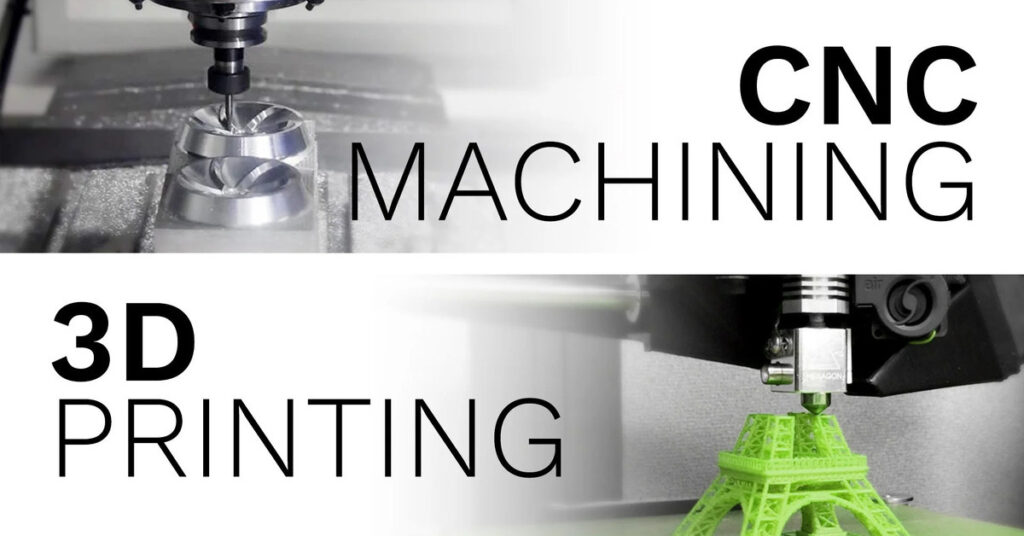
CNC machining and 3D printing are versatile manufacturing technologies among industries’ many widely used processes. They exhibit high compatibility with various materials and are suitable for rapid prototyping and low-volume production.
However, these processes might not be ideal for all production needs. Therefore, understanding the CNC machining vs. 3D printing comparison will help you determine the one that fits your production needs best.
This article explores the CNC and 3D printing processes, including their similarities and differences. You will also get helpful tips for choosing the ideal technique for your projects. Let’s get to it!
Choosing the Ideal Nylon Grade for Your CNC Machining Project
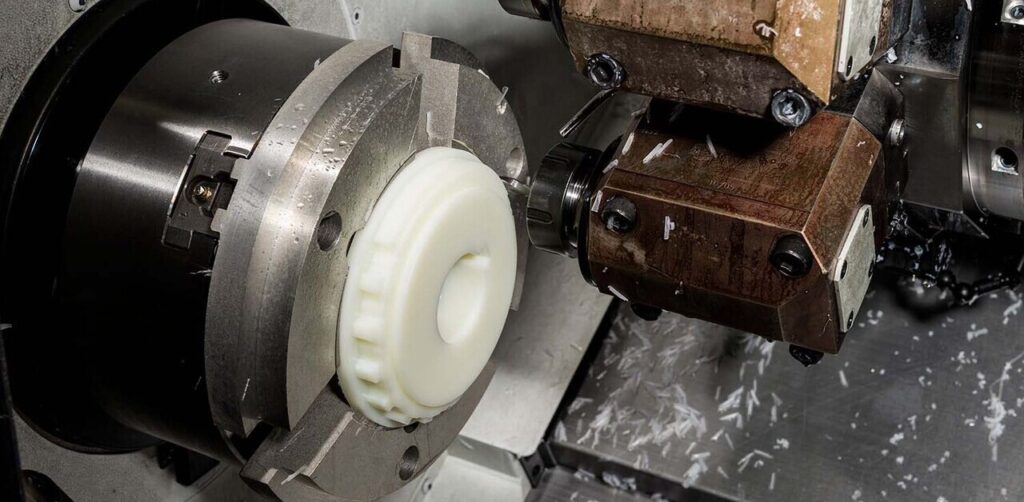
This blog delves into the process of selecting the perfect nylon grade for your CNC machining project.
We discuss common nylon grades, their properties, and key factors to consider when making a decision.
Additionally, the blog highlights alternative manufacturing methods and how to achieve optimal performance, cost-efficiency, and product longevity with the right nylon grade.
Black Anodized Aluminum: The Ultimate Guide to Stunning and Durable Finishes
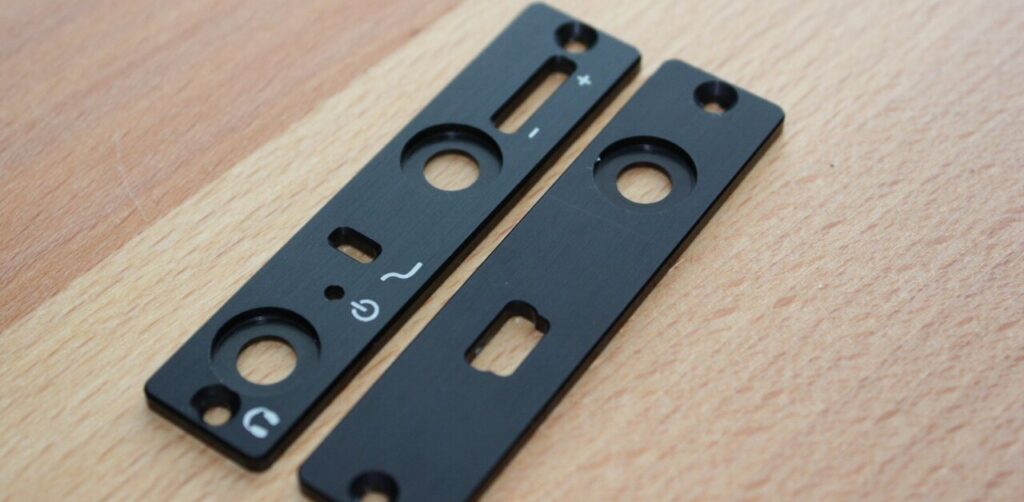
This ultimate guide to black anodized aluminum offers a detailed look into the anodizing process, its benefits, and its applications across various industries. We delve into the key steps of black anodizing aluminum alloys, types of anodizing, and factors to consider for optimal results.
The guide also provides insights into the chemistry behind the process, comparisons with other surface treatments, and tips for overcoming common challenges.
By understanding the intricacies of black anodizing, you can elevate the performance and aesthetic appeal of your aluminum products, ensuring a stunning and durable finish.
6061 Aluminium Alloy: Everything You Need to Know
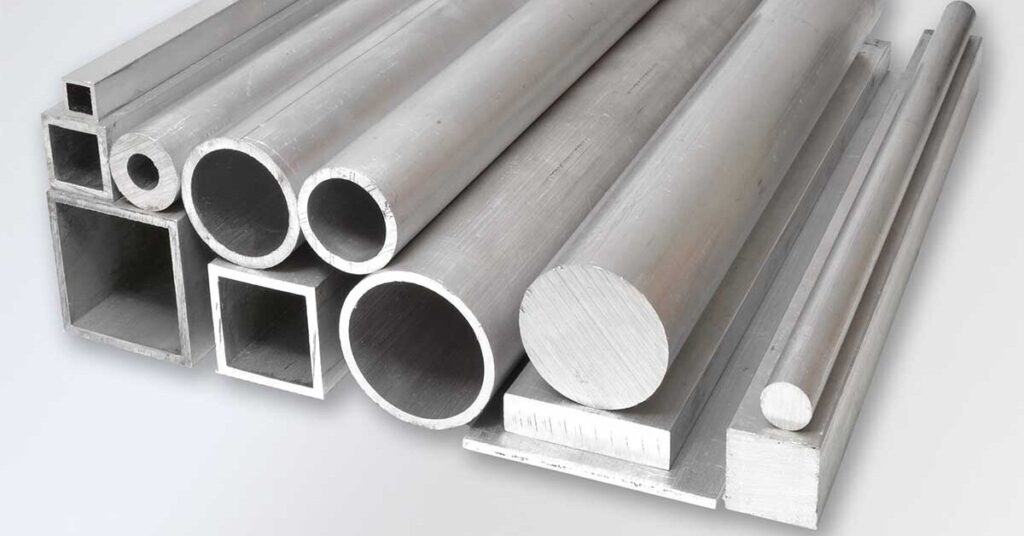
Aluminum alloys are crucial in nearly all modern industrial innovations and production processes. These alloys are readily available and have a wide range of uses because each contains a blend of two or more metallic elements giving them refined material properties.
The 6061 aluminum alloy is a versatile and widely used grade for various industry applications. The alloying elements in the 6061 aluminum alloy offer unique properties, including good workability, incredible strength, electrical conductivity, thermal conductivity, and corrosion resistance.
This article discusses 6061 aluminum alloy composition, its attributes, properties, and typical applications. You’ll also learn helpful tips on choosing the suitable alloy for your project. Let’s get to it!
Industrial Ceramics 101: Which Type Is Best for Your Project?
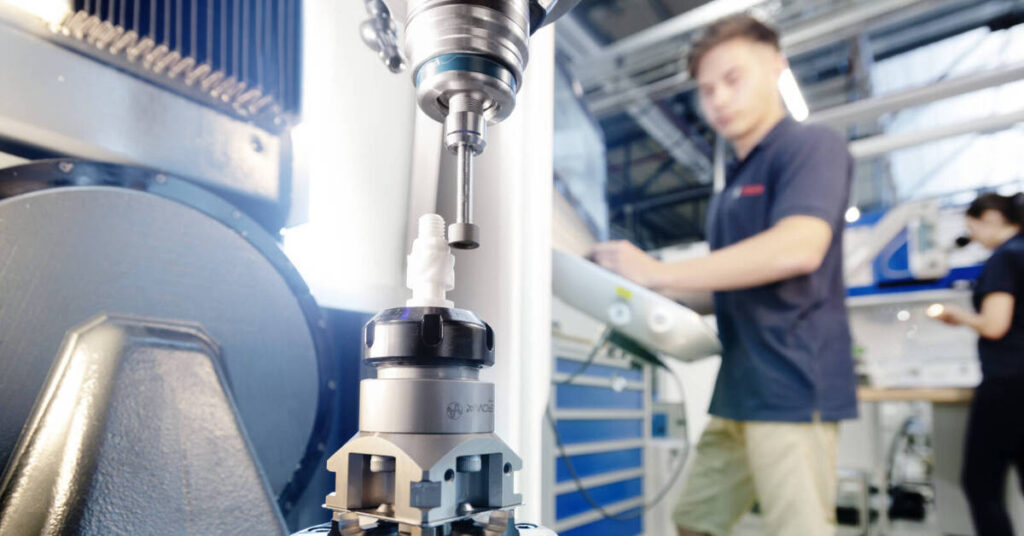
Thanks to their unique properties, such as thermal stability, strength, and durability, ceramics have been used for industrial applications for centuries.
Choosing the correct type of industrial ceramic for your project can help enhance efficiency, reduce costs, and ensure safety. In this blog post, we will explore the different types of industrial ceramics and provide a step-by-step guide to selecting the best ceramic material for your project based on factors such as operating conditions, performance characteristics, and production feasibility.
Get the Most Out of Your Components with DLC Coating
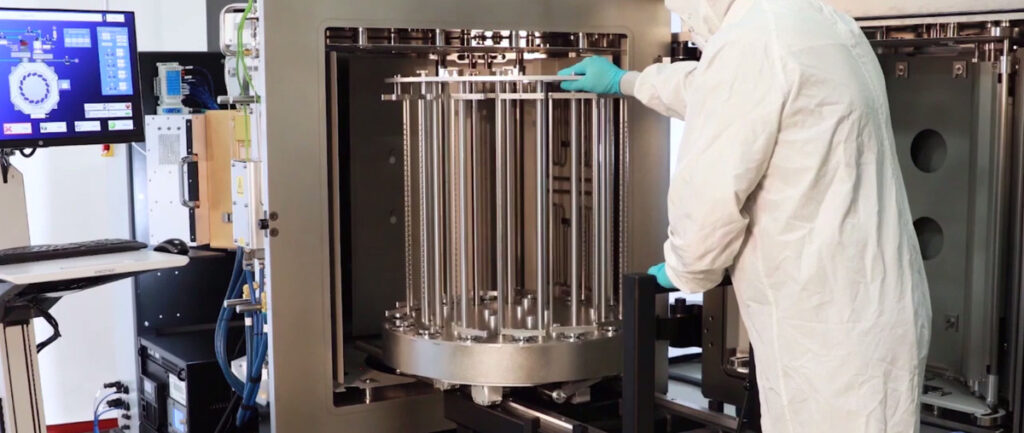
Diamond-like carbon (DLC) coatings have gained increasing attention in recent years due to their unique properties, including high hardness, low friction, and excellent wear resistance. These coatings are applied using a variety of methods, including physical vapor deposition (PVD) and chemical vapor deposition (CVD), and can be used on a range of materials, including metals, polymers, and ceramics.
This blog explores the benefits of DLC coatings, including improved performance and durability, reduced friction, enhanced corrosion resistance, and increased lifespan of parts and components. We also delve into some of the key industries that are embracing DLC coatings, including automotive, aerospace, medical, and industrial applications.
Whether you’re a manufacturer looking to improve the performance and durability of your products or a consumer looking for better quality and longer-lasting products, this blog will provide valuable insights into the benefits of DLC coatings.
Ceramic CNC Machining Overview
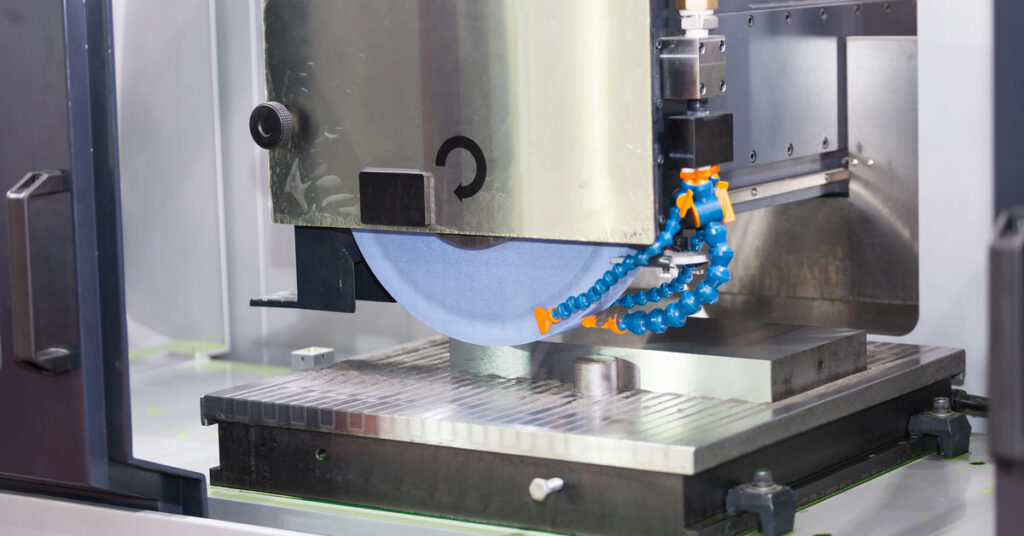
CNC machining of ceramics involves using computer numerical control technology to shape and produce intricate ceramic parts.
The importance of CNC machining of ceramics in various industries stems from its high durability, wear resistance, and other valuable qualities, and CNC machining technology can make ceramic parts have better accuracy and a wider range of applications.
This article provides an overview of the ceramic machining process, its far-reaching applications, and more. Continue reading to further explore the topic.
Get the Perfect Finish: A Guide to Metal Surface Finishing
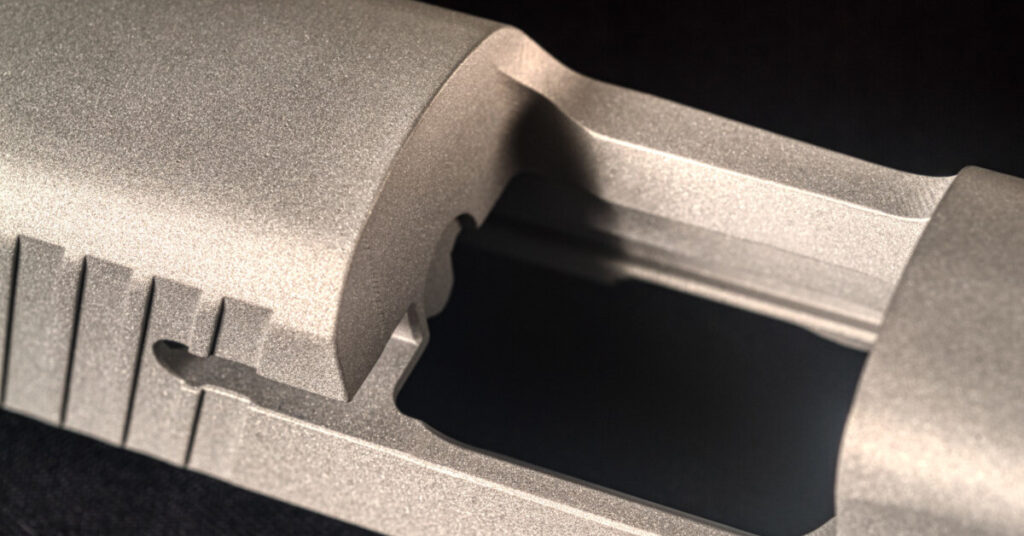
Are you seeking to enhance the performance or appearance of your metal components?
Metal surface finishing is an essential part of the manufacturing process. It helps to protect metals from corrosion and can even add aesthetic appeal. From standard methods like bead blast and powder coating to more specialized procedures such as anodizing and plating, metal surface finishing can provide various benefits depending on the application.
In this blog post, we’ll explore the benefits and common types of metal surface finishing. By the end of this post, you will better understand how metal surface finishing can help protect and enhance your metal parts. So let’s get started!
Heat Sink Design: Basics, Principle, and Practical Tips
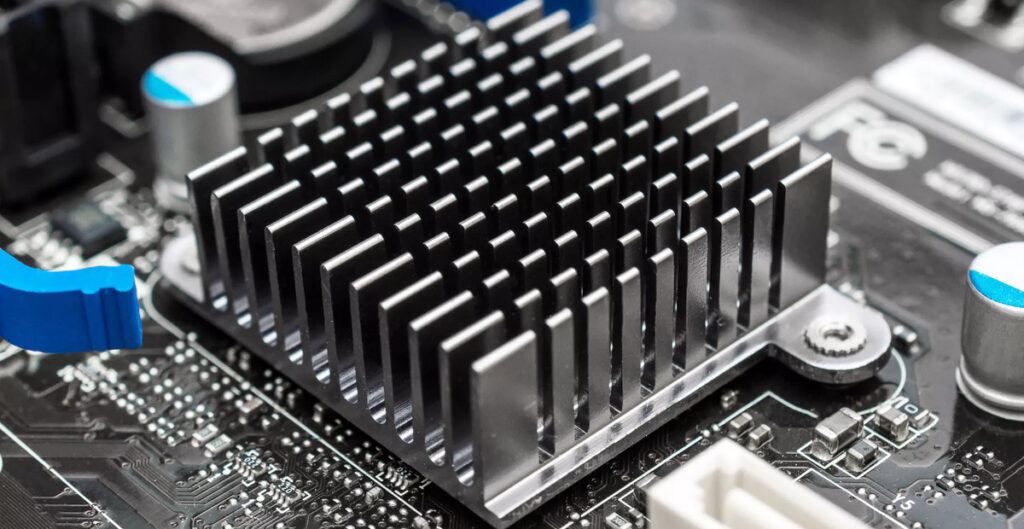
A heat sink is an essential component for every electronic device, ranging from computer sets to television, LED lighting, etc. The heat sink is a thermally conductive device with a high ability to absorb and transfer heat from components preventing them from overheating or damaging.
Heat sink design is essential when considering heat dissipation within a device and ensuring its longevity. Optimizing the heat sink design maximizes the surface area in contact with the cooling medium. As a result, thermal resistance and heat dissipation can be further improved.
This article discusses the basics of heat sink design, including its types and applications. You’ll also learn effective tips for getting the best when manufacturing heat sinks.
Medical CNC Machining: Everything You Need to Know
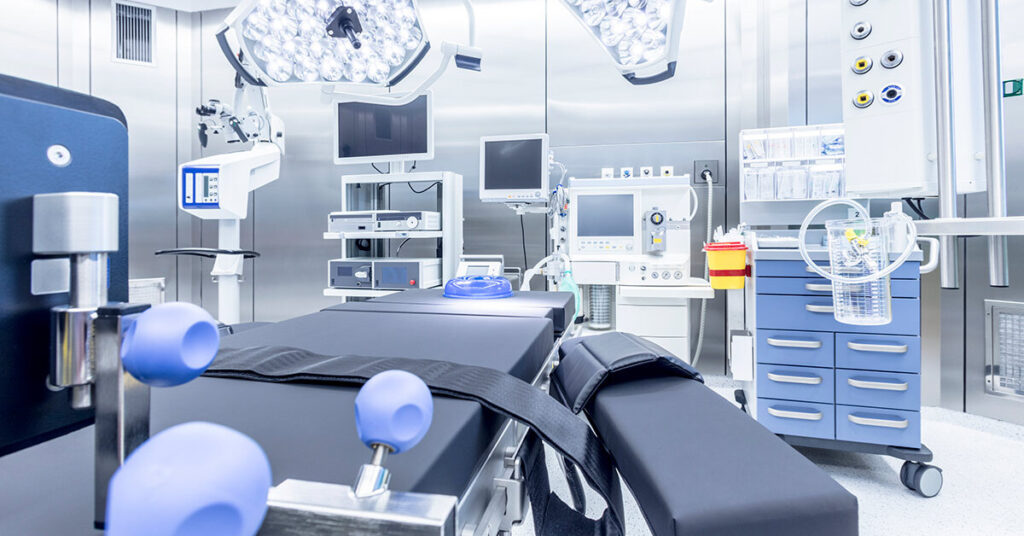
The medical manufacturing industry has witnessed high demand for quality components with tight tolerances. Most of these products are expected to meet the industry’s required quality and safety standards and are typically manufactured quickly. Thus, product designers and manufacturers adopt medical CNC machining to meet these standards.
CNC machining’s versatility and high compatibility with various materials make it the ideal manufacturing option for the medical industry. You can effectively produce medical components with utmost precision and accuracy, ensuring the safety of patients and reducing the risk of errors.
This article explores the medical industry’s use of CNC machining, the application of medical CNC machined parts, and tips for getting the best medical CNC machined parts.
From Guns to Warships: Applications of CNC Machining in the Defense Industry
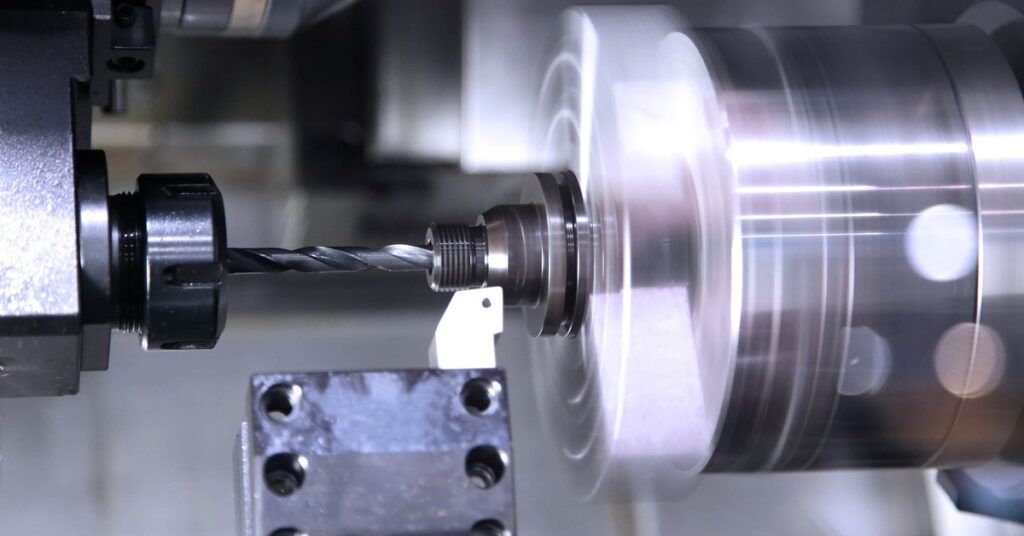
Discover how CNC machining is utilized in the defense industry to create precise and reliable components for everything from guns to warships.
This article highlights the various applications of CNC machining in the defense industry. It explains how it helps to create critical components for military equipment that meet strict tolerances and standards.
Learn how CNC produces firearm components, aircraft and spacecraft parts, radar and electronic systems, and warship components. Gain insight into the benefits of CNC technology in producing military equipment and how it contributes to the safety and success of military operations.
CNC Machining Tolerances: Overview, Benefits, and Tips
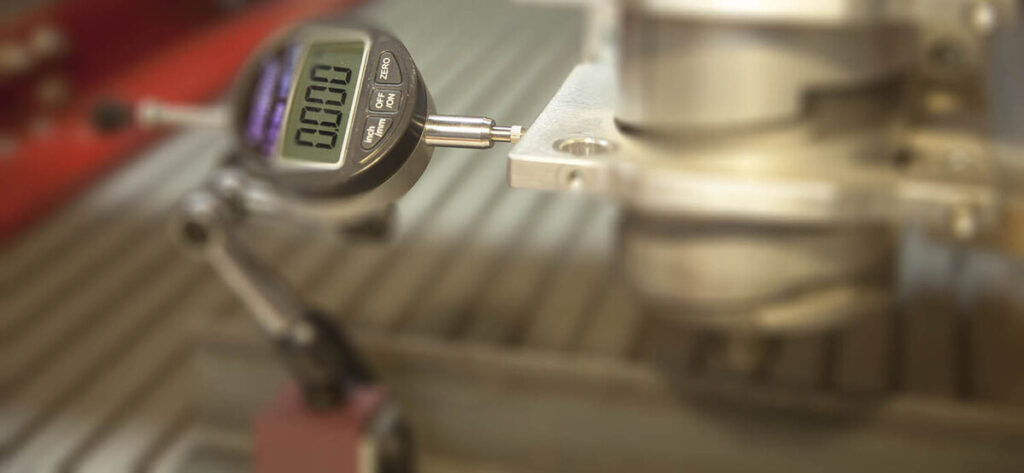
CNC machining has significantly improved manufacturing results as part of the emergence of Industry 4.0. It utilizes various fabrication methods and advanced machines to create superior quality and high-precision components. These CNC machines help achieve the highest levels of accuracy and tight CNC machining tolerances.
However, CNC turning and milling parts with the tightest tolerances are often expensive and time-consuming. Thus, it is essential to specify the appropriate tolerances that a part requires when machining.
This article discusses every essential aspect of CNC machining tolerances, including the types, benefits, and how to determine the ideal tolerance for your parts. Let’s get to it!
Measurement of Nitriding Layer for CNC Machined Parts
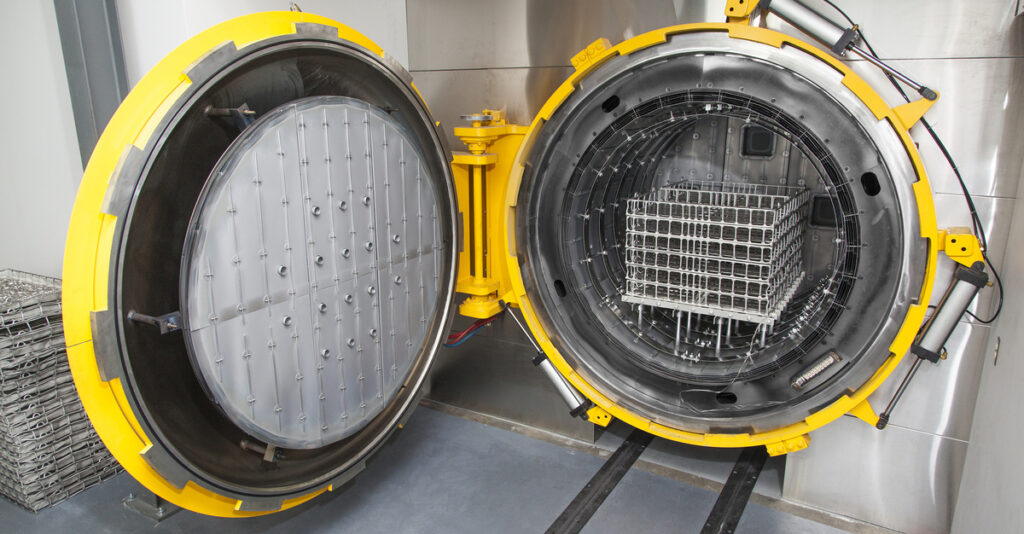
If you’re interested in enhancing the wear resistance and fatigue strength of your CNC machined parts, nitriding may be a viable option. However, measuring the nitriding layer is critical to achieving the desired properties.
In this blog, we will discuss the different methods for measuring the nitriding layer on CNC machined parts, including microhardness testing, surface roughness testing, and metallographic examination. We will also explore the advantages and disadvantages of each method to help you choose the best approach for your specific application.
Additionally, we’ll delve into the differences between nitriding and carburizing, as well as the advantages of testing the nitriding layer by metallographic examination. By the end of this blog, you’ll better understand the importance of measuring the nitriding layer for CNC machined parts and how to select the most suitable method for your needs.
From Prototyping to Production: CNC Machining Solutions for Automotive Parts Manufacturing
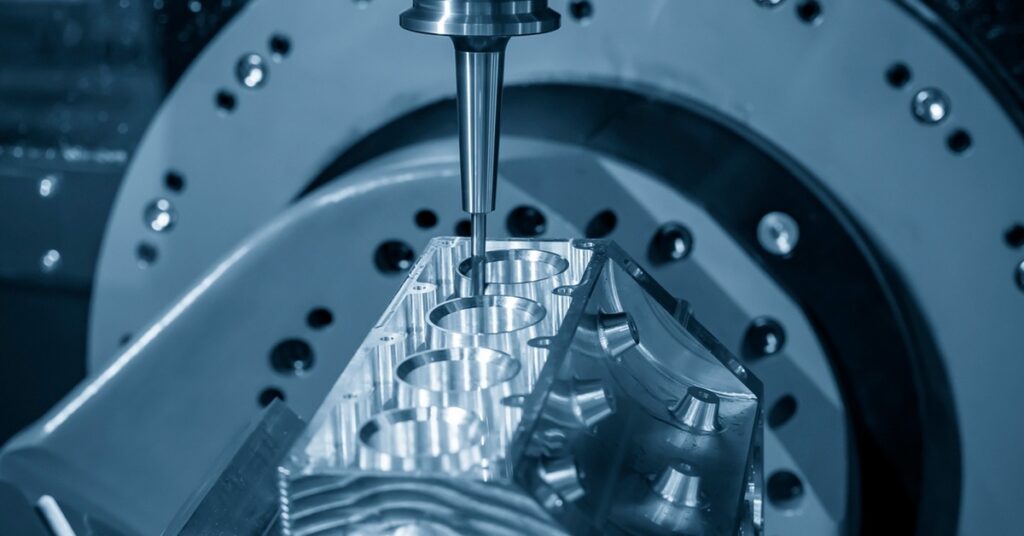
In the automotive industry, CNC machining has become an increasingly popular solution for producing high-quality and precise parts.
From prototyping to mass production, CNC machining offers a range of benefits for automotive manufacturers, including flexibility in producing small quantities, the ability to produce complex geometries without the need for expensive tooling, and efficient mass production of parts.
In this blog, we explore the application of CNC machining in automotive parts manufacturing, including the types of CNC machines used, the benefits of using CNC machining, quality control measures in place, and Common materials for auto cnc machining. We also showcase some experience with automotive parts produced using CNC machining technology.
Black Oxide Coating Finishing Ultimate Guide In CNC Machining
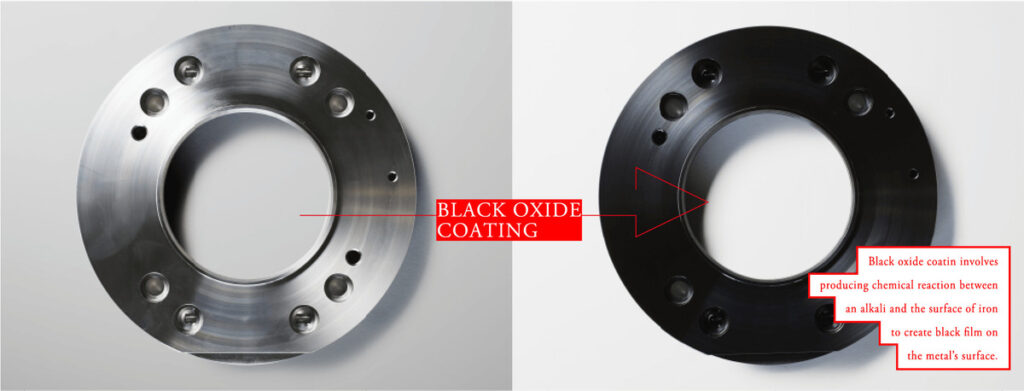
Welcome to AT-Machining’s ultimate guide to Black Oxide Coating Finishing in CNC machining! Our blog is a comprehensive resource for anyone interested in learning more about this versatile and affordable surface finish option.
This blog discover the process of applying black oxide finish, explore different types available, advantages and disadvantages, common defects and solutions, performance tests, and factors to consider. Get insights into hot black oxide, commonly used salt baths, and materials. Our blog helps determine if black oxide is the right finish for precision machined parts in any industry.
As a CNC machining service provider based in China, AT-Machining has the expertise and experience to handle your precision machining needs from start to finish!